Vol. 2
Building the future of manufacturing with cutting-edge technology
Mobile Collaborative Robot Development Team, Intelligent Technology Development
Department
Vol. 2
Building the future of manufacturing with cutting-edge technology
Mobile Collaborative Robot Development Team, Intelligent Technology Development
Department
Team Members
-
Senior ManagerTakahiroNew graduate hireTakahiro worked in the Heat Treatment Section of NSK's former Maebashi Plant for around a year, before pursuing further study in Japan for four years. After returning to work, he worked in visual inspection at the precursor to the current Manufacturing Engineering Center. In this role, he developed a system to monitor the operational status of machinery in real time. After stints working as a group manager in the company's IT and robotics divisions, he was appointed as a group manager in the Intelligent Technology Development Department when it was established.
-
Image ProcessingXiaoyingMid-career hireXiaoying joined NSK in 2019 as a mid-career hire, after previously working in production line automation at a robotic systems integration company. After joining NSK, she has worked in the Automation Group of the Intelligent Technology Development Department, developing mobile collaborative robots to automate alignment and removal of components on the production floor. She is also currently interested in 3D simulators and has been tasked with utilizing 3D virtual systems to shorten development time when developing new equipment.Comments from team managerCommentXiaoying has prior experience meeting the high demands of customers as a systems integrator. She is also a foreign national, so she brings a fresh perspective to the team. I hope that the unique qualities and skills she brings to the table will inspire our manufacturing and development team. She is very dedicated and driven, and is always focused on the end goal! I find her willingness to learn new technologies such as real digital twin1 and her positive attitude wonderful.NSK’s unique development technology that generates an accurate virtual copy of the device or product being developed. This allows engineers to arrive at solutions that break through preconceived ideas by observing the device or product from the inside in detail and understanding its true nature through deduction and modeling.
-
Robot ProgrammingHirokiNew graduate hireHiroki joined NSK as he was interested in working for a business-to-business (B-to-B) manufacturer that supports the foundations of society. For around three years after joining NSK, he worked in mechanical design and equipment start-up for bearing assembly and inspection equipment in the Manufacturing Engineering Center's Manufacturing Equipment Development Department. He then transferred to the Intelligent Technology Development Department's Automation Group, where he is working to develop mobile collaborative robots.Comments from team managerCommentOur work in the Automation Group requires all-round knowledge and experience in machinery, electronics, and systems, and it is not a job that can be done by a specialist in any one technology. Hiroki moved to the group after 3 years of working in mechanical design with a desire to take up a new challenge, and he has worked diligently and enthusiastically even when tackling a task for the first time. His willingness to learn new technologies is very admirable. Plus, he is a great moodmaker and team player!
Leveraging robotics and image processing
to achieve plant automation and
increased efficiency
At the center, a relatively new organization called the Intelligent Technology
Development Department was launched only five short years ago. At NSK's
Manufacturing Engineering Center, our engineers develop and implement production
equipment with the aim of improving product inspections and enhancing
productivity through automation and increased efficiency.
In this interview we sat down for a chat with the members of the Automation Group, which is on a mission to develop innovative automated equipment using the latest in robotics and image processing technology. Together with their team leader, Takahiro, Hiroki, and Xiaoying work together as a four-person unit to develop automated production equipment through autonomous robotic technology.
In this interview we sat down for a chat with the members of the Automation Group, which is on a mission to develop innovative automated equipment using the latest in robotics and image processing technology. Together with their team leader, Takahiro, Hiroki, and Xiaoying work together as a four-person unit to develop automated production equipment through autonomous robotic technology.
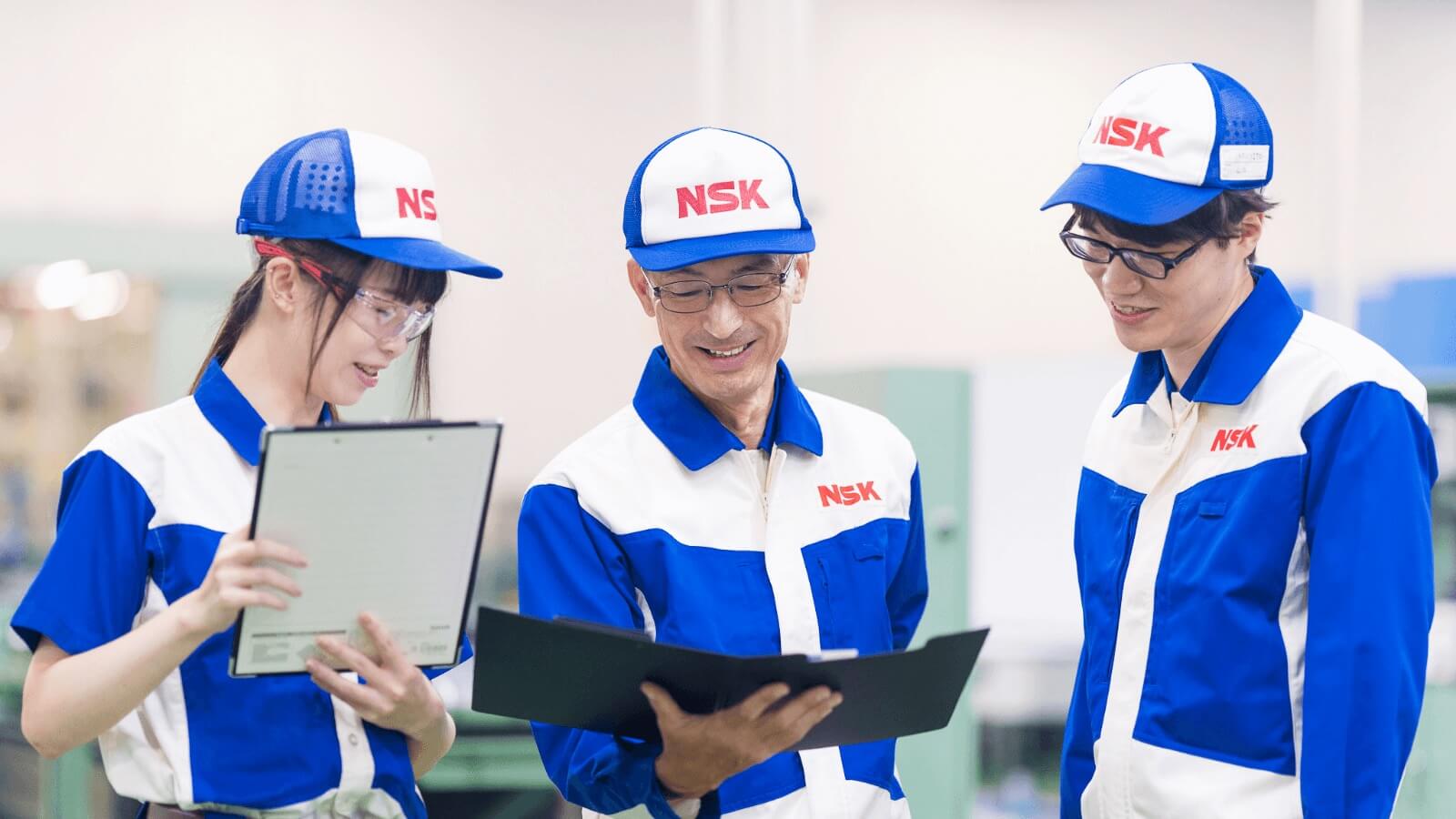
The team pooled their respective strengths to develop a robot that could align, load, and unload components
On the production floor, loading, unloading, and transporting components is a
complex task, making it difficult to automate. As a solution to this problem, this
team developed a mobile collaborative robot that works like a human arm and can be
adapted to a variety of different production machines. By mounting a collaborative
robot on top of a commercially available autonomous mobile robot (AMR) and adding a
robotic hand for loading and unloading the components as well as image processing
functionality, the team succeeded in creating the perfect device for automating this
complex task.
Putting our heads together to find new solutions with new technology
Tell us about how you approach your work.
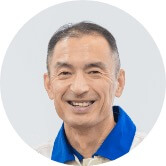
Typical manufacturing engineering work consists of maintaining the plant and
building new production lines by reinstalling machines for repeat products.
However, we do not simply wait for requests. Instead, I visit the plants and
work with managers to figure out what their needs are and determine what
kind of equipment would make operations more efficient. Then I share the
image and specifications of the equipment we discussed with the younger
members of our team like Hiroki and Xiaoying. Once I have them on board with
the concept, we split up the tasks that need to get done and dive into the
development process.
What roles did you each play in this project?
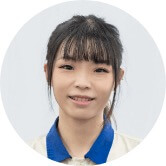
I was in charge of making the robot adjust its position and identify the
components it needed to pick up and transport through image processing. To
use the human body as an analogy, I essentially helped create the eyes.
Since this was a mobile robot, I developed an imaging function to check the
position of the robot and confirm that the required number of components
were loaded onto it.
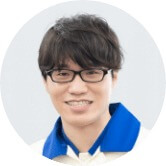
I was primarily in charge of creating the programming for the robot’s
movements and how it handled the components as well as the motion of the
unit overall. Essentially, I developed and designed the brain of the robot
that tells it when, how, and how far to move.
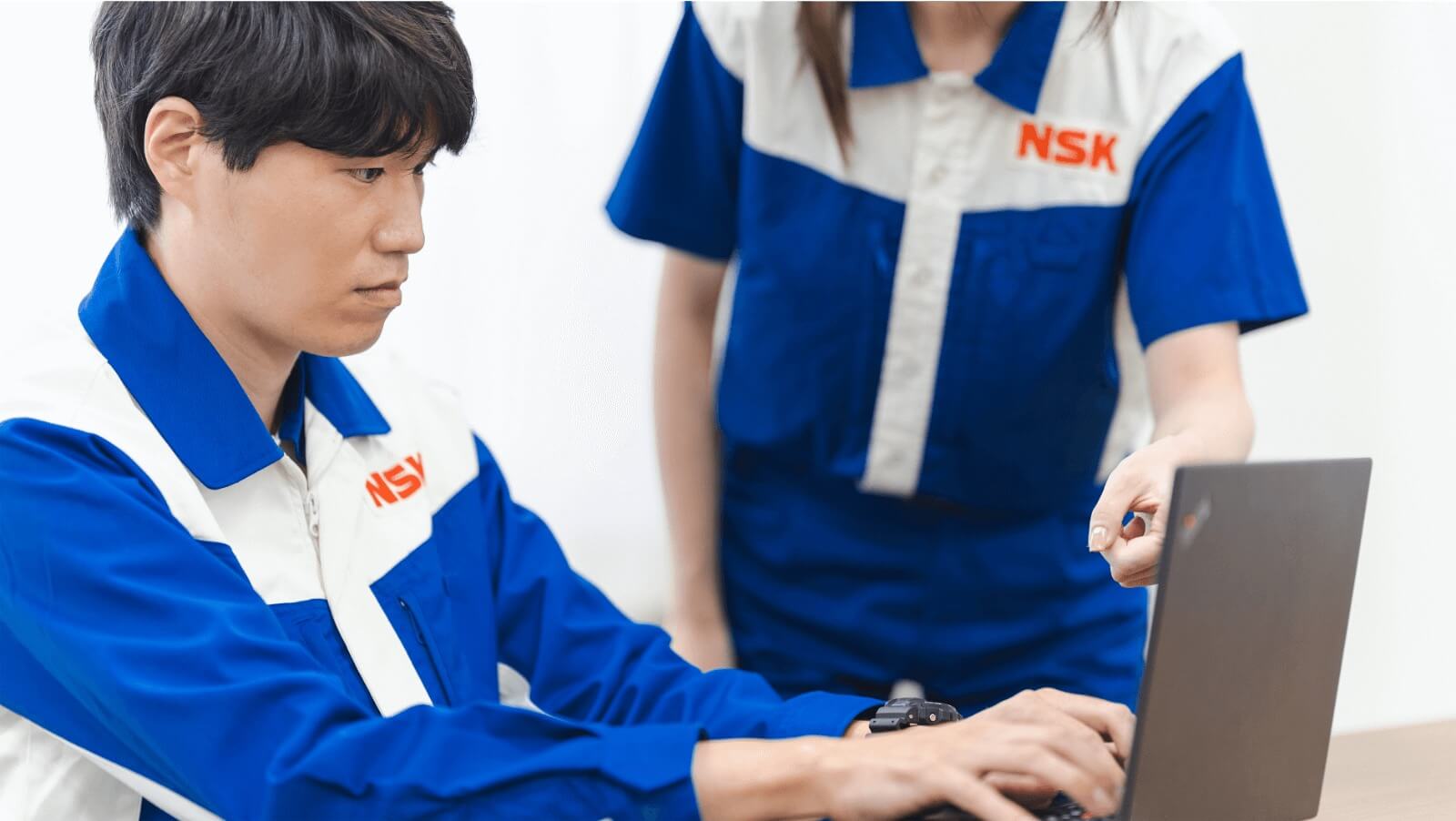
When you hit a wall while working on this project, how did you overcome it?
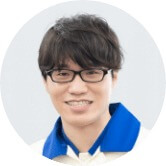
Well, we ran into a lot of walls (laughs). We would share the problems and
challenges we were facing with the team, and put our heads together to come
up with a solution. If we don’t maintain a regular understanding of each
others’ work, we would each be left to face those challenges and problems on
our own. When all of our team members understand what the others are working
on, it's a lot easier to give each other advice. If you’re struggling with
something, the person next to you will always have a helpful idea.
I think we can provide that support for each other because we all have a common understanding of a single goal. Each of us is constantly thinking of how we can develop even better technology. That's why we have an environment in which people are quick to put their ideas out on the table, and everyone is ready to listen.
I think we can provide that support for each other because we all have a common understanding of a single goal. Each of us is constantly thinking of how we can develop even better technology. That's why we have an environment in which people are quick to put their ideas out on the table, and everyone is ready to listen.
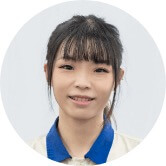
There are a lot of people you can ask for advice if you don’t understand
something because the people in our group have a diverse array of technical
backgrounds. I’m thankful to be on a team where everyone comes together to
find a solution whenever anyone has a problem.
When developing this robot, I ran into a lot of problems that I wasn’t expecting. Whenever an issue came up, I would consult with Hiroki and we’d tackle the problem together to come up with a solution. When the two of us couldn’t solve the problem alone, we would consult with our team leader or Takahiro, and through collaboration we would arrive at a solution.
When developing this robot, I ran into a lot of problems that I wasn’t expecting. Whenever an issue came up, I would consult with Hiroki and we’d tackle the problem together to come up with a solution. When the two of us couldn’t solve the problem alone, we would consult with our team leader or Takahiro, and through collaboration we would arrive at a solution.
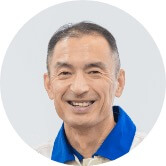
Since our team leader was also there, I generally held my tongue and let
them work out the problem based on their own ideas (laughs).
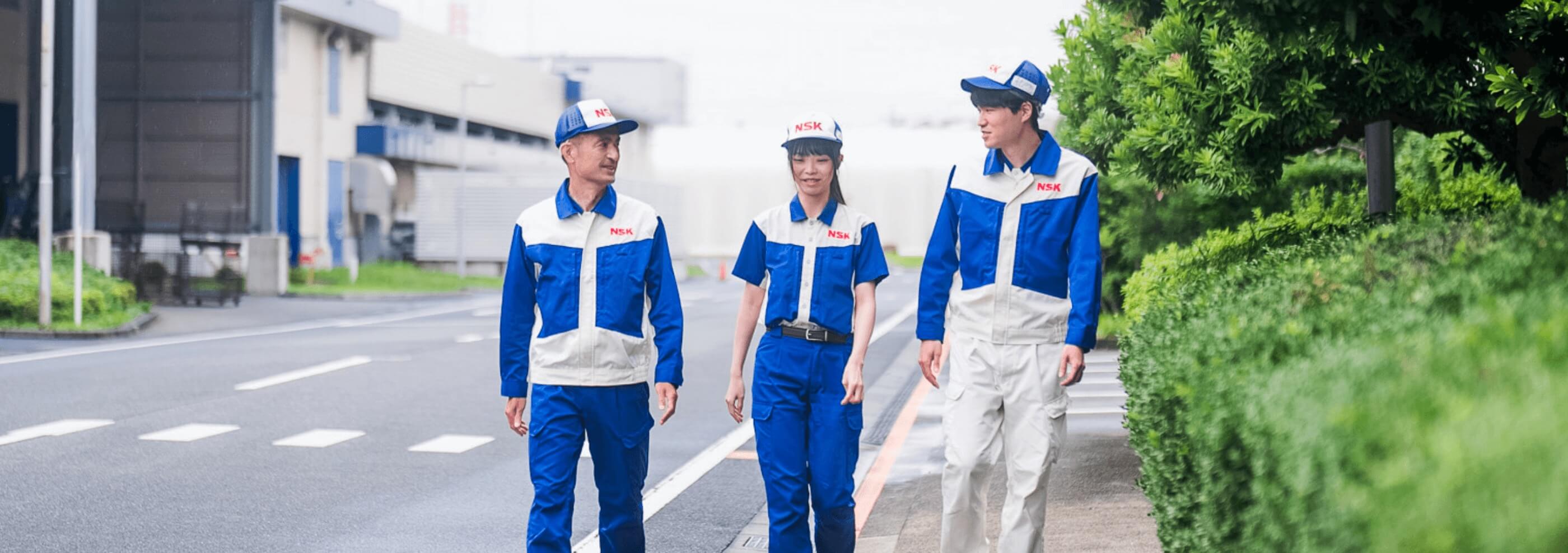
In what ways do your team members help you out?
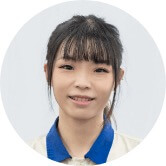
Hiroki sits next to me, so he is the first person I go to. Neither Hiroki
nor I have a lot of experience with IT system development, so we are
learning together. However, Hiroki always helps me out because he
immediately notices the small details. He is also very open-minded and
imaginative, and suggests approaches that I would have never thought of,
which helps drive my work forward. With this robotics project, the screen
layouts he created for the robot are extremely well designed and
user-friendly.
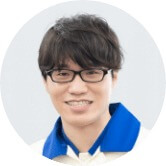
Since I transferred to this division in the fall of 2020, I am a newcomer to
the team, so I didn’t really understand what was going on at first. But
whenever I would ask Xiaoying a question, she would always give me a
detailed explanation. I am very thankful for her help, because once I
understood the current status of the project, I was finally able to offer up
my own opinions and contribute my own strengths as an engineer.
Moreover, I requested to be transferred to this division because I wanted to try my hand at things outside the realm of machine design. Despite still being inexperienced, Takahiro and our team leader give me a wide range of tasks so long as I show that I have a firm understanding of what needs to be done. I feel that this is because we trust and support each other as a team.
Moreover, I requested to be transferred to this division because I wanted to try my hand at things outside the realm of machine design. Despite still being inexperienced, Takahiro and our team leader give me a wide range of tasks so long as I show that I have a firm understanding of what needs to be done. I feel that this is because we trust and support each other as a team.
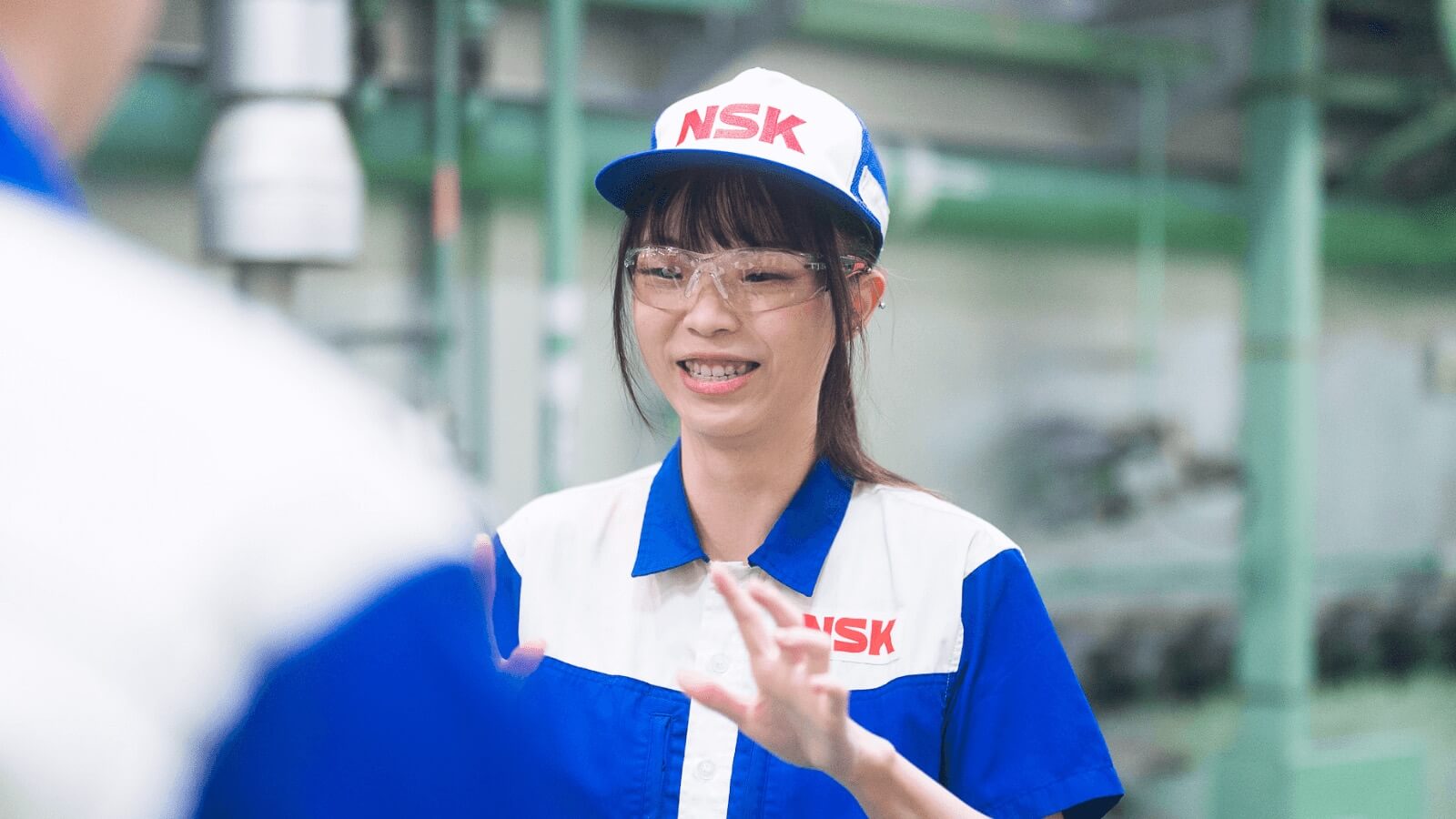
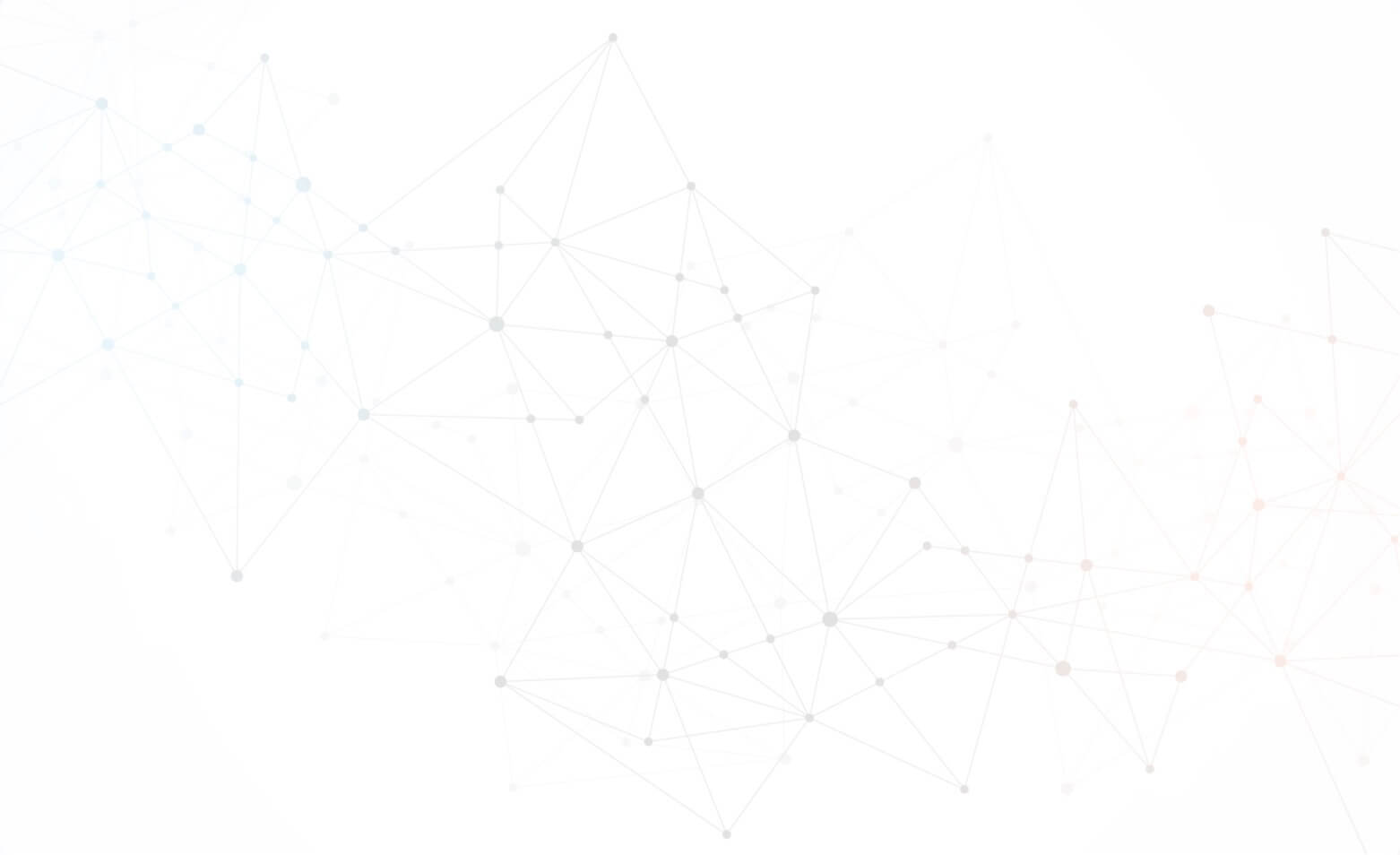
Is there anything you would like to thank your team for?
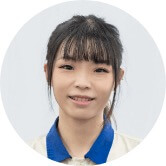
I am of foreign nationality, and it was my first time changing companies, so
I was a little apprehensive. However, everyone welcomed me into the team and
made me feel right at home.
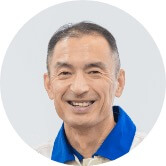
The culture and customs that someone is brought up with may be different
from your own, but I think that basically you should respect an individual
for who they are. Of course, NSK has a number of its own customs that it has
cultivated over the years, but these aside, I think we should eliminate the
mindset that we have to do things a certain way because this is Japan. So
for me, I have no intention of treating Xiaoying any differently than I
would anyone else. That being said, coming from a different background I
think that Xiaoying probably felt some pressure when she first joined the
team.
NSK may have a 100-year long history, but there are still practices that should be changed. That is why I aim to be open to the proposals that Xiaoying brings to the table, and leverage this to change NSK for the better.
NSK may have a 100-year long history, but there are still practices that should be changed. That is why I aim to be open to the proposals that Xiaoying brings to the table, and leverage this to change NSK for the better.
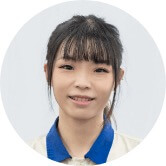
When I first joined the team, it took a bit to get used to each other, but
everyone was very welcoming and easy to talk to. Especially Takahiro. He
always checks our experiments and gives us advice when things don’t turn out
well, which encourages us when we feel like giving up!
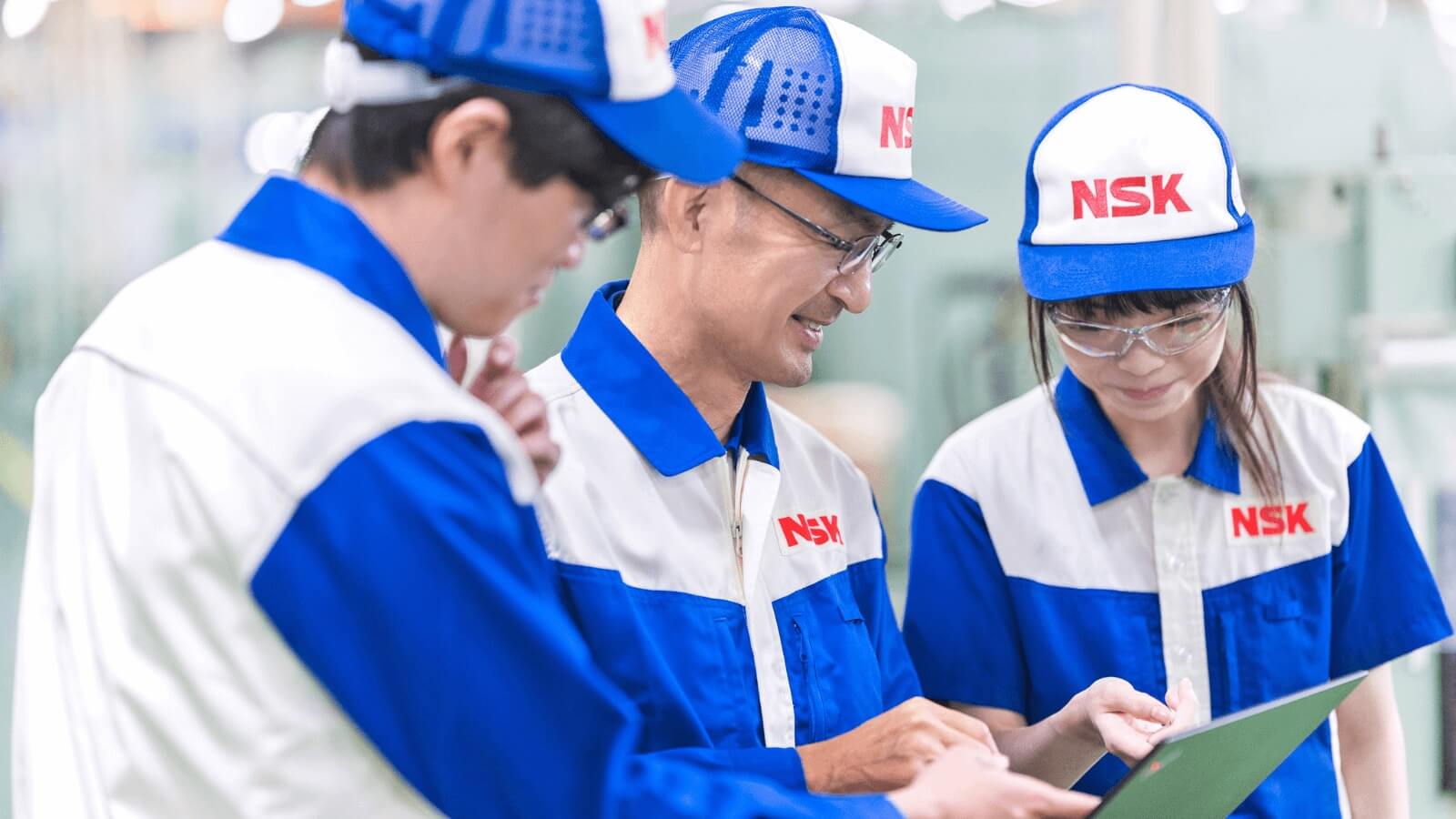
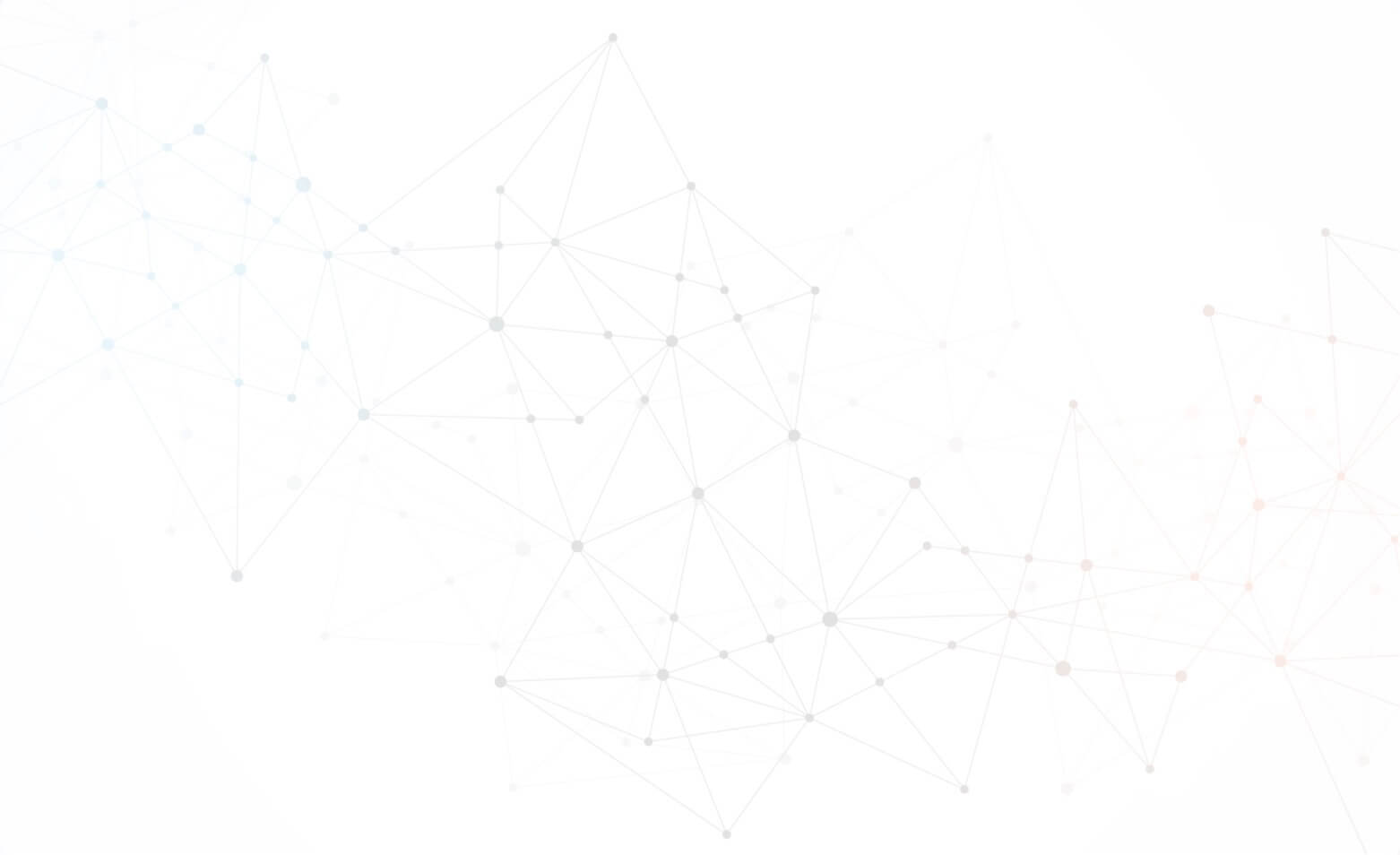
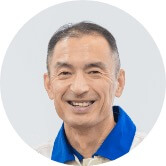
Our team’s job is to create new technology, so developing this equipment is
no simple task. When things continue to go wrong, you can’t help but feel
discouraged. But I try to interact with my teammates in a way that keeps
them positive because I want them to enjoy their work.
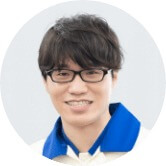
Takahiro is really easy to talk to. There are times when just explaining
what is troubling me to Takahiro helps me clarify the problem, and the
advice he gives me is sometimes the key to solving it. I’m very grateful.
Usually, I don’t think you get very many opportunities to speak with your
department head. But on this team, our supervisors will often drop by and
ask how everything is going. It puts me at ease knowing that they are taking
a keen interest in my efforts, and I also find it motivating.
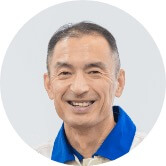
On this team, we always have to be quick to integrate the world's
cutting-edge technologies into the solutions we are developing. Moreover,
what is cutting-edge today, will become commonplace five or ten years down
the line. That’s why we have to look five years into the future and be
creative in coming up with new equipment. But that is what makes this job
hard—things don’t always go as planned because there are no precedents for
what we are trying to develop, and you have to rely on your team's expertise
and intuition to build something new. Nevertheless, I think that this
experience will certainly pay off when our young members like Hiroki and
Xiaoying are shaping the future of our plants five or 10 years from now. I
encourage them to take an interest in new ideas and continue challenging
themselves.