NSK Ltd.
Corporate Communications Department
NSK Develops High-Performance Bearings with Low Particle Emissions for Servomotors
New Grease and Seal Achieve Low Particle Emissions1, Long Life, and Low Torque
●Research using high-precision evaluative testing identified the mechanism behind issues, enabling effective improvements
●A newly developed grease and seal deliver twice the low-particle-emission performance of conventional products
●Helps maintain stable operation in industrial machinery such as industrial robots
1 Spread of contaminants from grease/oil scatter from the bearing
NSK Ltd. has developed a low-particle-emission, high-performance bearing that contributes to stable operation of industrial machinery such as industrial robots.
In fiscal 2024, NSK will begin accepting orders for samples of this new product, targeting annual sales of 1.5 billion yen in fiscal 2026. The new grease and seal developed for this bearing are not only for use in servomotors; they are finding applications to other products that require low-particle-emission performance, contributing to stable operation in a wide range of industrial machinery.

Servomotor and New High-Performance Bearing with Low Particle Emissions
1. Background
With smaller workforces and advances in industrial automation, the market for robot servomotors continues to grow. Servomotors used in robot joints operate in demanding conditions with high temperatures and sudden changes in speed. Even so, servomotors are key for precision response—they must accurately control robot movement, positioning, and speed.
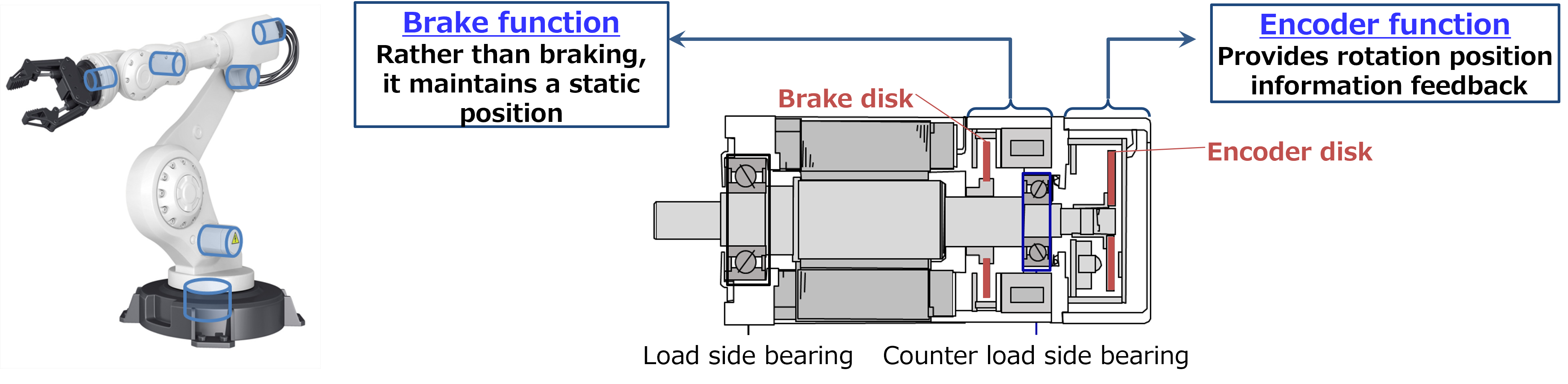
Example Bearing Locations in Servomotor for Robot
Bearings employed in servomotors are used near essential functional components for precision positioning such as encoders and brakes, but bearing grease and oil can scatter, sticking to the disks and causing contamination. This can lead to failures such as encoder read errors and slipping brakes, resulting in operation stops and downtime. Because of this, there is greater demand than ever for bearings with low particle emissions. NSK has addressed this need with scatter-resistant grease and seals that offer a high level of sealing performance.
Higher precision designs in recent robots and the growing market have created demand for even higher reliability in servomotors, driving the need for better particle-emission performance from bearings. However, there were multiple obstacles: the mechanism of disk contamination was unknown, and it was not possible to obtain high-precision assessments with conventional low-particle-emission performance evaluation and testing methods. In response, NSK applied its advanced technologies to realize high-performance bearings with low particle emissions.
2. Applied Technologies
1) Cause investigation for disk contamination mechanism
After inferring the mechanism behind disk contamination, NSK verified the phenomena using visualization and evaluative testing.
2) Higher precision evaluation and testing
Using NSK analysis technology for evaluative reproduction, NSK produced a test machine with a structure and environment similar to an actual servomotor. The machine produced precision test results, allowing the development of a product with superior low-particle-emission performance.
3) Innovation in design elements
Thanks to the clear understanding of the contamination mechanism and the advanced testing method mentioned above, NSK was able to identify elements that required improvement. As experts in controlling friction and wear, NSK used its tribology technologies cultivated over many years to develop grease and seals with superior low-particle-emission performance.
3. Features
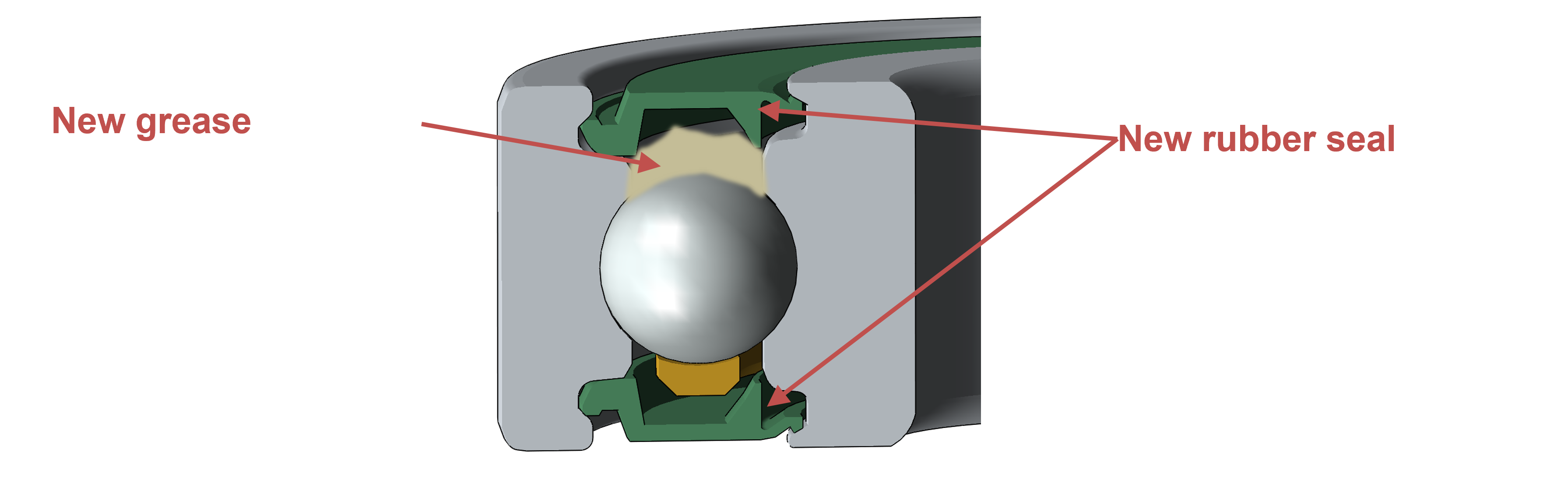
New Structure to Reduce Particle Emissions
The new grease and seal deliver twice the low-particle-emission performance as conventional products. The grease also lasts much longer, while the seal provides lower torque.
1) New grease: Formulated to resist evaporation in high-temperature environments and offer superior thermal resistance, resulting in:
● Low-particle-emissions: Twice the performance of conventional products
● Enhanced resistance to seizure: Double the conventional lifespan
2) New rubber seal: A new design for the lip where the seal contacts the inner ring helps to achieve:
● Low-particle-emissions: Less than half the grease scatter of conventional products
● 10% lower torque: Lower contact friction between the seal and inner ring than conventional products
About NSK
NSK began its journey manufacturing the first bearings in Japan in 1916, and has since developed into a global organization researching, designing, and manufacturing Motion & Control™ solutions essential for mobility and industrial applications. NSK is the top supplier of bearings in Japan and is the third largest supplier in the world by market share.
Our responsive products and technologies enhance automotive performance and industrial productivity while reducing energy consumption to unprecedented low levels. In the early 1960s, we set our sights outside Japan and have established over 200 business locations in 31 countries alongside a vast network of joint ventures and partnerships in all corners of the world.