Driving, Steering, and Braking for the Future of Safe and Comfortable Mobility
The future evolution of the technology underlying automotive performance.
Profile
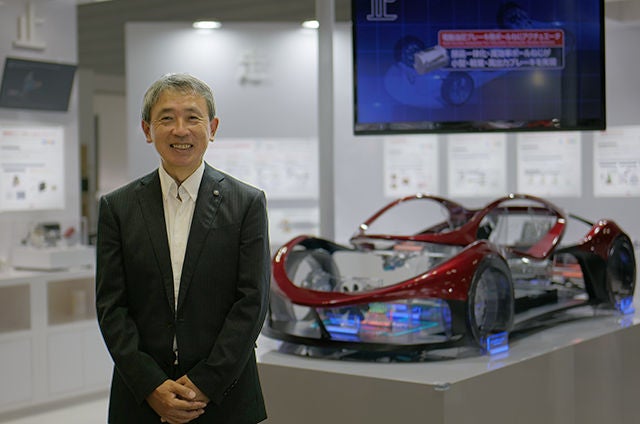
Eiji Inoue
Head
Automotive New Product Development Department
Driving, Steering, and Braking Define How Vehicles Move
I think of my car as “a means to go where I want.” Fundamentally an automobile is designed to turn (steer) freely, stop (brake) whenever you want, and accelerate (drive) you safely to your destination, wherever it is. These functions, driving, steering, and braking, are known as the three major elements of automotive motion.
Driving is an automobile’s most basic function. The power generated by the engine, motor, or other power sources is transmitted to the wheels, moving the car and achieving acceleration along with any other desired movement by the driver.
Steering is a function that transmits the driver’s movement of turning the steering wheel to the wheels to change the direction the vehicle is going. Significant changes in steering systems are expected in the future with the development of autonomous driving.
Braking is a function that applies force to the wheels when the driver steps on the brake pedal to slow the car down and bring it to a stop. To further improve safety, automakers are pursuing electrification of braking systems.
All of these elements are essential for safe and comfortable driving, and require a very high level of reliability for use in automobiles.
Technology that Supports Driving
In order to drive at the desired speed, a transmission (gearbox) is needed to regulate power between the engine and the wheels. The transmission optimizes the wheels’ rotation speed and torque (magnitude of load), much like shifting gears on a bicycle. In a conventional, engine-powered vehicle, fuel is burned by the engine to produce energy for driving. It requires greater torque at slower wheel speeds, such as starting to move from a standstill, than when already on the move. Thus, the transmission is responsible for adjusting the relationship between the engine, wheel speed, and torque according to situation. In other words, it shifts gears smoothly and flexibly.
The biggest challenge in driving is reducing energy loss. It takes a lot of energy to run passenger vehicles, which typically weigh over one ton. To reduce CO2 emissions and minimize environmental impact, society demands vehicles that run on less energy. Many technologies have been created for this purpose. For example, automatic transmission (AT) is a mechanism that has evolved remarkably. Automatic transmissions have gained a greater number of speeds, going from three gears about 30 years ago to eight or even ten gears today. This allows the balance between RPM and torque to be finely adjusted, so that the engine's power can be transmitted more efficiently to the wheels, reducing fuel consumption and vehicle wear and tear.
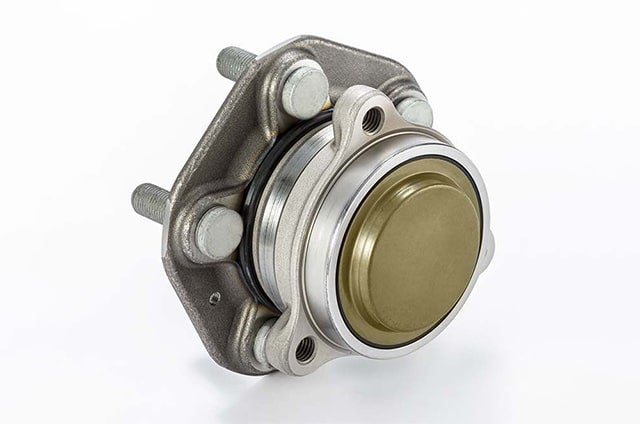
Low Friction Hub Unit Bearing for EV
In addition, to reduce energy loss, frictional force must be reduced in the rotating parts of the force-transmitting components. A wide range of the NSK Grou’s products are used in automatic transmissions, including bearings to reduce friction as gears turn and friction material products. Hub unit bearings are used in the wheels to support the weight of the car when driving and the lateral forces applied when turning. They must have durability and reliability in various environments such as rainwater, mud, and snow, and provide smooth rotation.
On the other hand, no matter how efficient the engine is, it consumes more than twice the amount of energy than, theoretically speaking, is needed to drive the car. This is why features have been incorporated to reduce how much the engine runs, including a feature that turns off the engine when idling. The electrification of vehicles is also progressing. For example, there are hybrid vehicles (HEVs) that use both an engine and electric motor, recovering the vehicle’s kinetic energy when decelerating and reusing it as electrical energy, as well as electric vehicles (EVs) that run on motors powered solely by electricity.
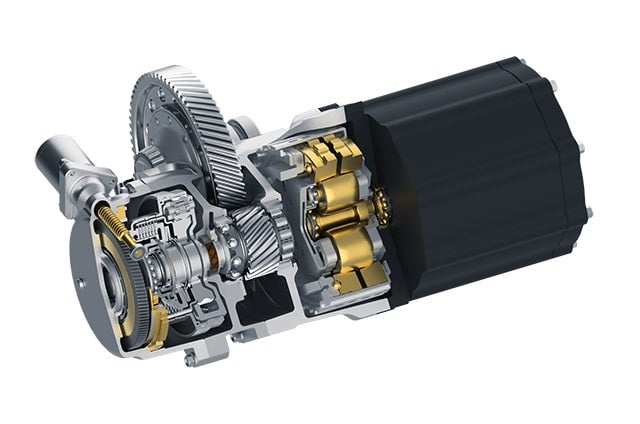
Seamless 2-Speed e-Axle Concept (Gen2) helps solve the issue of EV cruising range
One of the challenges in EV driving is the cruising range under battery power. To drive a long distance on a single charge, a large number of batteries must be installed, and space must be secured to carry the batteries. Consequently, there is a need to reduce the size and weight of various components used in automobiles. To get high power from a small motor, it must rotate at high speed. For this, bearings and reduction gears are required that can withstand high speed rotation. Converting battery energy more efficiently and using less energy to drive the car will also increase the cruising range. NSK’s solution to this problem is the Seamless 2-Speed e-Axle Concept (Gen2). Drawing on multiple technologies that NSK has cultivated over the years, this new product is capable of quiet and smooth gear shifting while saving space and supporting higher motor speeds for a comfortable ride.
Technology that Supports Steering
When a driver turns the steering wheel, force is transmitted from the base of the steering wheel to the wheels by a thin, rod-like part, allowing the car to turn. The components that convey force from the steering wheel to turn the wheels as the driver intends constitutes the steering system.
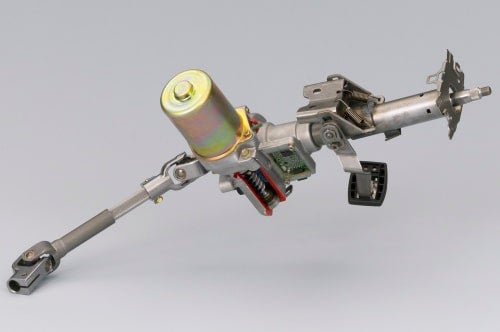
Column type EPS
The steering system is another product that has become increasingly electrified. If a car is equipped with hydraulic steering, it will constantly use energy to generate hydraulic pressure, even when the steering wheel is not moved. At the same time, cars equipped with electric power steering (EPS), in which the steering is driven electrically, use a motor for assistance only when necessary, thus reducing energy consumption. In the column type EPS that NSK specializes in, a component, the torque sensor, is attached to the base of the steering wheel. The sensor reads how the driver wants the car to move and transmits this information to the wheels.
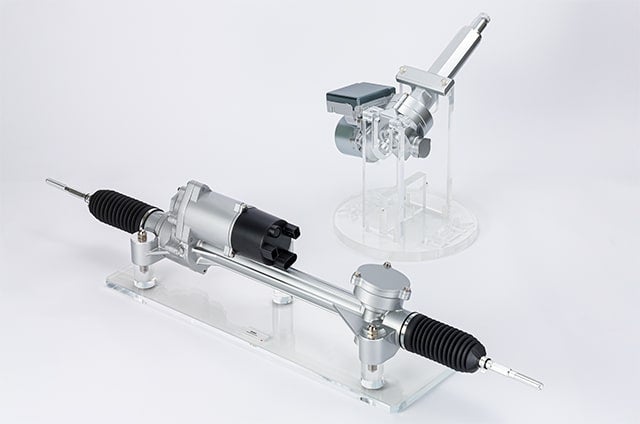
Steer-by-Wire systems for autonomous driving
Autonomous driving technology has also been advancing recently. As we change to an autonomous driving society, the way drivers interact with automobiles is going to change. In the future, we may see cars with steering wheels stowed away except when needed, or cars without steering wheels at all. Currently, the steering wheel and the road wheels are mechanically connected by a steering mechanism. But I expect that in the future, the steering wheel and road wheels will be mechanically separate, and a system in which the steering direction is transmitted by electrical signals (steer-by-wire) will become mainstream. As products intended for automated driving, NSK is developing its Steer-by-Wire systems using the EPS technology it has cultivated to date. Since there is no mechanical connection between the steering wheel and the road wheels, the system can isolate unpleasant vibrations from the road surface and avoid hazards through autonomous driving control. In this way, we are working to deliver new value.
Technology that Supports Braking
When a driver presses the brake pedal, the car slows down and stops. To achieve enough stopping force for any situation, the driver’s pressure on the brake pedal is amplified and transmitted by a component called a brake booster. The hydraulic force generated by the amplified power moves the brake pads, which pinch and tighten on a rotating part of the wheel, creating a braking force that stops the automobile.
Conventional, gasoline-powered vehicles use vacuum pressure created when the engine is running to power the brake system. However, HEVs have times when the engine is not running, and since there is no engine at all in EVs, engine-generated vacuum power is not available. Because of this, braking components are increasingly electrified in HEVs and EVs.
Moreover, in recent years, an increasing number of vehicles have been equipped with automatic emergency braking (Advanced Emergency Braking System, AEBS). Automatic emergency braking is gradually becoming mandatory in Japan from 2021, in the EU from 2022, as well as in other countries, making it a technology that will be indispensable in the future.
Electric brakes use a ball screw actuator for electric-hydraulic brakes. These incorporate ball screws, for which NSK has top-level share globally. The ball screw component is well suited for precise control of force due to its high efficiency of movement and high responsiveness, contributing to the advancement of safe drive technology.
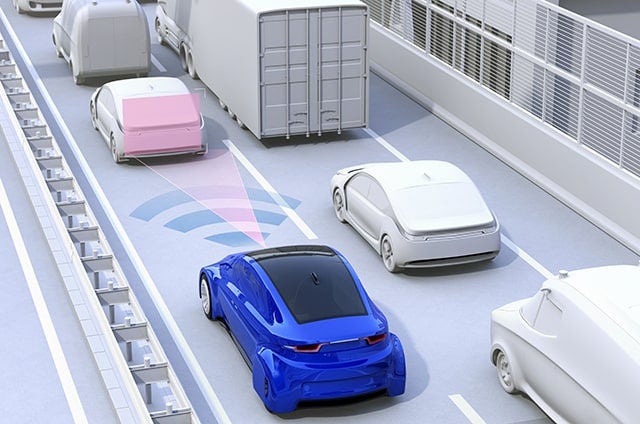
Automatic control systems are being introduced, even in braking
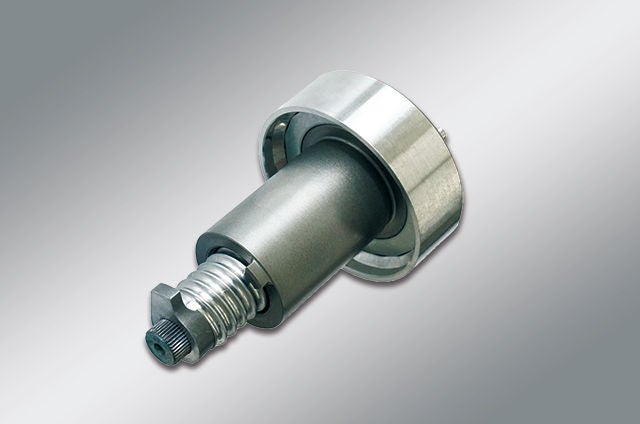
The ball screw actuator for electric-hydraulic brakes contributes to the electrification of braking
Aiming to Help Realize a Sustainable Mobility Society
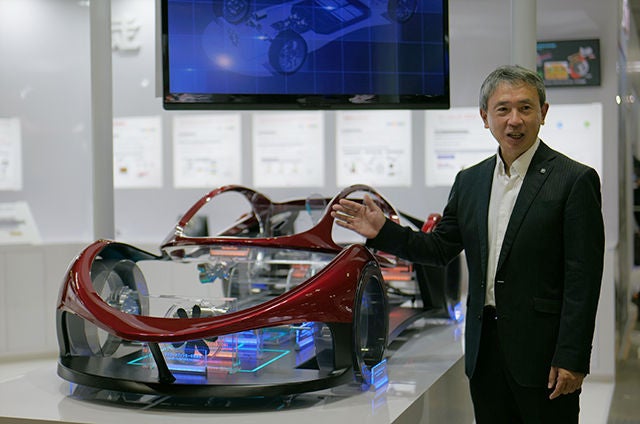
To date, NSK has developed many products that have supported the evolution of automobiles. Going forward, we will continue developing products and technologies that contribute to the electrification of driving, steering, and braking. Electrification is expected to save energy because it enables energy to be used only when needed. It also improves safety and accident prevention, since electricity can be used to implement various controls. It is clear that the environment surrounding cars is changing rapidly, not only in terms of electrification, but also in terms of CO2 emission reduction and safety improvements. I want us to step out of our conventional product framework and create products that respond to the needs and changes in society. We will work to help realize a sustainable mobility society while considering both drivers’ and passengers’ peace of mind and pleasure.
NSK Stories related to automotive technology:
- World-leading Performance for EV Motors: NSK Bearings Step-up to Meet the Challenge of Ultra-High-Speed Rotation
- Setting the Future in Motion with New Ball Screw Units for Advanced Braking Systems: Part 1 (Strategy)
- Setting the Future in Motion with New Ball Screw Units for Advanced Braking Systems: Part 2 (Product Design)
- Setting the Future in Motion with New Ball Screw Units for Advanced Braking Systems: Part 3 (Manufacturing)