World’s First! Highly Accurate Prediction of Rolling Bearing Life Applying Ultrasonic Testing
After years of research and development NSK is revising-up the basic dynamic load rating of many bearings to up to double the equivalent rolling contact fatigue life (with no change to design and materials!).
You may be surprised to learn that the fundamental formulas we use today to calculate bearing life are more or less the formulas defined in a 1962 report by the International Federation of the National Standardizing Associations (ISA), the precursor to the International Organization for Standardization (ISO). Today, the formulas are codified as the ISO standard “ISO 281:2007 Rolling bearings — Dynamic load ratings and rating life.”
In 2023, over 60 years later, we have learned a thing or two more about calculating and predicting bearing life, and the materials and methods we use today have advanced by leaps and bounds so it is probably about time we reconsider how we evaluate rolling bearing life.
With the standard remaining static for so long, NSK is the first company in 60 years to make a significant breakthrough in bearing life calculation that can improve productivity and contribute to environmental protection. In this article we talk to the NSK researchers and engineers that developed an all-new highly accurate method of calculating bearing life and learn why NSK is refreshing its approach and updating the catalog life rating of many of its products.
Profile
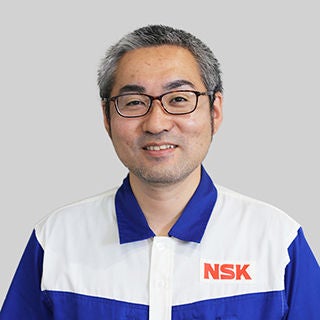
Hiroki Komata
Chief Engineer
Core Technology R&D Center
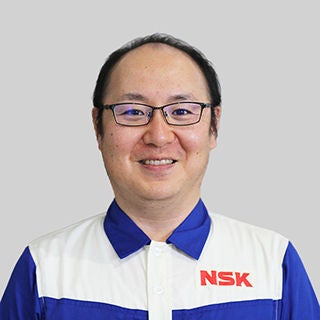
Sho Hashimoto
Group Manager
Technology Development Division HQ
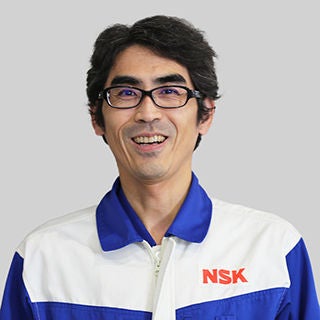
Masakazu Kawada
Senior Manager
Industrial Bearing Development Office
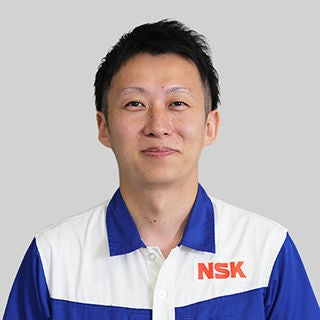
Tomoki Doshida
Coordinator
Core Technology R&D Center
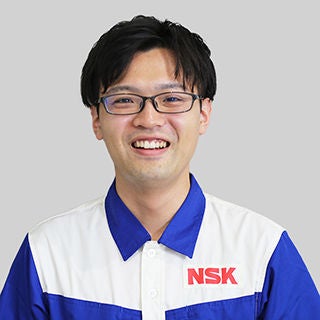
Keita Yamada
Technology Development Division HQ
A New, More Accurate Indicator of Bearing Life
Komata The theory underlying the ISO standard for calculating bearing life was developed in 1962 but bearing and material technology has advanced considerably since then. About 20 years ago, NSK noticed a growing gap between the bearing life calculated in the ISO standard and the actual bearing life verified by endurance testing, and we began a more detailed study of the subject.
At that time, around when the research began, we confirmed that the life of NSK bearings was approximately 20 times longer than the life expected under ISO standards. And today, in 2023, the life of NSK bearings can be more than 50 times longer than the catalog life rating based on ISO. Erring on the side of caution is certainly fine, but longer bearing life can be used beneficially to protect the environment and improve production efficiency for example by reducing the frequency of replacement and the amount of waste.
The ISO bearing life calculation formula emphasizes the effect of lubrication conditions. Of course, lubrication greatly affects bearing life, but lubrication technology is much better today than it was in 1962. Our research has demonstrated that under well-lubricated conditions, the composition and quality (the amount of impurities) of the bearing steel is a more accurate indicator in predicting how long a bearing will last in its application.
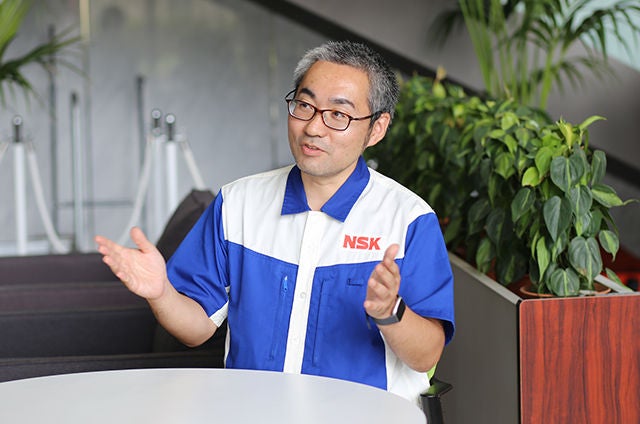
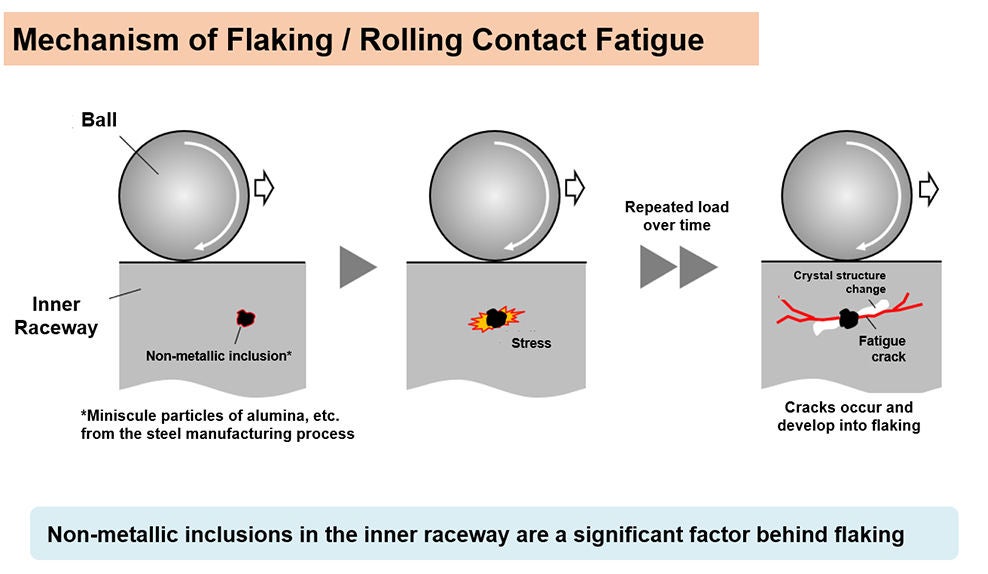
From Theory to Real World Application
Hashimoto We knew empirically that under a favorable lubrication environment, NSK bearings last much longer than their catalog life, and we also knew that this was due to improvements in material quality and manufacturing technology. In particular, it was well known that impurities (non-metallic inclusions) in the steel material had a very significant effect. While this was very beneficial from the standpoint of developing long-life bearings, the technology for accurately predicting life had not kept pace. However, as we continued our research, we realized that an evaluation method based on fracture mechanics could provide more meaningful insight.
Although we did not have much knowledge of fracture mechanics at that point, we were able to accelerate the development of the technology through an open innovation project with Kyushu University. The result was a quantitative evaluation method that determined which factors influence the process of crack propagation to what extent in a material, which was one of the key points in establishing a technology to predict bearing life with high accuracy. As a result of this research, we were able to quantitatively reflect the effects of non-metallic inclusions on bearing life in the bearing life prediction equation.
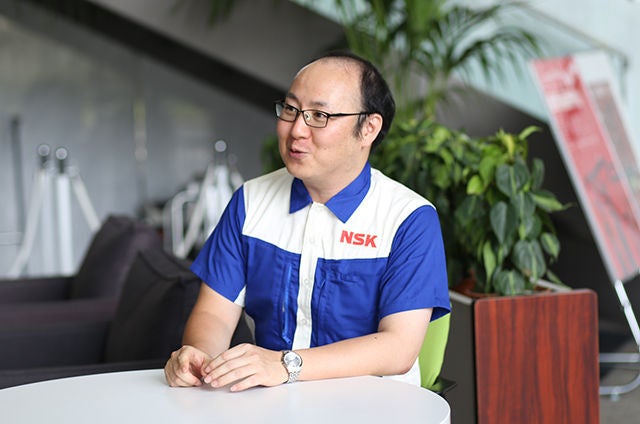
The professor who guided our research filled in the gaps in our knowledge and thinking. This helped us clarify our research policy and landing point, which also increased the speed of our development. In addition, thanks to dramatic improvements in computer processing power, we were able to perform many high-load simulations and computer analysis in a short period of time, which accelerated the development of our quantitative evaluation method. Although we were confident in the persuasiveness of the hypotheses we had developed, we needed solid data to back it up.
Ultimately, our quantitative method and understanding of the phenomena were validated through extensive and varied endurance life tests. Although fracture mechanics was a very effective approach for quantitatively evaluating crack propagation from impurities, which is the dominant factor in determining bearing life expectancy in well-lubricated conditions, it was a great challenge to incorporate it into life prediction methods on a practical real-world level. By combining the method we developed with an ultrasonic inspection technique that scans the non-metallic inclusions in a large volume of steel, we were able to predict the life of NSK bearings with much higher accuracy.
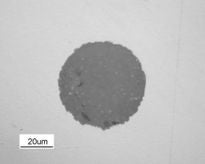
Non-metallic inclusions (impurities in steel) are often just a few tens of micrometers in size
Analyzing 3000 Times the Volume of Steel in One-Fifth the Time
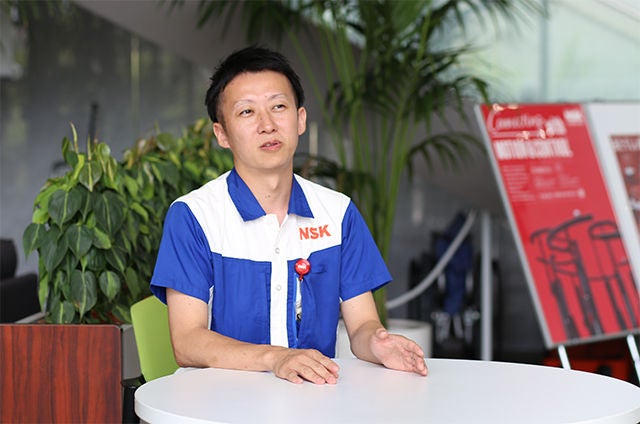
Doshida Steel materials inevitably contain impurities (non-metallic inclusions) and have a certain degree of variation from batch to batch. Therefore, unless NSK could develop a method to more accurately measure the amount and size of non-metallic inclusions in the steel materials it procures, it would not be possible to put highly accurate life prediction technology into practical real-world use.
Conventional inspection methods involve cutting and polishing slices of steel, observing under a microscope, and visually counting the number of non-metallic inclusions. While this method is commonly used in the industry, it is time-consuming and only inspects a small portion of the steel, making the resolution of analysis inadequate for a new life prediction method. We explored a number of alternatives and considered the possibility of using the Micro-UT method (ultrasonic testing) to inspect a large volume of steel in a short period of time.
However, NSK had no precedent for using ultrasonic waves to detect non-metallic inclusions as small as several tens of micrometers in steel. Therefore, we began our technological development by confirming whether non-metallic inclusions were really present at the locations detected by ultrasonic testing. In addition, it was very difficult to analyze the ultrasonic testing data in order to accurately estimate the size of each non-metallic inclusion, which were just several tens of micrometers in size. After many tests, including optimization of ultrasonic testing conditions and manual measurement of the actual dimensions of a large number of the detected non-metallic inclusions, we were able to establish a technique to accurately estimate the size of non-metallic inclusions from the ultrasonic testing data. With the establishment of the new inspection method, it is now possible to nondestructively inspect more than 3,000 times the volume of steel compared to conventional microscope methods in one-fifth the time and to obtain highly reliable data on the amount and characteristics of non-metallic inclusions.
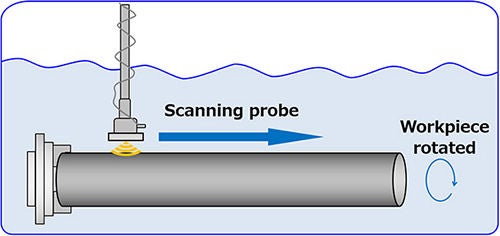
Diagram of Micro-UT method (ultrasonic testing to detect non-metallic inclusions)
Another challenge we faced was the rapid deployment to NSK technology centers around the world. After close communication with each center to verify that the new method could meet a diverse range of needs, we were able to deploy new testing systems globally in less than two years. As a result, the new ultrasonic testing method is now being used not only for materials procured in Japan under the jurisdiction of the Core Technology R&D Center, but also for steel materials at each site globally under the jurisdiction of each region’s technology center.
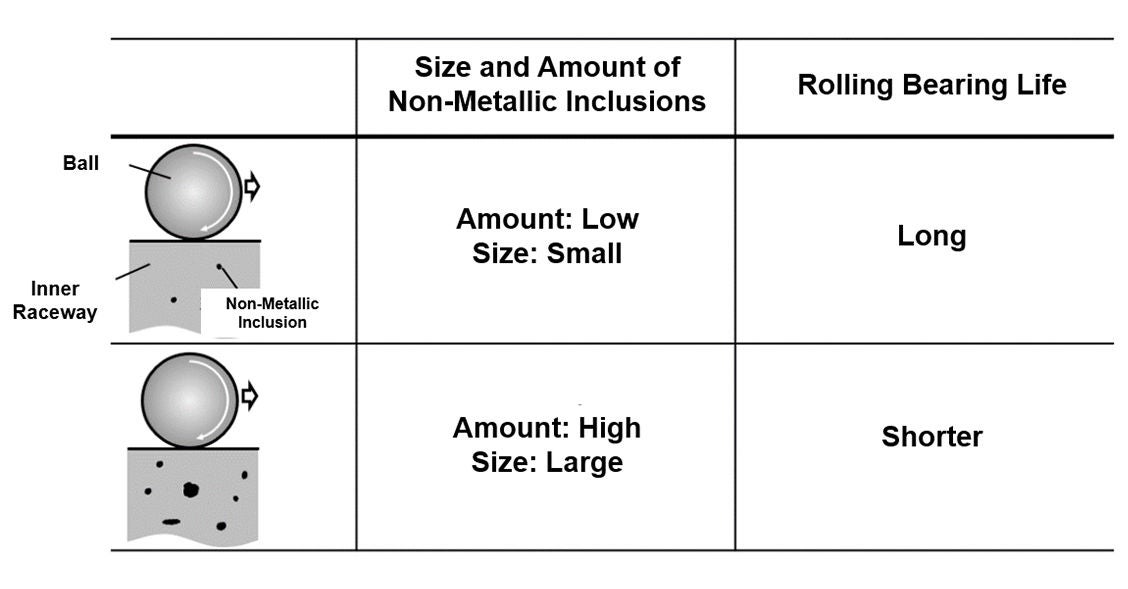
Product Quality and Reliability Underlies Every Facet of our Society
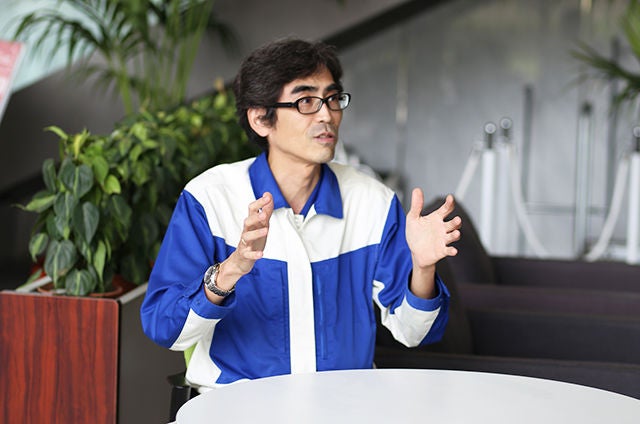
Kawada NSK has plants all over the world and procures steel from a variety of sources around the globe and ensuring the quality of NSK products can mean the difference between life and death. If a car on the highway or a high-speed train suddenly breaks down, the consequences could be disastrous. Another example is that much of our energy generation, from wind turbines to hydroelectric and thermal power generation, uses bearings under extremely harsh conditions of high loads and high temperatures. A bearing failure in our energy infrastructure can mean power outages for thousands of homes.
Product quality is driven by the quality of the material. Impurities in steel are a major factor affecting bearing life, and the new method applying ultrasonic testing makes it possible to determine the size and quantity of non-metallic inclusions in a wide range of steel materials in a short time, which can then be statistically analyzed to control NSK's steel products.
Making it Easy for Customers to Utilize
Yamada This high-precision life prediction technology has made it possible to quantitatively demonstrate the long-life performance of NSK bearings. However, there are various factors that must be carefully considered to make it easy for customers. Therefore, we will review the basic dynamic load rating, which is a parameter for bearing life calculation in the catalog, so that the long-life performance of NSK bearings can be simply applied in customers’ machine design. NSK’s current bearing catalog contains a very large number of bearing types, and the applications and conditions of use by our customers are also diverse. In order to ensure that many customers can use NSK bearings with confidence, we are reviewing the basic dynamic load ratings in consideration of an appropriate safety margin. At the same time, it is important to fully promote the strengths and high quality of NSK products to new customers, as catalog data is one of the factors that help customers choose NSK products.
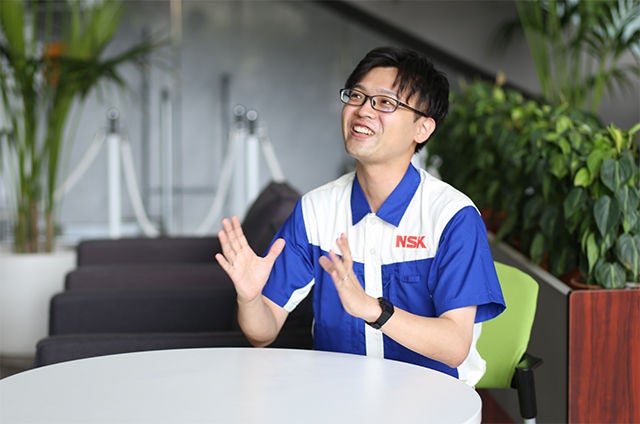
Clear Communication is Key
Hashimoto If catalog data for an existing product is suddenly updated and our customers are abruptly notified that the product will last 20 times longer than before, there could be a lot of puzzlement and skepticism. It is our job to concisely explain to our customers that we are updating our catalog data based on a well-researched methodology supported by extensive empirical data, and that the updated values are well within the safe and secure range. Moving forward, we will continue to develop this technology and new technologies to meet the needs of our customers and society.