Success Story
Industry: Quarrying, Mining & Construction
Application: Conveyor Application for a Quarrying & Mining Company
Cost Savings: $15,418
Introduction
An Quarrying & Mining Company were having reliability issues with a conveyor application. Bearing inserts were operating in a very harsh environment, exposed to water and abrasives particles. Located just 5 meters above the ground, inspection and maintenance tasks were severely problematic creating difficulty predicting premature failures. NSK assessed the situation and proposed the use of Molded-Oil inserts. The solution increased bearing life by 9 times.
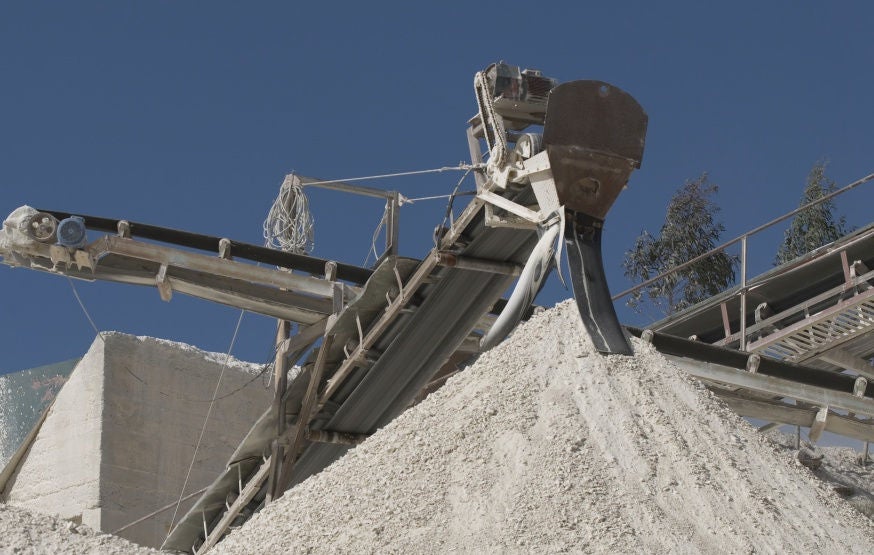
- Conveyor Application

- Molded-Oil Bearings
Key Facts
- Conveyor application with remote access (5m above ground) and difficult maintenance
- Harsh environment, exposed to water and abrasive particles
- Regular failures with difficult replacement procedure and large downtime costs
- NSK Molded-Oil bearings proposed which are excellent for remote applications
- Additional benefits of improved sealing with flinger, lip seal and molded oil providing a barrier to contamination ingress
- Bearing lifetime significantly increased from every 2 months to 19 months
Value Proposals
- NSK engineers reviewed the application and discovered that the main problems were contamination, water and maintenance difficulties due to the remote location
- NSK Molded-Oil bearing inserts were proposed which do not need to be re-lubricated and have better sealing due to the barrier created by the molded oil polymer
- The bearings were trial fitted to the conveyor and lifetime was increased from 2 months to 19 months
- Customer benefited from increased productivity and reduced maintenance costs
Product Features
- Molded-Oil inserts (with solid lubricant)
- Ideal for remote applications
- Martensitic stainless steel
- Integral Flinger seal and Nitrile rubber seals
- Bore size 20mm – 40mm
- Corrosion resistance
- Resistant to contamination increasing operating life
- No need for re-lubrication
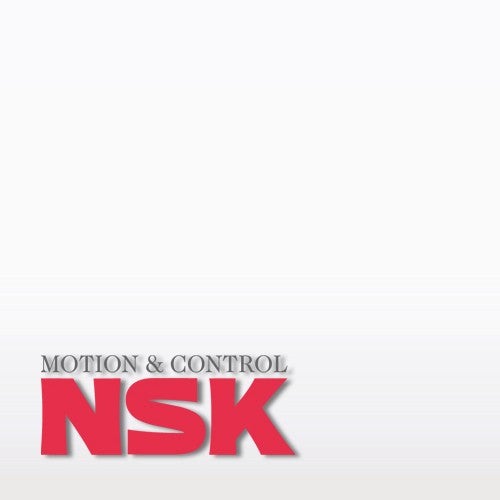
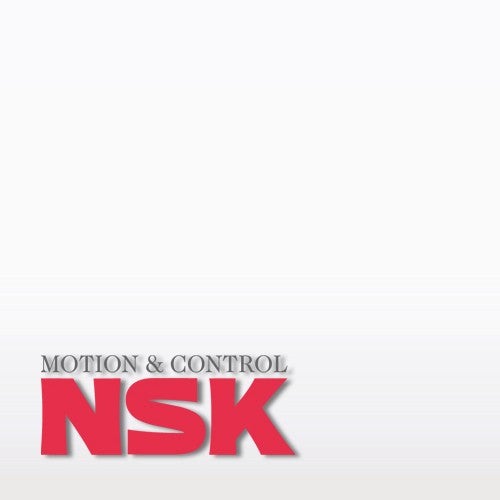
Cost Saving Breakdown
Before | Cost p.a. | NSK Solution | Cost p.a. | |
---|---|---|---|---|
Bearing Costs: Replacements per year × employees time × $32/h | $579 | Bearing Costs: Less than 1 replacement per year × employees time ×$32/h | $67 | |
Engineering Costs: Downtime costs: 250ton/h × $7.5/ton × time × replacements per year | $16,875 | Engineering Costs: Downtime costs: 250ton/h × $7.5/ton × time × replacements per year | $1,969 | |
Costs of lost production: Life: 2 months approximately (440h) | Costs of lost production: Life: 19 months approximately (4140h) | |||
Total Costs | $17,454 | $2,036 |
Reference:SS-E-7022
Share