Success Story
Industry: Textile and Leather
Application: Belt washer
Cost Savings: $10,102
Introduction
An international manufacturer of technical textile products was experiencing frequent bearing failure on a belt wash application. NSK carried out a Bearing Failure Analysis revealing ingress of water and chemicals leading to the bearing failures. NSK was asked to find a solution to this problem. A trail was agreed which resulted in an increase of bearing life.
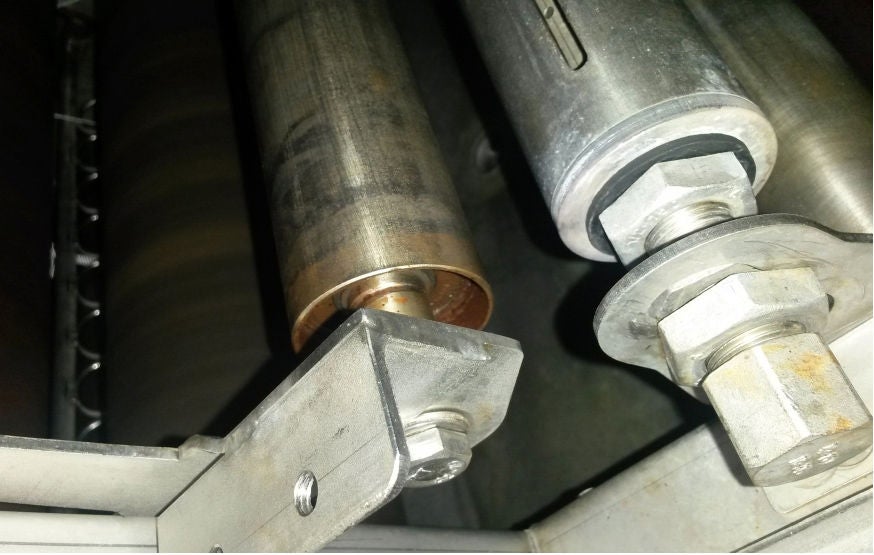
- Belt washing application
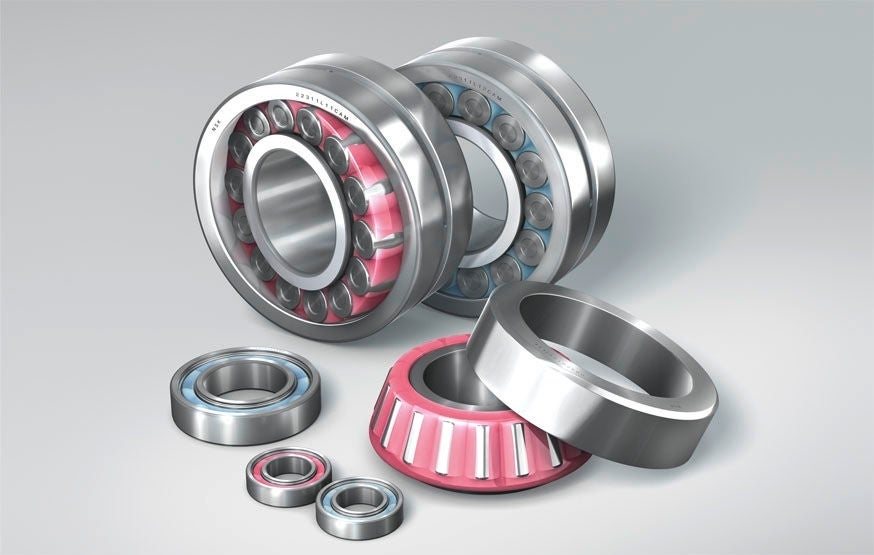
- Molded-Oil Bearing
Key Facts
- High volume belt cleaning and inpregnation line
- Water ingress
- NSK’s solution: replacing standard ball bearing with NSK’s Molded-Oil ball bearing
- No bearing failures for more than 12 months
- Productivity improvement
- Cost saving generated
Value Proposals
- NSK engineering conducted a Bearing Failure Analysis showing ingress of water and chemicals into the bearing
- NSK required to replace the standard ball bearings with ball bearings Molded-Oil
- A trail was agreed which resulted in an increase of bearing life from 3 months to over 12 months
- The customer benefited from increased productivity and reduced maintenance costs
- No need for re-lubrication
Product Features
- Available for high speed applications
- Available in Ball Bearing, Spherical Roller Bearing and Tapered Roller Bearing types
- Rust-proof - Stainless steel for corrosive environments
- Ideal for applications where contact with liquids and chemicals is unavoidable
- Seals made from nitrile rubber
- Contact-seal type available in standard inventory for ball bearings
- Able to minimize oil leakage
- Longer service life
- No need for re-lubrication
- Smooth rotation of rolling elements
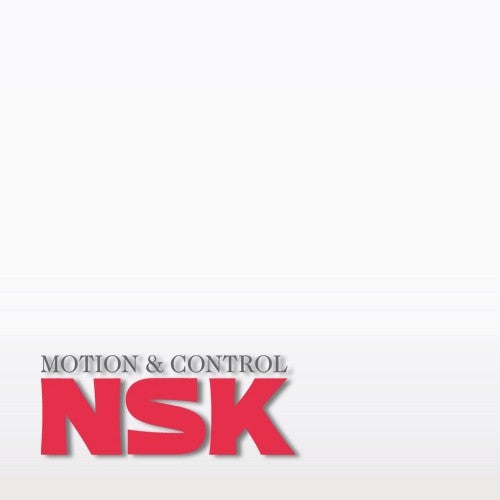
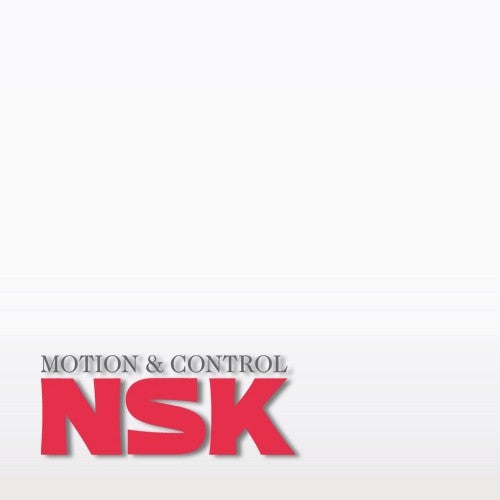
Cost Saving Breakdown
Before | Cost p.a. | NSK Solution | Cost p.a. | |
---|---|---|---|---|
Lubrication Costs: Re-lubrication | € 1.200 | Lubrication Costs: No re-lubrication | € 0 | |
Engineering Costs: Cost of maintenance | € 7.800 | Engineering Costs: No cost of maintenance | € 0 | |
Total Costs | € 9.000 | € 0 |
Reference:SS-E-1015
Share