Safety Management
NSK’s Approach
The NSK Group has positioned safety as one of its core values. We continuously strive to increase our employees’ safety awareness so that safety will always be their basis for determining the best course of action. We implement various measures based on our Safety Philosophy to protect the safety and health of every employee, and to ensure the safe conduct of everyone in the workplace. Never content with the status quo, we constantly work to further raise the level of safety.
NSK Group’s Safety Philosophy
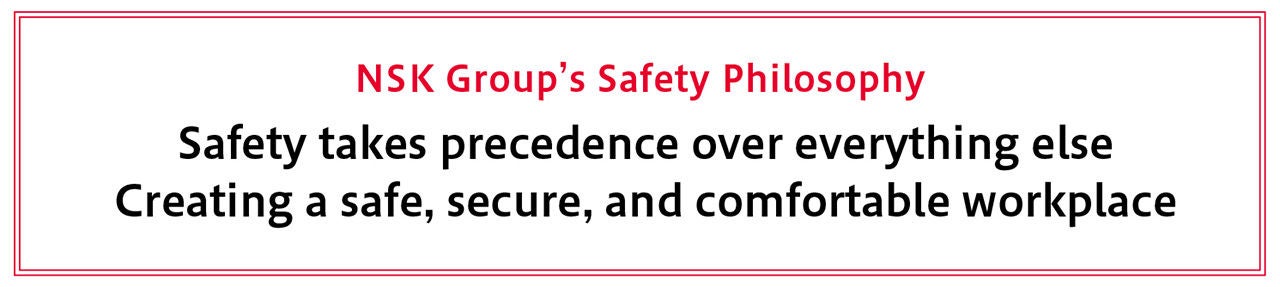
We are committed to protecting the safety and health of all employees and business partners working within the NSK Group. This philosophy expresses our conviction that safety takes precedence over any business concern and that corporate activities depend on safety. It is the foundation of each and every NSK Group employee’s mindset. In all our workplaces worldwide, employees take action on one’s own initiative to ensure safety and to create comfortable environments where they can work with peace of mind.
NSK Group Safety Policy

The NSK Group has three key safety policies. As part of “Foster, spread, and instill a culture of safety,” workshops are held for employees working at production sites to foster a mutually enlightening culture of safety. In addition, to encourage management to exercise felt leadership (leadership that is felt by employees), we have held core value workshops for executive management from FY2020. As part of building “zero accident” workplaces, we are working to prevent serious accidents by reducing the risks of equipment and operations through STOP 6+2 activities and risk assessments. We also work to create a safe working environment for our business partners, such as outsourcing contractors and subcontractors. In addition, we are promoting the “putting preventive and predictive technologies in place” for equipment to detect abnormal signs that could lead to disasters in advance and prevent major breakdowns.
The NSK Group has positioned safety as one of its core values. We continuously strive to increase our employees’ safety awareness so that safety will always be their basis for determining the best course of action. We implement various measures based on our Safety Philosophy to protect the safety and health of every employee, and to ensure the safe conduct of everyone in the workplace. Never content with the status quo, we constantly work to further raise the level of safety.
We are committed to protecting the safety and health of all employees and business partners working within the NSK Group. This philosophy expresses our conviction that safety takes precedence over any business concern and that corporate activities depend on safety. It is the foundation of each and every NSK Group employee’s mindset. In all our workplaces worldwide, employees take action on one’s own initiative to ensure safety and to create comfortable environments where they can work with peace of mind.
The NSK Group has three key safety policies. As part of personnel development, to encourage management to exercise “felt leadership” (leadership that enables workers to understand and “feel” management’s thoughts on safety), we have held core value workshops for executive management since FY2020. In addition, we hold workshops for employees working at production sites to foster an interdependent culture of safety. As part of our hardware countermeasures, we are working to prevent serious accidents by reducing the risks of equipment and operations through STOP 6+2 activities and risk assessments. We also work to create a safe working environment for our business partners, including outsourcing contractors and subcontractors. In the area of compliance, we provide workers with personal protective equipment and implement new measures to prevent occupational injuries and accidents, while also working hard to ensure compliance with relevant laws, regulations, and work procedures. By actively communicating about these measures, we collect information from other companies and relevant organizations and promote new NSK standards.
NSK Group Safety Philosophy
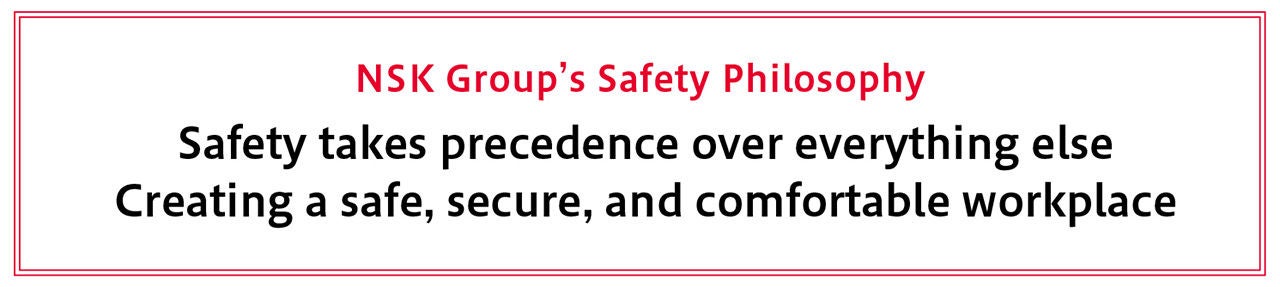
NSK Group Safety Policy
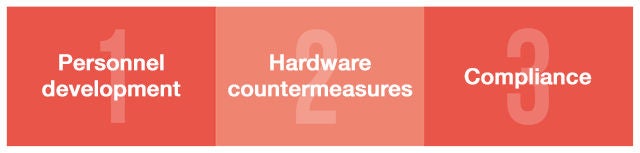
System
◆Organizational Structure for Safety Management
The NSK Group operates a global safety management structure headed by the CEO. Under this structure, safety management activities are communicated from the EHS Promotion Office at the Manufacturing Strategy Division HQ to NSK Group companies through the regional headquarters.
Safety issues facing specific regions are addressed by the EHS Committee the highest safety management decision-making body (attended by the Manufacturing Strategy Division HQ head, plant heads, and executive officers of each business division HQ). The committee determines annual policy and holds discussions on the progress made on these issues four times a year. In conjunction with the Global EHS Managers Meeting (attended by EHS managers from each region), these two bodies hold meetings to discuss issues and share information on initiatives.
Global EHS Operating Structure
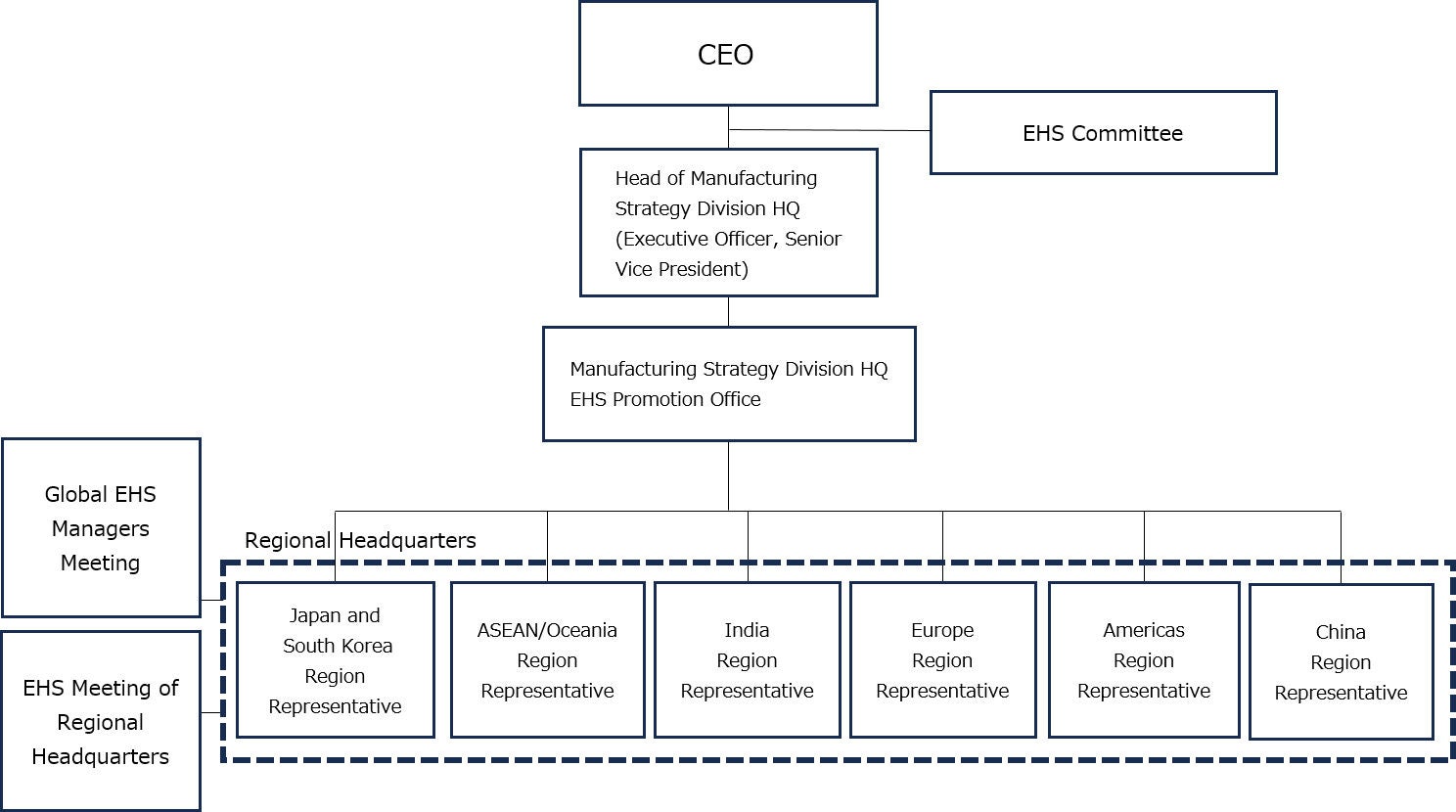
Safety Management System
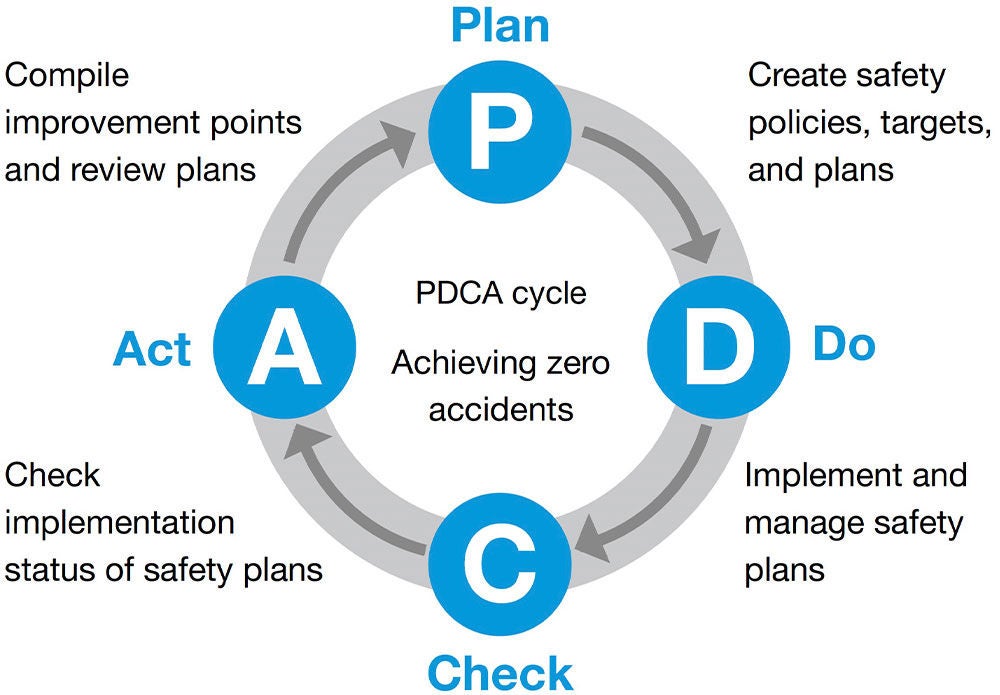
In Japan, company and union representatives participate in the NSK Central Safety and Health Council and the Safety and Health Committee, where they discuss and analyze occupational accidents and share insights on how to further enhance safety measures.
◆Occupational Health and Safety Management System
All NSK Group production sites have obtained external certification for ISO 45001, the international standard for occupational health and safety management systems. In addition, third-party management audits and internal audits by qualified personnel are carried out annually to enhance the effectiveness of the management structure and to continuously improve our activities in order to enhance the level of safety.
Targets and Performance
◆Mid-Term Management Plan 2026 (MTP2026) Targets, with Targets and Performance for Each Fiscal Year
Policy | Personnel development | Hardware countermeasures | Compliance | |
---|---|---|---|---|
MTP2026 | Targets |
|
|
|
FY2023 | Targets |
|
|
|
Performance |
|
|
| |
FY2024 | Targets |
|
|
|
◆Lost Time Injury Frequency Rate Target and Performance
MTP2026 Target | FY2023 Performance |
---|---|
0.10 | 0.28 |
Note: Lost time injury frequency rate = Number of workplace accidents resulting in one or more days of work absence / total actual working hours × 1,000,000
The global lost time injury frequency rate including the discontinued operations (steering business) was 0.24.
Occupational Safety Measures
The NSK Group employs two approaches to raise individual safety awareness: ongoing activities to increase safety awareness, and initiatives to give people more time to think about safety. Kiken Yochi (hazard prediction) Training (KYT), communication of near-miss incidents, and the safety practice of pointing and calling are implemented at workplaces on an ongoing basis as continuous activities to increase safety awareness. KYT is intended to prevent workers from getting stuck in unconscious routines. Past accidents and near-miss incidents at each workplace are compiled into a booklet, and everyone recites them in unison at morning briefings and other occasions. Our initiatives to give people more time to think about safety include “Look Across Activities,” “Core Value Contact,” and group activities related to safety. In these group activities, safety-related themes are set twice a year for sites in Japan, and improvement activities are carried out with the participation of all employees. Awards are given for outstanding activities.
◆Personnel Development
Fostering a Culture of Safety (NSK Safety Culture Workshops)
As part of its efforts to foster a culture of safety, NSK conducts safety culture workshops. These workshops involve an initial safety culture questionnaire given to all employees at each production site to determine a safety culture baseline and to analyze the strengths and weaknesses of the organizational structure, leadership, and business operations. Next, employee interviews and site observations are carried out to identify suitable methods for improving the situation on the ground. A two-day workshop with all department heads is then held to formulate and implement an action plan to boost the level of the safety culture. Sites with a high level of independent or interdependent safety culture tend to have lower rates of occupational accidents, and we believe that ongoing initiatives are required to maintain and improve safety culture levels.
Following an implementation when the action plan formulated during the workshop is carried out and safety awareness is promoted among employees at all levels, a second safety culture questionnaire survey is conducted. The second questionnaire is used to determine whether the level of safety culture has risen and to reflect on the strengths, weaknesses, and effectiveness of the action plans to further foster a culture of safety.
The NSK Group will continue to promote these activities in and outside of Japan with the aim of instilling interdependent safety culture at its plants around the world.
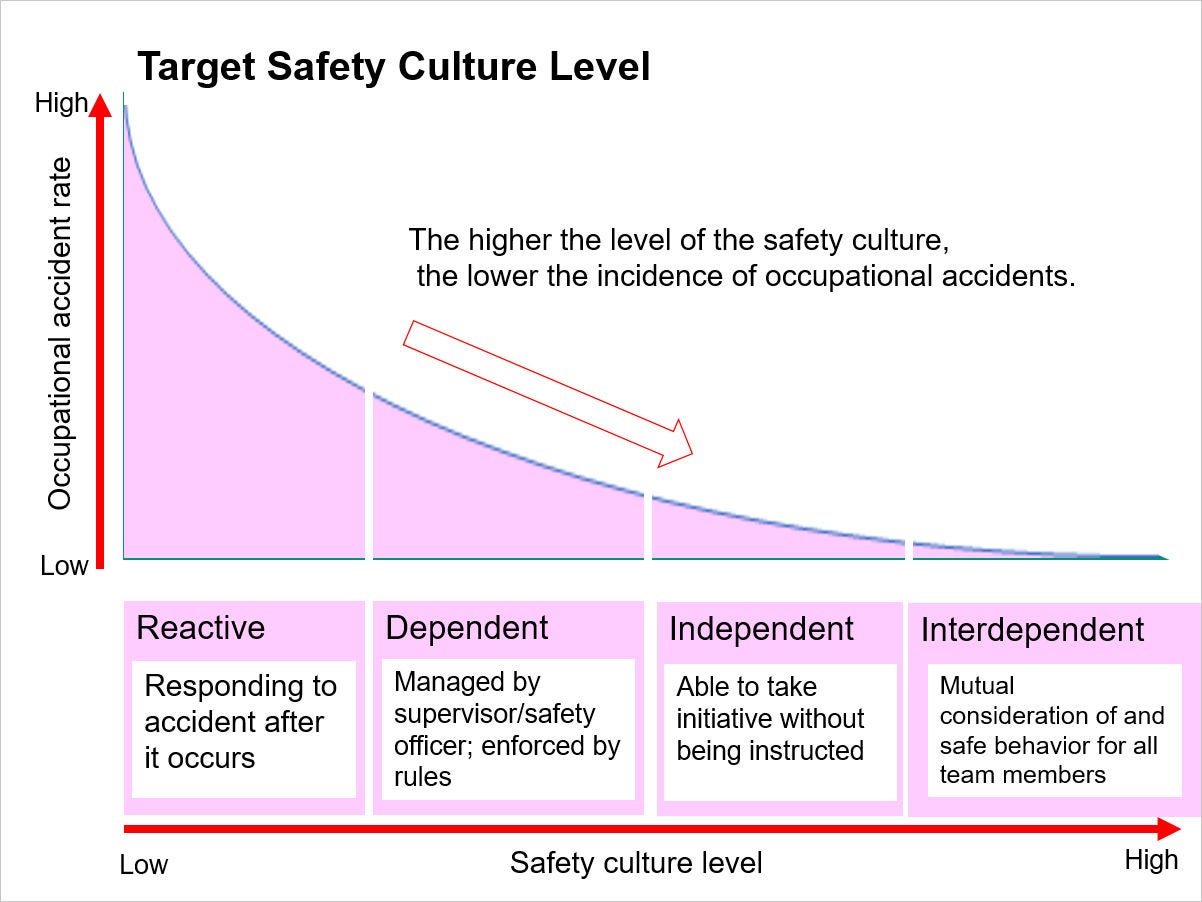
Practicing “Core Value Contact” in Each Department
The NSK Group practiced “Safety Contact” at the beginning of meetings, morning briefings, and other occasions from FY2019 to FY2021. In this activity, employees shared their thoughts and ideas about safety. It gave employees more time to think about safety, with the expectation that this would enhance sensitivity to safety issues. The program received positive feedback such as: “It’s easy to relate to stories I hear from people close to me,” and “It allows me to see different ways of thinking about safety in a new light.” “Safety Contact” served as a valuable safety enhancement tool.
Starting in FY2022, the NSK Group expanded the “Safety Contact” program and renamed it “Core Value Contact,” to give employees not only more time to think about safety, but also about the Group’s Four Core Values (Safety, Quality, Environment, and Compliance) and their contribution to the Core Values.
Safety Dojo
The NSK Group has established facilities called “Safety Dojo” at all production sites, where employees receive training using simulators to experience potential workplace hazards. In these dojos, employees learn the importance of prioritizing safety by recognizing the risks of hazardous tasks by learning from actual workplace incidents that have occurred within the NSK Group, while being trained to follow correct operating procedures. All plant employees receive regular, annual training at the Safety Dojo. We have compiled manuals of operational procedures, which have been distributed to plants in each country to help foster a culture of safety. Virtual reality (VR) content has also been incorporated into the curriculum recently, allowing participants to simulate experiences such as working at heights and dealing with fire hazards.
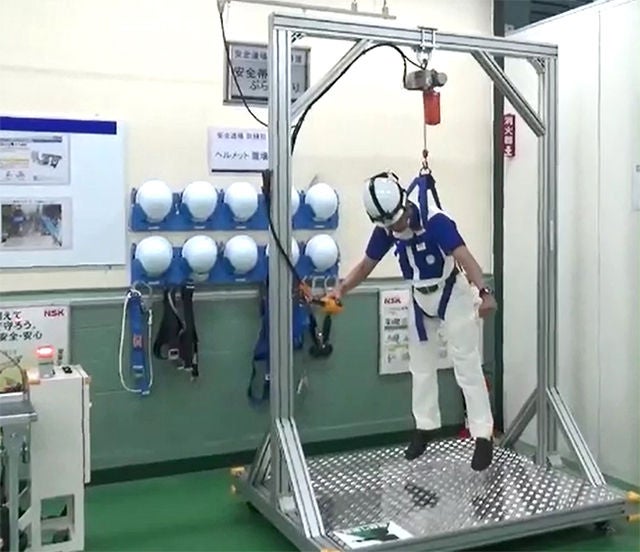
Experiencing a safety harness
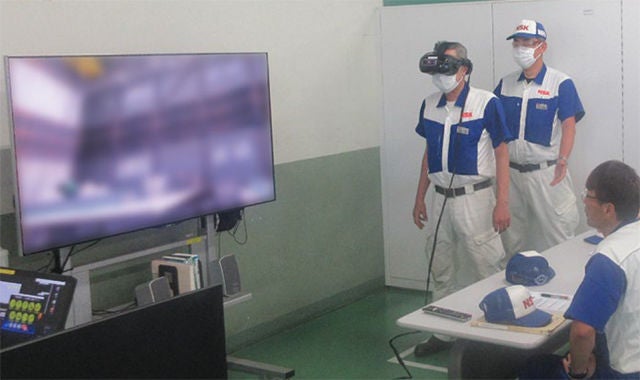
VR safety training at the safety dojo
STOP6 + 2 Activities
The NSK Group conducts “STOP6 + 2” activities as a means of preventing fatal and serious accidents. STOP6 is an initiative for occupational safety designed to prevent fatal and serious accidents. STOP6 classifies accidents in the manufacturing industry into six major types and defines key prevention activities. In addition to the accident types identified by STOP6, the NSK Group addresses “oxygen deficiency and poisoning” and “accidents caused due to an employee working alone” as two additional accident types in its “STOP6 + 2” activities.
Major Accident Types in STOP6 + 2 Activities
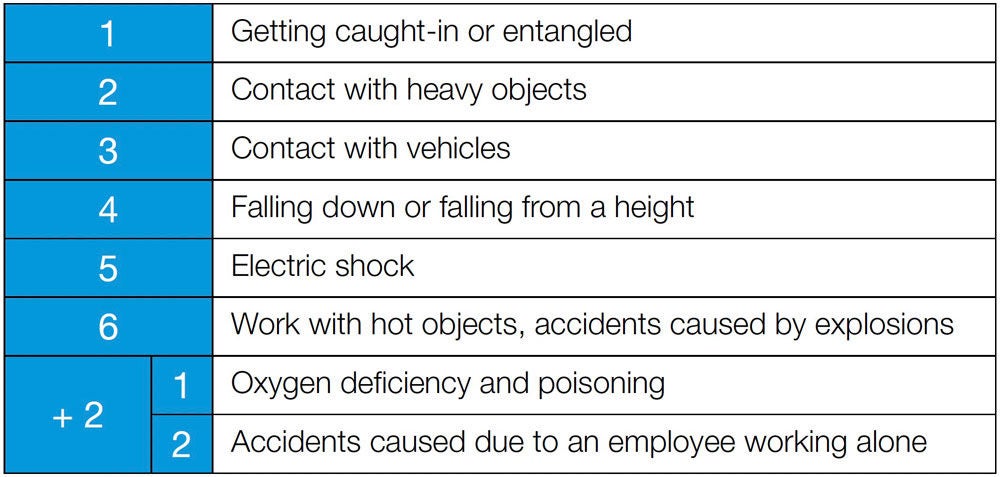
◆Hardware Countermeasures
Risk Assessment
At NSK’s production sites, we conduct risk assessments of equipment and machinery, continuously implementing measures to reduce workplace hazards, particularly those deemed high-risk. To enhance safety, risk assessments are also conducted from the development stage for new equipment and processes. Currently, we are training safety assessors who have obtained qualification certifications from external institutions, ensuring that personnel with the proper knowledge and skills are taking action to mitigate risks. NSK currently has approximately 1,000 safety assessors, and we are working to continuously increase this number.
These initiatives are also being expanded to China, with in-house instructors from the Manufacturing Strategy Division HQ visiting the region to conduct risk assessments at production sites to establish this practice and boost the level of risk assessment.
As a result of these initiatives, the total number of workplace incidents across the entire NSK Group has decreased each year, and the number of incidents has been halved compared to when these initiatives first began.
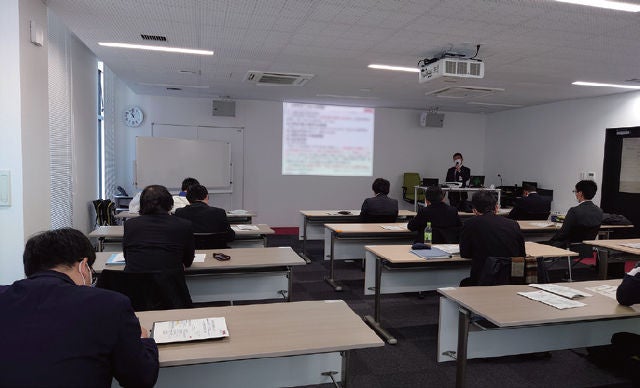
In-house training to improve the risk assessment skills of certified personnel
◆Compliance
Sharing Examples of Workplace Incidents
In the event that a workplace incident occurs at an NSK Group site, the information is shared on the Company’s intranet for all business sites worldwide to view. Reenactment videos are created to provide detailed insights into the incident. This encourages employees to carry out activities to look across* at other workplaces where incidents occur and reflect on whether similar operations or situations exist in their own workplace.
By sharing past workplace incidents across the organization, NSK is working to prevent the recurrence of incidents, heighten safety awareness, and further promote the creation of a safe, secure, and comfortable working environment.
* NSK conducts “Look Across Activities” where employees take ownership of their surroundings and work proactively on issues, as well as taking an interest in and being involved in these efforts at other workplaces. Carrying out “Look Across Activities,” either on a workplace or an individual level, makes it possible to identify new risks and make the working environment safer. These activities also increase communication about safety in the workplace and help to foster an interdependent safety culture.
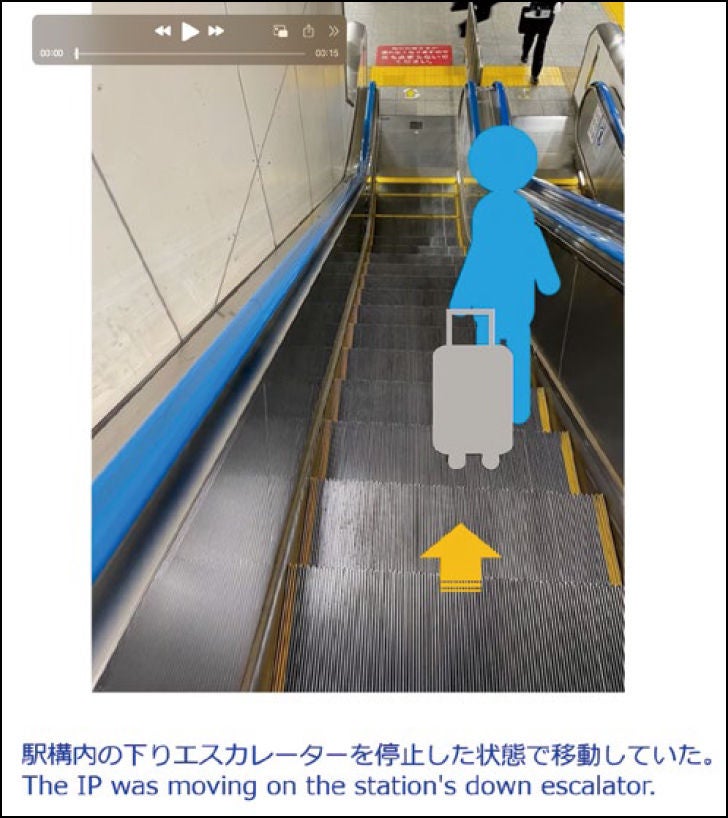
Frame captured from a workplace incident reenactment video
Contributing to Safety Awareness (National Industrial Safety and Health Convention)
The NSK Group trains risk assessment promotion leaders by providing classroom lectures and risk assessment practices at production sites for personnel who have a machine safety specialist certification. In addition, we are rolling out a project led by risk assessment promotion leaders to re-inspect all production facilities in Japan in order to reveal unidentified risks. These efforts have improved risk communication (sharing information on hazards within the Group). Employees working at plants are now able to identify and discuss problem areas at an advanced level.
There are currently over 1,000 qualified safety assessors at the NSK Group. Occupational accidents at sites in and outside of Japan have fallen by 60% since 2016, when these risk assessment activities were begun. In addition, the NSK lost time injury frequency rate in Japan, at 0.11, is significantly lower than the manufacturing industry average. These results demonstrate that our rational risk assessment and risk reduction activities are effective. We shared examples of our safety-related personnel development and reductions in occupational accidents at the 83rd National Industrial Safety and Health Convention.
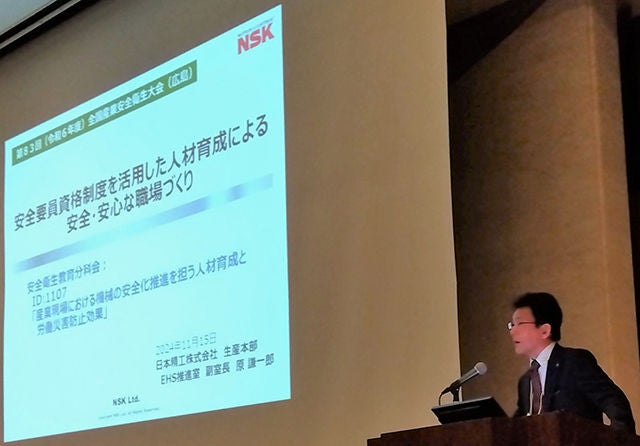
NSK presentation at the 83rd National Industrial Safety and Health Convention
Reviewing Guidebook for External Construction Crews and Reinforcing Construction Rules
To ensure the safety of external construction crews who carry out such high-risk work as work at height or working with fire, the NSK Group has put together a guidebook for external construction crews, which covers 18 specific points. We also regularly review regulations and standards to maintain our record of zero occupational accidents in construction. More specifically, these efforts include strengthening the presence of attending personnel during hazardous work, upgrading preliminary training for construction directors and work managers, and conducting interdependent safety checks using task point checklists before work begins.
The entire process for construction request applications, from initial request to completion of construction, is centrally managed via the external construction management web system developed by NSK. At the same time, employees are able to check daily construction schedules and locations, and this has also helped to improve efficiency.
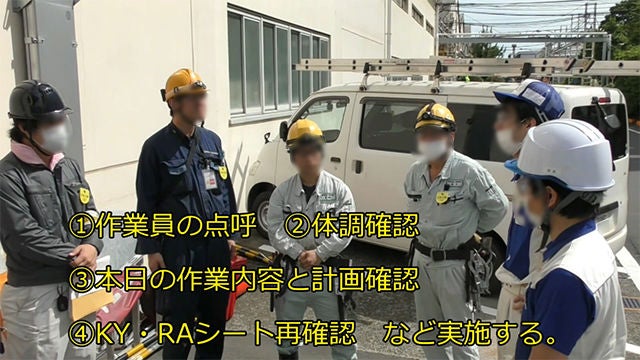
Frame capture from an educational video on guidelines for managing external construction