World-leading Performance for EV Motors: NSK Bearings Step-up to Meet the Challenge of Ultra-High-Speed Rotation
Many companies are engaged in a variety of initiatives to realize a sustainable society. The automotive industry has made great strides in popularizing the electric vehicle (EV), which has a low environmental impact, but there are still significant challenges to achieve widespread adoption. Today, we talk to NSK engineers about the challenges in developing bearings for EV, and how bearings are helping take EV technology to the next level.
Profile
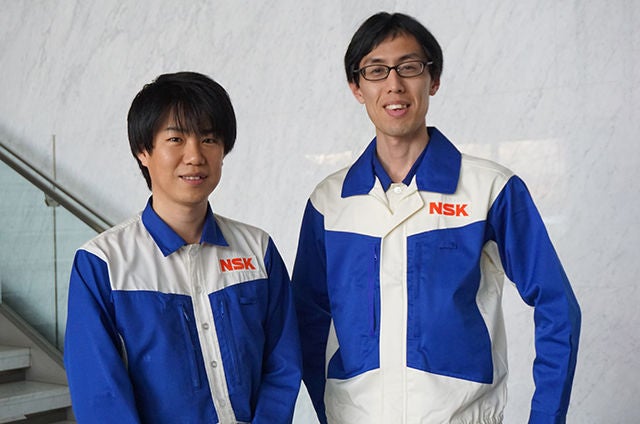
Yasuhiro Iwanaga (left)
Coordinator
Powertrain Bearing Technology Department
Automotive Powertrain Bearing Technology Center
Yoshimune Shimokawa (right)
Powertrain Bearing Technology Department
Automotive Powertrain Bearing Technology Center
What do EV need from component makers?
Iwanaga The new movement in automotive technology called CASE* has created a push in the automotive industry to electrify the constituent components of each sub-system in vehicles. Among the various types of EV, which include fully-electric vehicles and plug-in hybrids, there is one common challenge: consumers want to be able to drive longer distances on a single charge. Maximum range depends on vehicle weight, efficiency, and battery capacity. Accordingly, a key task for the industry is to downsize components, thereby reducing weight or creating space for additional battery cells. The motor is no exception. By reducing the size of the motor, the vehicle becomes lighter, and it can travel farther using less power. However, when you shrink the size of the motor, it cannot produce the same amount of power if it keeps rotating at the same speed as before. So as the motor gets smaller, the only thing that we can do to maintain power is to increase the rotational speed. Not only does this require us to reduce the size of the bearings and other components used inside the motor, but it also requires the components to be able to handle rotation at much higher speeds.
*CASE: Connected, Autonomous, Shared & Services, Electric
1985: Top team in Japan
2019: First place in Second Division
2020: Back in First Division
Endo The Brave Bearies are based at Ishibe Plant in Shiga Prefecture. This year is the 49th year since the team’s establishment. With the help of the company, the team members work at the plant in the mornings and practice softball in the afternoons.
Matsuda In my daily work, I’m in charge of data entry and clerical work, such as restocking and organizing plant equipment. The other players are also responsible for product inspection, quality control, general affairs, etc.
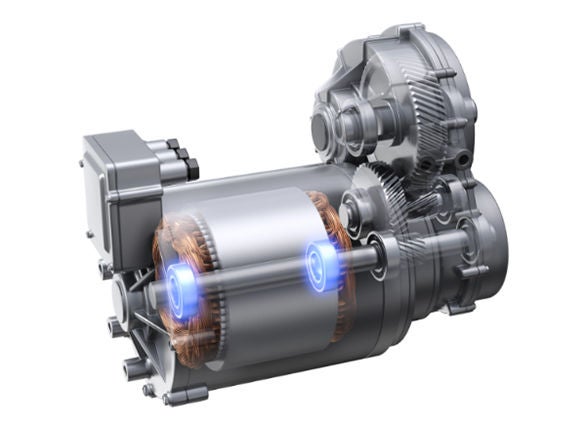
Example bearing placement in EV motor
Shimokawa From an environmental perspective, making the motor and other EV components smaller and lighter enables us to utilize the freed-up space for additional battery cells. This improves fuel and power consumption and increases the vehicle's running distance on a single charge, resulting in EV appealing to more consumers and ultimately leading to a positive contribution to the environment, such as through lower EV life cycle CO2 emissions.
The many types of EV
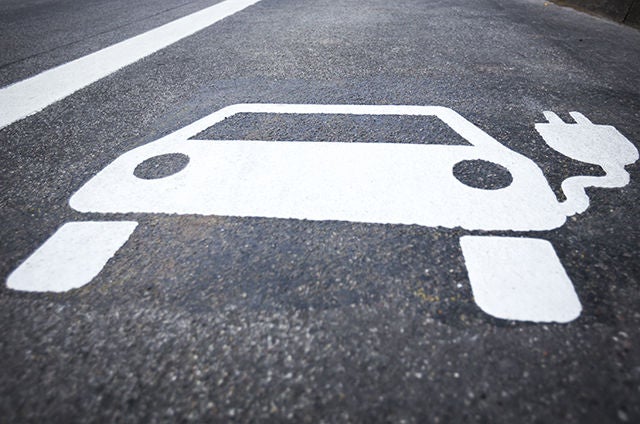
EV:Electric Vehicle. Entirely powered by an electric motor.
HV:Hybrid Vehicle. Has both an electric motor and a combustion engine. Switches between one or the other, or uses both at the same time. In conventional hybrids, the battery can't be charged using external sources; it's charged using energy converted from the combustion engine, or from regenerative braking.
PHV:Plug-in Hybrid Vehicle. Same as a hybrid, but can also be charged from an external source of electricity. Offers the benefits of an electric vehicle, but can also travel long distances more easily since you can fill up on gas as needed.
FCV:Fuel Cell Vehicle. Has “fuel cells” which use a chemical reaction between hydrogen and oxygen to create electricity and power an electric motor.
Combining multiple new technologies was no easy task, but overcoming the challenge is how we delivered a world-leading product
Iwanaga NSK has experience developing products to support motors of increasingly high speeds, but our new development team, specializing in next-generation high-speed products, was launched two years ago. The first product we developed was the Ultra-High-Speed Ball Bearing for EV Motors announced in March of this year. At the time of announcement, this bearing was the world's fastest grease-lubricated bearing for use in EV motors (March 2020, based on in-house findings), with a dmN* that is about 2.5 times higher than that of conventional products.
*dmN: An indicator expressing a bearing's rotational performance calculated as bearing pitch diameter (dm) x rotational speed (n).
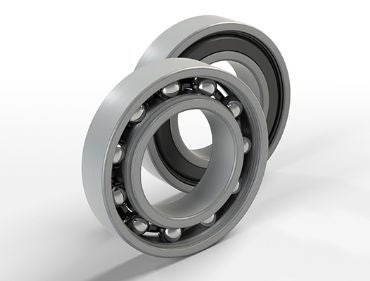
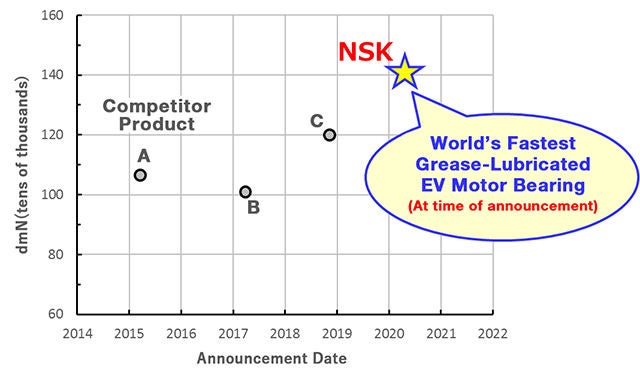
How does our new product compare?
Shimokawa As a bearing's rotational speed increases, so too does the heat generated inside of the bearing, making it difficult to maintain an oil film to reduce friction. As this state progresses, excessive heat causes the surfaces of the elements in contact (balls, cage, rings) to soften and melt, causing the bearing to seize. To address this issue, we decided to use an original grease developed by NSK that can withstand the heat generated by high-speed rotation. This grease allows an oil film to form even during high-speed operation, thereby preventing bearing seizure and extending the product service life beyond that of conventional products. An extension of the bearing's service life means an extension of the life of the motor, which ultimately contributes to resource and energy conservation.
Bearings also have a component called a cage which fixes the position of the bearing's rolling elements (balls or rollers) to prevent them from colliding with one another. When rotated at high speeds the cage (undesirably) deforms due to centrifugal force. When a cage excessively deforms, it rips apart and the bearing is destroyed. As such, in developing this bearing for EV motors which spin at extremely high speeds, we also needed to completely rethink both cage design and materials to create a new cage capable of withstanding the intense stress and centrifugal force.
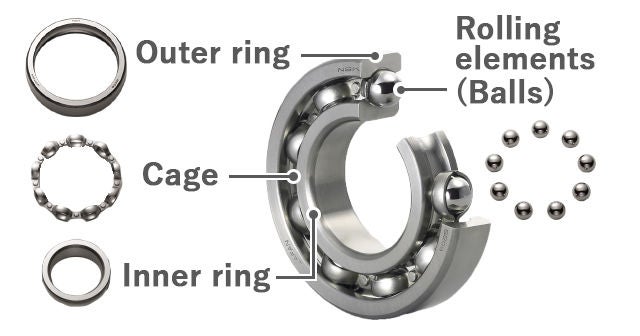
Ball bearing structure
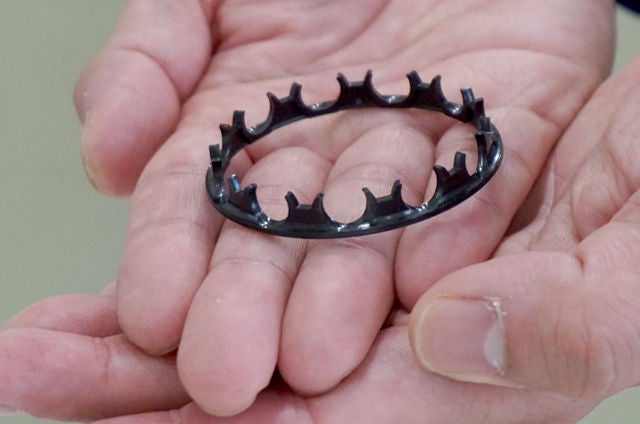
New cage design and materials to withstand even higher-speed rotation
Since there were many new elements in developing this bearing, such as the design and materials used for its components as well as the grease, there was a high level of difficulty in this development project — adding even just one new element is complex, but adding three at the same time really made us work. However, despite encountering repeated failures and roadblocks, we were able to learn from our mistakes and create the product we have today. During this process we leveraged the experience and technological prowess that NSK has built up over the years, and it felt great to see the cutting-edge work from many departments crystallize into a real product delivering new value to market.
Iwanaga Collaboration with other divisions was essential to the realization of this product. Even outside of the automotive industry the need for electrification and higher-speed products is increasing, and at NSK there are divisions other than our team that are developing products to meet these conditions. We drew from the knowledge and expertise of these divisions as we worked through the development process. The existence of in-house teams researching NSK's Core Technologies, which serve as the foundation supporting all of the technologies that NSK develops, also played a major role in securing the analysis and evaluation resources and know-how required to make this project a success. As the goal of this development project was to achieve 1.4 million dmN with a grease lubricated bearing for motors, something no company had achieved before, we didn't have the testing equipment or evaluation technology to handle such a high speed. Accordingly, we collaborated with the evaluation team to develop testing equipment in parallel with the development of the bearing. I think that it was this inter-departmental development process involving numerous divisions that enabled us to complete this product in an extremely short period of time.
Sharing knowledge to create products needed by society
Shimokawa I want to share the knowledge we gained and discoveries we made through the course of this project with other divisions and add them to NSK's overall knowledge base so that we can leverage them for future development projects. I believe that this knowledge can be applied to technologies used outside of automotive products such as products for machine tools where the need for grease-lubricated bearings that can operate at higher speeds is also increasing.
Our competitors will also be rapidly developing new products in response to highly demanding requirements, and I want to push forward with product development so that NSK can stay ahead of the competition. We will work so that our development efforts spark further innovation at NSK.
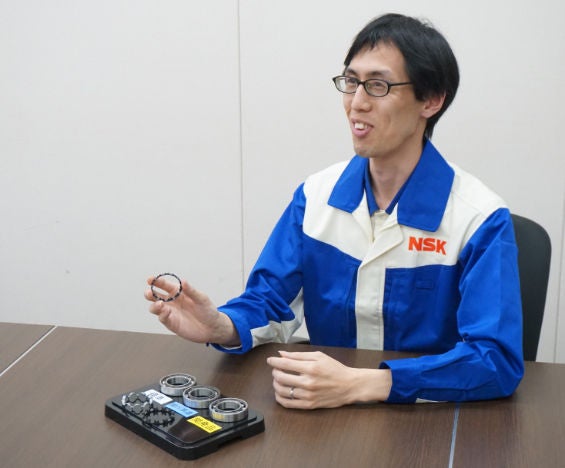
Iwanaga I want to leverage NSK's technological capabilities to develop new methods of using bearings and grease, and strengthen our ability to provide solutions to our customers. In order for the solutions we provide to our customers to be seamlessly integrated into their operations, we are striving to fully understand the customer's requirements and method of assessing and selecting candidate components, as well as their evaluation process required for the component to be included in a vehicle that hits the market. We will continue to develop products that are needed by society and satisfy end users, so that our customers always turn to NSK for innovative solutions and can choose us with confidence.
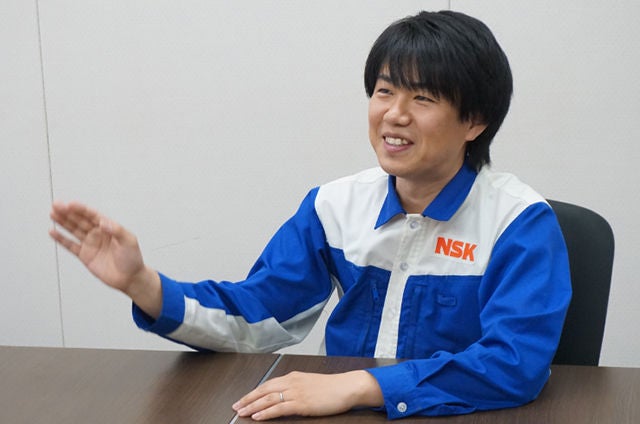
[Related article]