Success Story
Industry: Quarrying, Mining & Construction
Application: Ceramic Roof Tile Manufacturer
Cost Savings: $5,302
Introduction
A premium roof tile manufacturer was using considerable labor resources on a weekly basis in order to re-grease the ball sliders their handling machinery. This issues was occuring in multiple areas within the factory resulting in high maintenance costs and inconsistent performance leading to lost production.
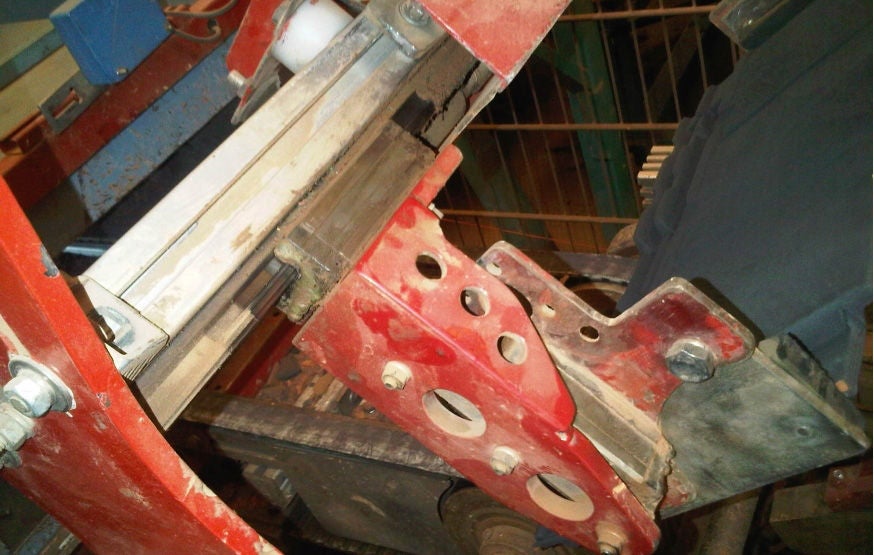
- Slide with solid lubrication K1 system
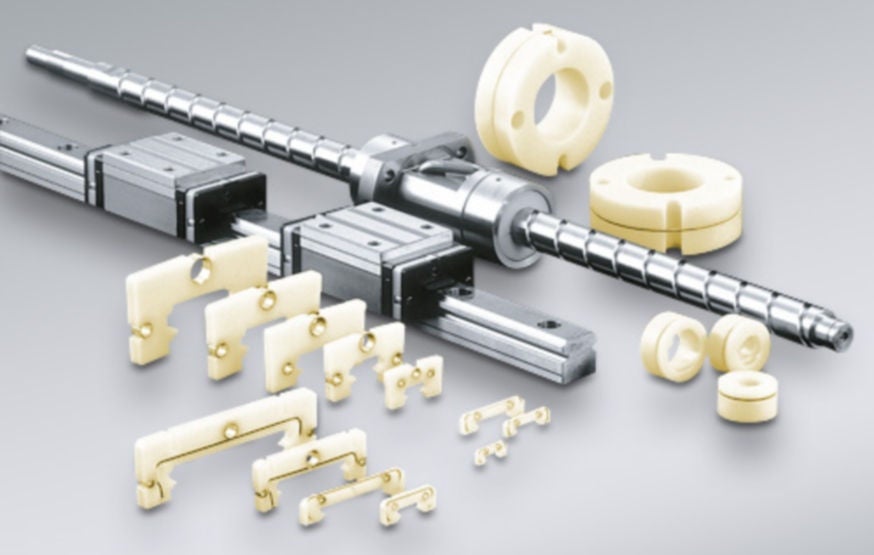
- Internal structure of K1 system
Key Facts
- High maintenance costs due to manual process
- Contamination and dust ingress
- Poor lubrication
- Fixed preload and smooth linear motion requirement
Value Proposals
- Application review highlighted lubrication and sealing needed improving
- Introduced the solid lubrication system K1
- Improved sealing and protection
- Preload maintained longer due to reduced wear
- Reduced running friction resulting in reduced actuator pressure needed for same operation ( 6 to 4 bar)
Product Features
- Long-term, maintenance-free operation
- Available in accordance with the FDA
- Effective sealing function
- Applicable to all the linear guide models
- Regardless of the mounting orientation the operation of K1 units is always guaranteed
- Designed to operate in highly contaminated environments
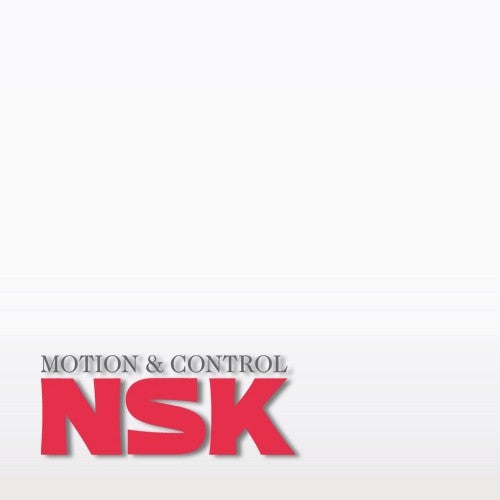
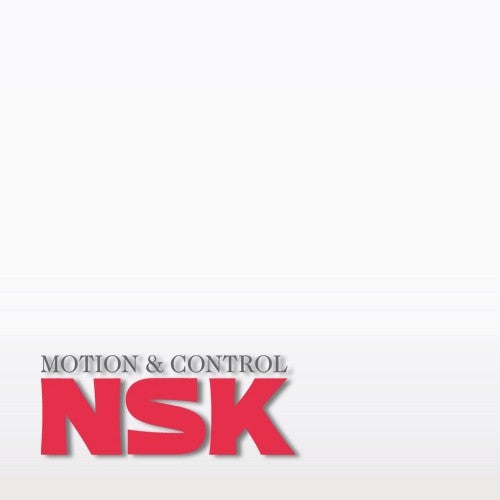
Cost Saving Breakdown
Before | Cost p.a. | NSK Solution | Cost p.a. | |
---|---|---|---|---|
Bearing Costs: $589/ machine x 6 machines | $3,534 | Bearing Costs: $509/ machine x 6 machines | $3,054 | |
Engineering Costs: 52 re-greases x 30min / machine x 6 machines x $32 hour / operation | $5,015 | Engineering Costs: 2 re-greases x 30min / machine x 6 machines x $32 hour / operation | $193 | |
Costs of lost production: 52 re-greases x 30min / machine x 6 machines = 156 hours | Costs of lost production: 2 re-greases x 30min / machine x 6 machines = 6 hours | |||
Total Costs | $8,549 | $3,247 |
Reference:SS-E-7026
Share