Quality Management
NSK’s Approach
With quality as one of its core values, the NSK Group aims to become “No. 1 in Total Quality.” In other words, we are working to achieve the industry’s best quality in everything we deliver—not only products and services but also information. We believe that this commitment to quality ensures that our products will satisfy customers all over the world.
To achieve our Quality Assurance Vision 2026 (100% good products and services that put the customer first), we engage in activities based on the Three Pillars of NSK Quality Assurance.
Three Pillars of NSK Quality Assurance
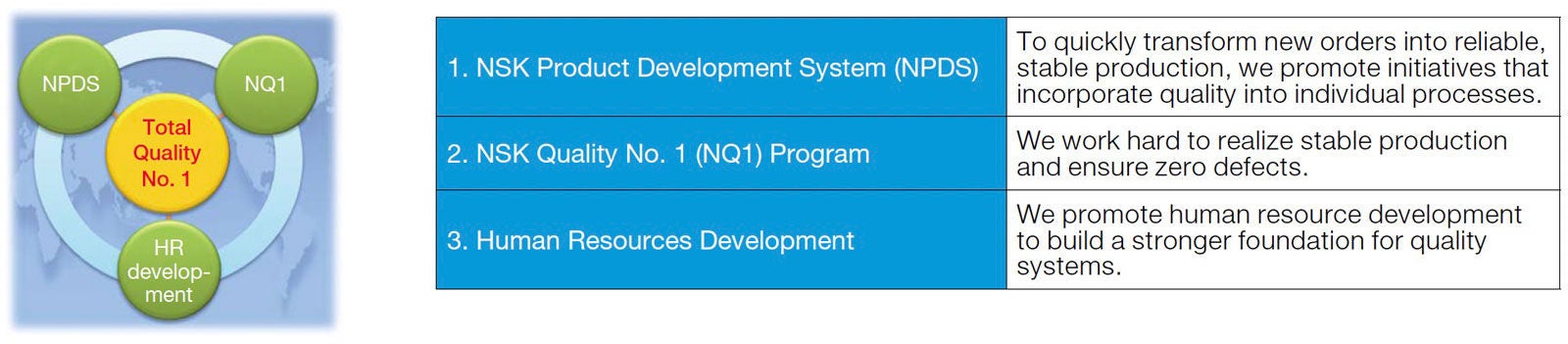
◆Quality Assurance Vision 2026
Our Quality Assurance Vision 2026 sets clear goals and expectations to achieve by 2026. It has Three Pillars, as mentioned above. Across the NSK Group, we are working to build a seamless, consistent system for quality improvement, leveraging inter-departmental collaboration to achieve our goal of being No. 1 in Total Quality. This includes quality at every operational stage, from design and manufacturing, to supplier management and field responsiveness. Our goal is 100% good products and services that put the customer first, by 2026.
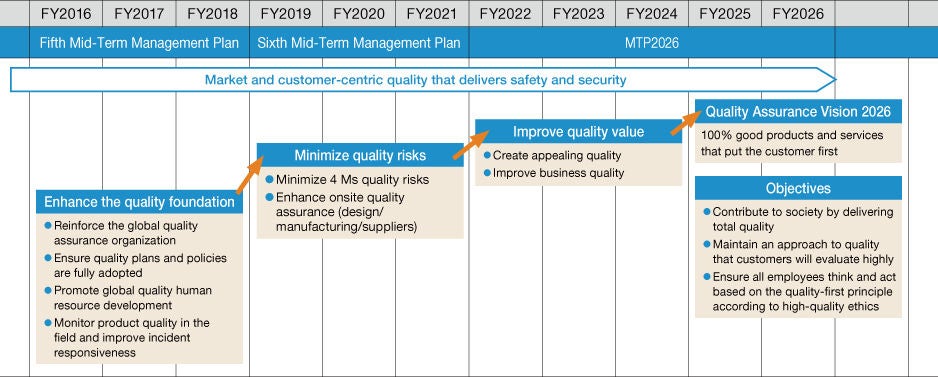
System
◆Quality Assurance Organizations
The NSK Group has established the Core Values Committee to promote and strengthen corporate activities based on NSK’s core values (safety, quality, environment, and compliance). To that end, it identifies issues for the entire Group to address by discussing policies and sharing information on related risks. The Committee also provides suggestions for and monitors progress on solutions to these issues.
The Quality Assurance Division Headquarters is positioned as the global headquarters for quality management, and quality councils have been established within each business unit as subordinate organizations of the Core Values Committee. Together, they work to strengthen quality improvement efforts by promoting cooperation among the manufacturing, sales, and technical departments. The headquarters also reports the Group-wide status of quality management to senior management at monthly Executive Officers’ Meeting.
We have established regional quality assurance departments in South Korea, the Americas, Europe, China, ASEAN/Oceania, and India. This global quality assurance system has been built to meet customer needs in each country and region, as the highest priority. Annual global meetings and biannual regional meetings on quality are held to share and discuss quality-related information and to strengthen monitoring, oversight, and the support structure in each region.
NSK Quality Council
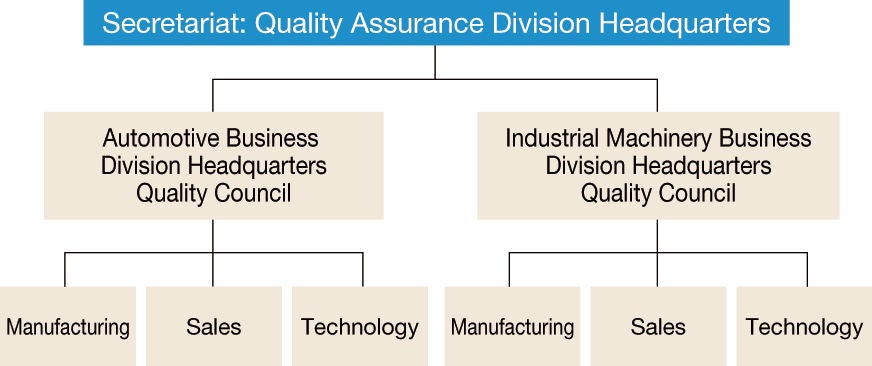
Global Quality Assurance Organization
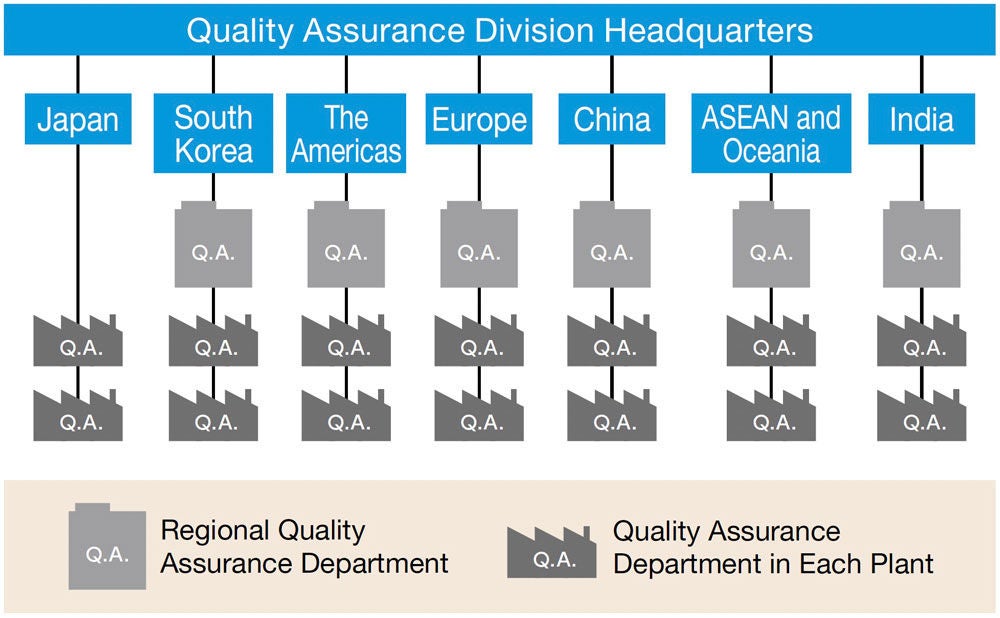
Targets and Performance
◆Mid-Term Management Plan 2026 (MTP2026) Targets, with Targets and Performance for Each Fiscal Year
Policy | NSK Product Development System (NPDS): NSK’s proprietary quality management system that quickly translates new orders into reliable, stable production | NSK Quality No. 1 (NQ1) Program: Initiatives to realize stable production and ensure zero defects | Human resource development: NSK is promoting the human resource development to build a stronger foundation for quality creation. | |
---|---|---|---|---|
MTP2026 | Targets |
|
|
|
FY2023 | Targets |
|
|
|
Performance |
|
|
| |
FY2024 | Targets |
|
|
|
* FMEA: Failure Mode and Effects Analysis, a method for identifying potential failure modes in design and manufacturing, evaluating their impact, and taking steps to address those
Quality Improvement Initiatives
To ensure quality that puts customers first, and enduring quality in the field, the NSK Group strives to secure and improve quality throughout the product process, from design, to procurement from suppliers, to manufacturing. We are promoting total quality through the four initiatives shown below.
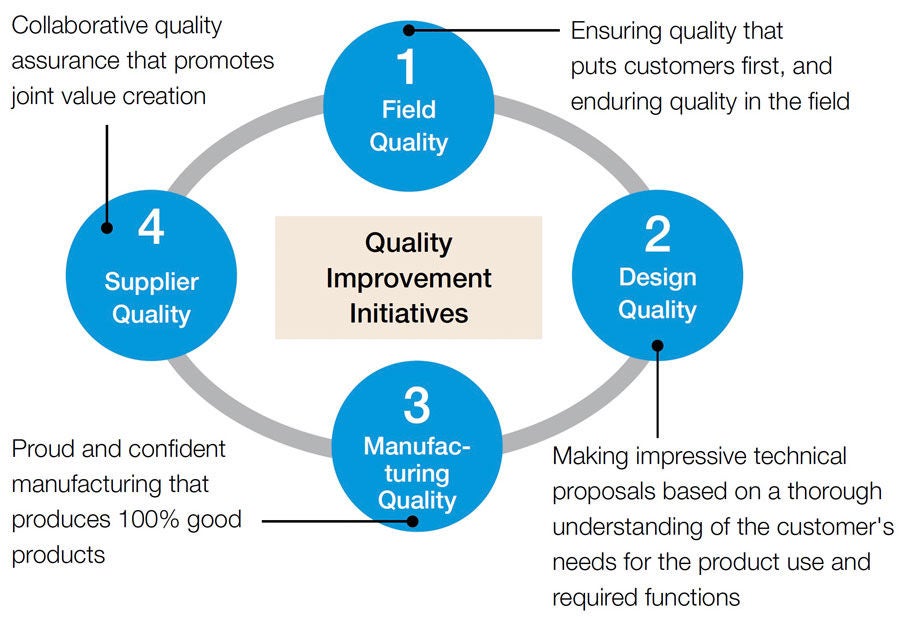
◆Initiatives to Enhance Field Quality
As a firm that services the manufacturing sector, the NSK Group aims to achieve a level of quality that meets the expectations of society at large. This is why we not only strive to satisfy our direct customers, but also look beyond to assess the needs of the end users who use products with NSK components. Our system enables us to both propose and deliver quality products and services that thoroughly fulfill both customer and social needs.
Customer Management Database
In order to accurately meet customer requests, the NSK Group provides technical support related to design and expert knowledge on product usage. We have also established a database of information such as response history for customer inquiries. The information gathered from various countries and regions is used to improve our products and services.
◆Initiatives to Enhance Design Quality
The NSK Group incorporates feedback from customers into its designs to enhance quality in the design stage. We make every effort to design products with a superior level of quality by drawing on our expertise and experience in the market, cultivated over many years. We always strive to meet our own unique quality targets, going above and beyond the core quality that our customers have come to expect.
Building Quality into Each Process: NSK Product Development System (NPDS)
The NSK Group has globally deployed an innovative quality management system, the NPDS, to respond promptly and reliably to new projects and to mass produce products that satisfy customers. At each stage of the process, from product planning to development/design, prototype manufacturing and mass production, we ensure that any concerns are resolved and strive to improve quality. Even after mass production begins, we conduct thorough management to maintain high quality.
Outline of NPDS
Education to Improve the Quality of Design Reviews in Developed Products
To improve product design quality in new projects, the NSK Group has its own internal system of experts that perform design reviews (DR) and has implemented worldwide measures to improve DR quality. These DR experts identify issues related to product quality from the design phase and into the mass production phase to prevent problems down the road. Along with the enhancement of DR content for NSK-developed products, we ask these experts to make the most of their knowledge and experience: (1) to promote robust design* proposals that fully meet customer requirements; (2) to build manufacturing processes that emphasize the 4Ms and maintain stable production; and (3) to hand down technology skills while creating learning opportunities for young NSK engineers.
To raise the DR level, the necessary materials and data need to be prepared in advance. When all the participants understand the design details before the DR meeting, the review discussions are more efficient and meaningful. NSK is increasing the number of opportunities for discussions between DR experts and our designers and developers, while working to raise their technical skills and improve the technical data that is needed for each step of the DR process. Moreover, by conducting optimal evaluation and feedback in each step of the DR process, we are working to improve the quality of product development projects as part of our DR quality enhancement efforts.
* Robust design: Design that ensures the required characteristics for various product usage conditions.
◆Initiatives to Enhance Manufacturing Quality
The NSK Group works diligently to deliver a consistently high level of product quality that meets customer needs.
We also develop manufacturing processes that focus on the 4Ms (man, machine, materials and methods) to further improve product quality.
4M Priority Issues
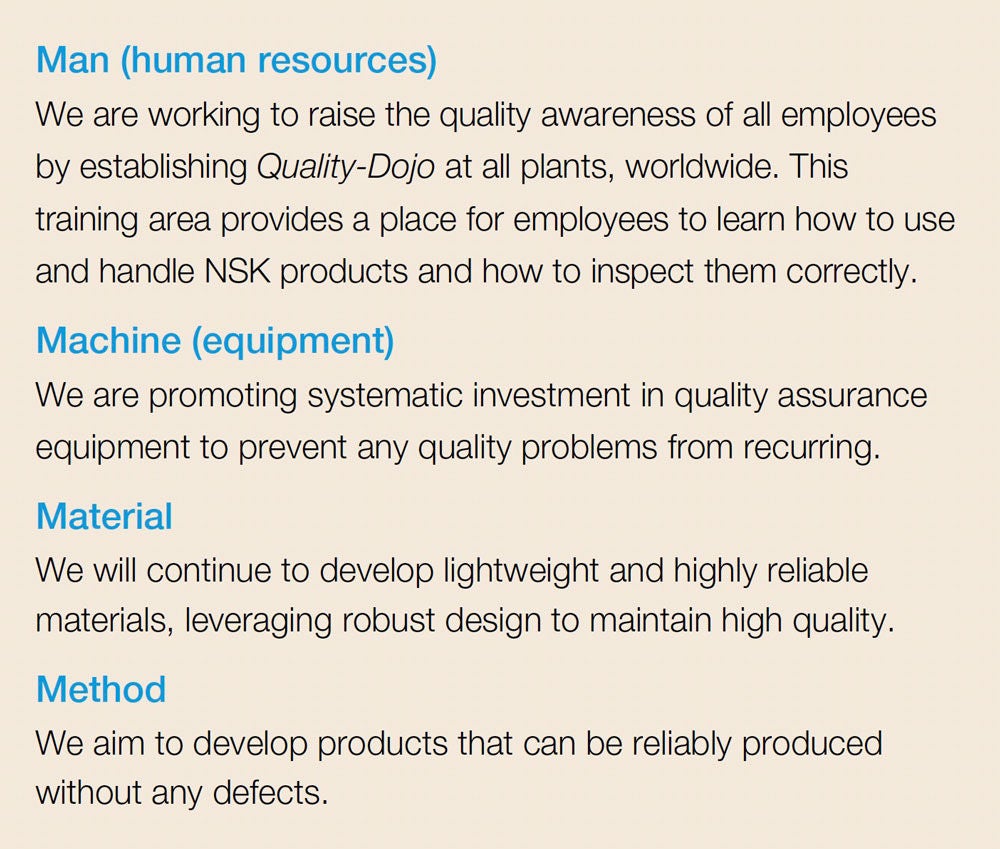
Product Assurance Through Quality Inspection
To provide customers with assurance that they can use our products with confidence, the NSK Group conducts thorough inspections to ensure product quality. These inspections consist of both visual and functional tests and are conducted at various points of the manufacturing process, from acceptance to shipping, to prevent any defective products from leaving the plant.
Going forward, we aim to improve process assurance and increase efficiency by automating more inspections.
Preventing Quality Defects Through Effective Data Utilization
NSK is working to implement heat treatment cockpit systems across all its plants worldwide. This system enables continual operational status monitoring for heat treatment furnaces. By managing the big data obtained from this monitoring, we aim to prevent heat treatment defects before they occur.
Some customers, such as operators of railway vehicles and large-scale plants, use NSK products in environments where maintenance and inspections are challenging, and where equipment failure poses significant risks. To better support these customers, we have introduced the Condition Monitoring System (CMS) for quality assurance and defect prevention. This system detects vibrations during bearing operation and conducts vibration diagnostics, enabling the early detection of abnormal conditions. Through initiatives like these, we strive to ensure that customers can use our products with confidence.
Global Quality Improvement Activities and Their Deployment
Every month, the NSK Group monitors the status of quality management at all production sites worldwide. The NSK Group is engaged in efforts such as zero-defect activities, recurrence prevention activities, and Quality-Dojo activities across all production sites as part of its quality improvement activities. The Quality Assurance Division Headquarters has introduced an award system for each activity, aiming to incentivize active participation. In addition, production sites that have achieved particularly excellent results in terms of quality are designated as outstanding plants, and their characteristics and operational initiatives are analyzed and horizontally deployed to other production sites.
《Objectives of Quality Information Exchange Meetings for Plants》
- Learn from the successful activities of other plants
- Share solutions for particular problems
- Adopt the "Look Across Activities" approach to problems (to prevent problems from recurring at other plants)
Quality Training
To promote continuous awareness and knowledge improvement on quality, one of the NSK Group’s core values, the Group provides annual quality training for all employees.
NSK’s quality education program is designed by the Quality Assurance Division Headquarters. Appropriate quality training is conducted as part of group training sessions organized by the Headquarters’ Human Resources Department, NIT,* and other relevant departments, depending on employees' divisions and organizational levels. Moreover, since fiscal 2019, we have been establishing Quality-Dojos at our plants and technical departments, where regular quality training is conducted annually.
《Training includes》
- Rank-based quality training for new employees and managers, tailored for their respective roles and responsibilities
- Quality-Dojo training that allows employees to learn through actual examples and products
- Digital quality training for all employees delivered via e-learning
Sixth Mid-Term Management Plan: Function-Based and Rank-Based Quality Education System
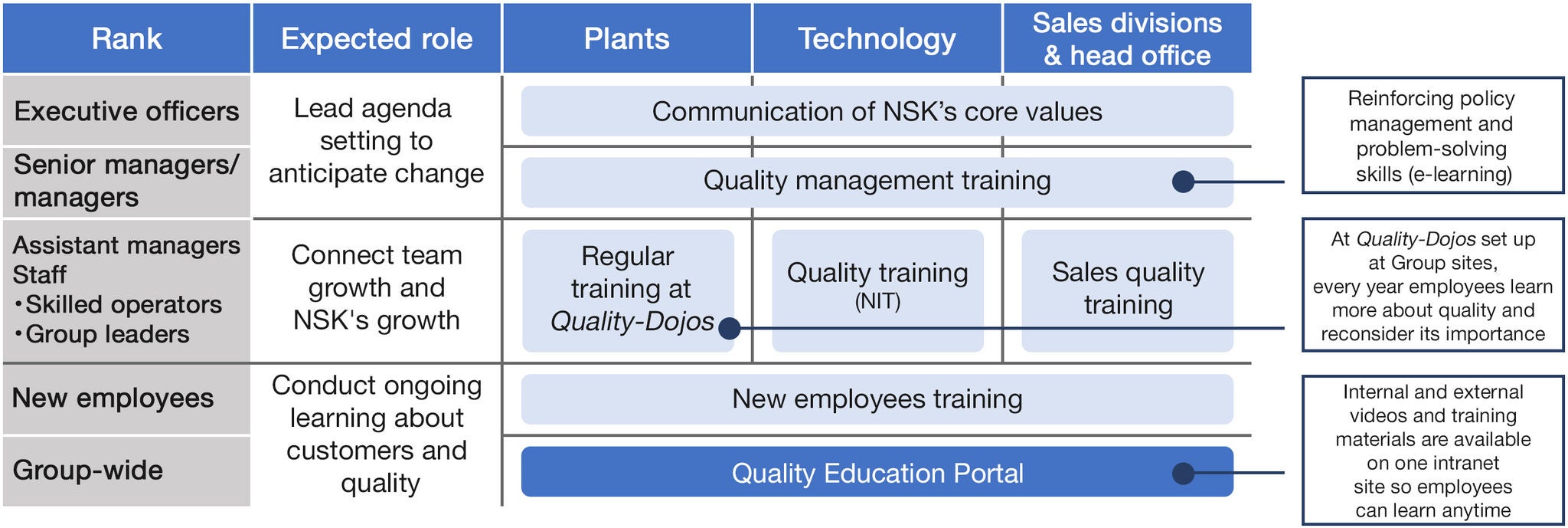
* NIT (NSK Institute of Technology): A faculty-based educational institution with credit-based courses that provides comprehensive technical education on product applications/handling, quality control, manufacturing methods, and cost efficiency. Established in 2007 as an educational center for members of NSK and NSK Group technical departments, NIT aims to develop highly skilled personnel who can support NSK's technological competitiveness.
Quality-Dojo* Training
We believe that quality education should be learned in the order of awareness →knowledge → technique/skill.
To eliminate defects caused by human error, we have established Quality-Dojos at 52 production sites worldwide. In these dojos, we foster awareness by explaining the importance of quality, while hands-on experience with actual products and defective items helps employees gain knowledge about products and quality. At NSK, it is our goal for employees working in production and technical departments to participate in Quality-Dojo training at least twice a year. By connecting what they learn to their daily work, these employees become valuable contributors to high-quality manufacturing, helping NSK achieve No. 1 in Total Quality.
* Teachers and assistant instructors will be appointed to all Quality-Dojos to manage them comprehensively, ensuring the enhancement and renewal of educational content to the training of instructors and the formulation of educational curricula.
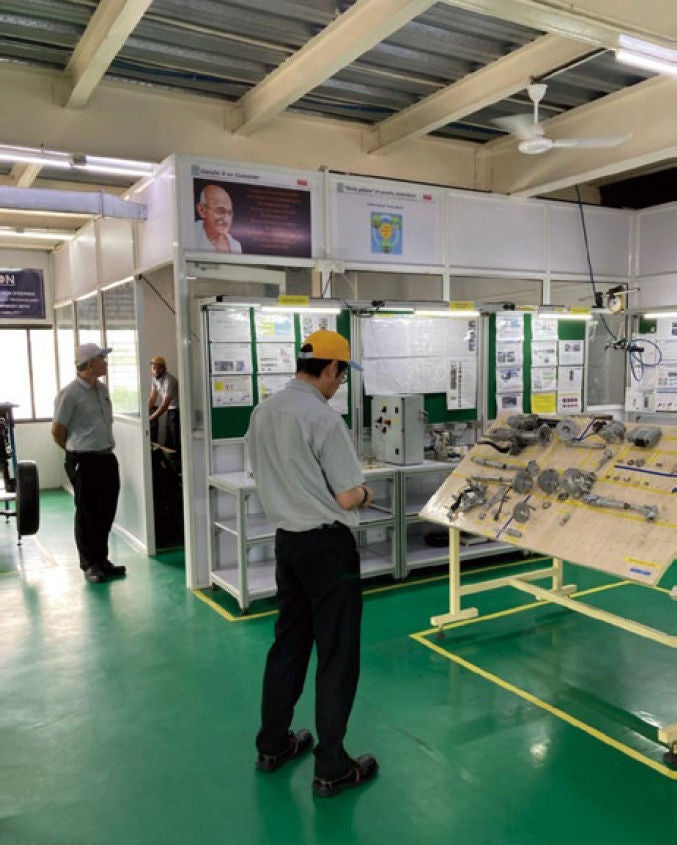
Quality-Dojo Training: On-Site
◆Initiatives to Enhance Supplier Quality
High-quality lubricants, materials, and parts are required to manufacture high-quality products. At the NSK Group, we engage in a wide range of initiatives to enhance quality, based on our strong ties with suppliers. Our Quality Assurance Division Headquarters works to promote quality data visualization at suppliers, implement improvement plans, and carry out quality improvement efforts, collaborating closely with the NSK plants that receive products from suppliers.
Main Initiatives
Policy | Details |
---|---|
Supplier briefings on quality activity policy | By providing annual procurement policy briefings for key suppliers, NSK shares its quality activity policies and provides guidance and explanations on quality compliance and quality improvement initiatives In May 2024, 87 companies participated in procurement policy briefings. |
Ascertaining and visualizing the current quality situations at suppliers | Using trend graphs and radar charts to clarify the situation for quality problems originating at suppliers that are detected during receiving inspections and on production lines |
Development of a management system for supplier quality problems |
|
Monthly report on supplier quality issues |
|
Activities to Enhance Supplier Quality Awareness
NSK has been introducing its suppliers to Quality-Dojo training, which is highly effective in fostering quality awareness. Some suppliers have established their own Quality-Dojos and are promoting quality training. NSK provides guidance on activity content, instructional panels, and training methods to support the improvement of supplier quality education. With the aim of further enhancing quality awareness, during Quality Month we also provide interested suppliers with cards listing the 10 Quality Principles that NSK workers follow.
◆Other Initiatives
Strengthening Audit Functions
The role of the Global Quality Audit Office at the Quality Assurance Division Headquarters is to monitor compliance situations and potential risks relating to quality control, and to implement preventive measures for potential problems. To fulfill this role, the office conducts audits from a third-party perspective.
The audit office also constantly gathers product recall and defect information on other companies. It examines this information and promotes necessary information development and preventive activities.
Quality Management System
The NSK Group has obtained ISO 9001 and IATF 16949 certifications, the international standards for quality management systems, at its development, design, and manufacturing facilities. In addition, the effectiveness of our quality management system is verified through periodic third-party and internal audits, and when problems are found, appropriate corrective measures are taken to continually improve the level of our efforts.
Response to Product Defects
NSK provides customers with technical information and handling instructions to ensure the safe use of its products. We do our best to ensure quality, but in the unlikely event of a product or service defect, we will promptly inform the customer of the information, and all relevant departments will work together to take prompt and appropriate action to prevent the problem from spreading. We will also investigate the cause of the problem and prevent its recurrence.