Resource Circulation
1.Resource Conservation and Recycling Measures
NSK’s Approach | Targets and Performance | Initiatives |
2.Utilization of Water Resources
NSK’s Approach | Targets and Performance | Initiatives |
1. Resource Conservation and Recycling Measures
NSK’s Approach
The NSK Group is promoting efforts at each stage of the supply chain to enhance the 3Rs (reduce, reuse, recycle) through the development of environmentally friendly products and efficient, waste-free production, all in pursuit of realizing a circular economy. In its development and design divisions, NSK focuses on reducing product weight and extending service life while developing products that are manufactured with minimal raw materials and are easy to recycle after use. Procurement divisions work in collaboration with suppliers to procure environmentally friendly parts and raw materials, including steel materials made from recycled scrap metal. In manufacturing divisions, efforts are made to reduce resource waste by improving material yield through process improvements and refinements to tools and molds. In addition, NSK collaborates both internally and externally with suppliers to recycle metal and grinding waste generated during production back into steel, while also promoting water recycling and waste liquid treatment to reduce waste emissions and improve recycling rates. Our logistics divisions contribute by reducing waste emissions through the repeated use of packaging and wrapping materials. Moreover, NSK ensures the proper disposal of waste by conducting voluntary inspections at its business sites, carrying out on-site verifications of companies entrusted with waste disposal, and enhancing management practices using information systems to prevent any compliance violations.
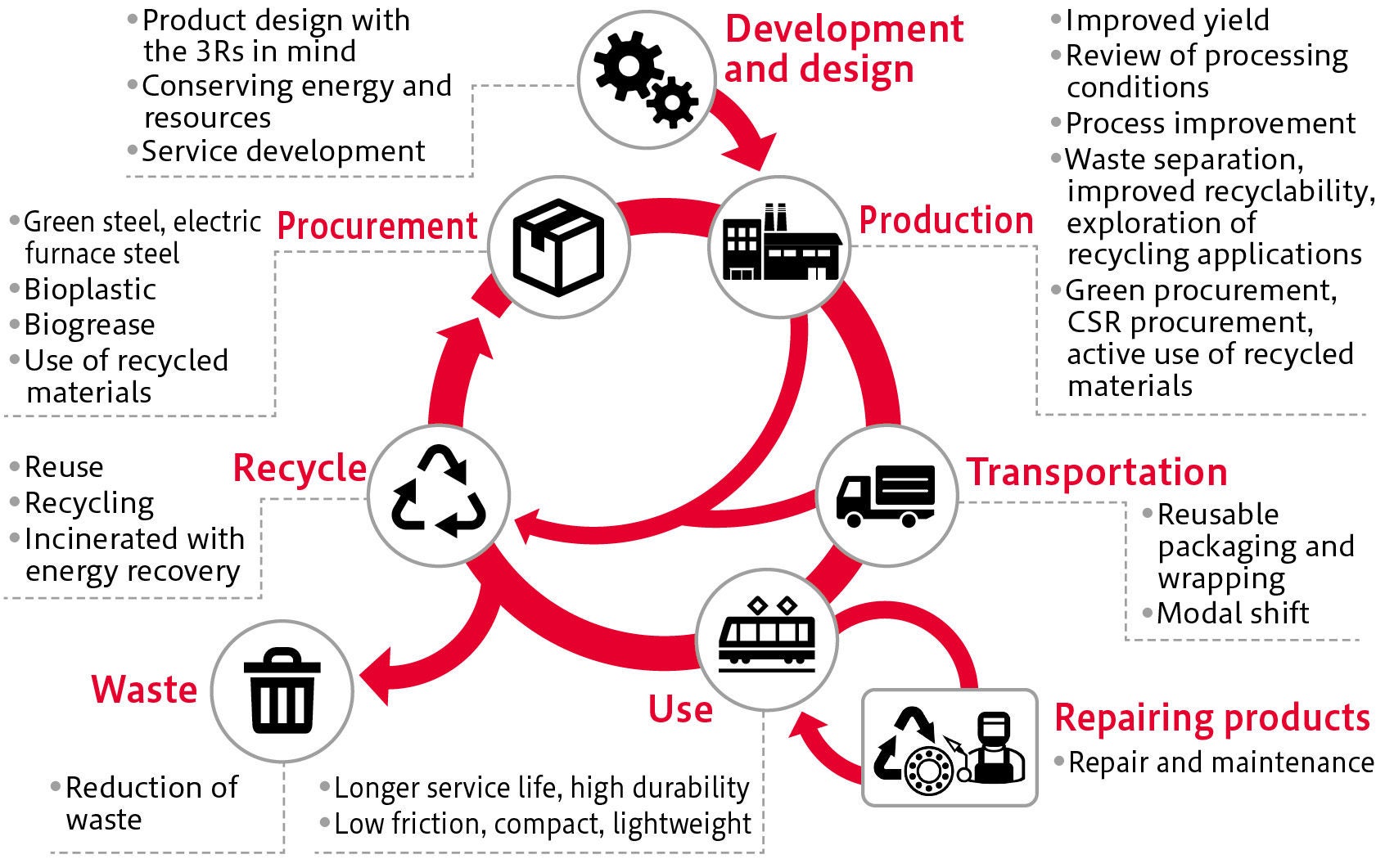
Targets and Performance
◆Mid-Term Management Plan 2026 (MTP2026) Targets, with Targets and Performance for Each Fiscal Year
MTP2026 | FY2023 Targets | FY2023 Performance | Initiatives | FY2024 Targets | |
---|---|---|---|---|---|
Manufacturing, technology, office | Industrial waste per unit of sales: Below -9.0% (base year FY2017) | Below -6.0% (base year FY2017) | -19.8% (base year FY2017) |
| Below -7.0% (base year FY2017) |
Maintain a recycling rate of at least 99% | 99% or higher | 99.2% | 99% or higher | ||
Manufacturing | Waste plastic per unit of sales (Global): Below -3.0% (base year FY2023) | Waste plastic per unit of sales (Japan): Below -1.0%(base year FY2022) | 0.0% (base year FY2022) |
| Below -1.0%(base year FY2023) |
Distribution (Japan) | Packaging waste per production unit: 14% reduction from FY2021 | Below -6.0% (base year FY2021) | -23.3% (base year FY2021) |
| Below -10% (base year FY2021) |
Initiatives
Reduce |
|
---|---|
Reuse |
|
Recycle |
|
Proper Disposal |
|
◆Production Process Initiatives
Pursuing Improvements in Material Yield*1
The majority of NSK’s main products, such as bearings, are made of steel, and approximately half of the CO2 emissions generated during the manufacturing process come from steel production by steel manufacturers. Developing and expanding environmentally friendly manufacturing methods that utilize steel efficiently, without waste, and enable resource conservation is a crucial issue for reducing CO2 emissions throughout the supply chain.
When manufacturing the outer and inner rings of bearings primarily from bar steel through turning*2, the material yield is usually below 50%. However, by revising the manufacturing method, it is possible to improve the yield to above 60%, thereby reducing the amount of steel used (see the chart below). NSK has focused on high-production volume products for these improvements, but it is now working on expanding the range of applicable products and further improving yields. In addition, improving yield reduces the amount of metal scrap generated in the manufacturing process, which in turn decreases CO₂ emissions during recycling into new steel at steel manufacturers. Through the efficient use of resources, NSK is contributing to the realization of carbon neutrality and a circular economy for society as a whole.
Manufacturing Process with Improved Yield
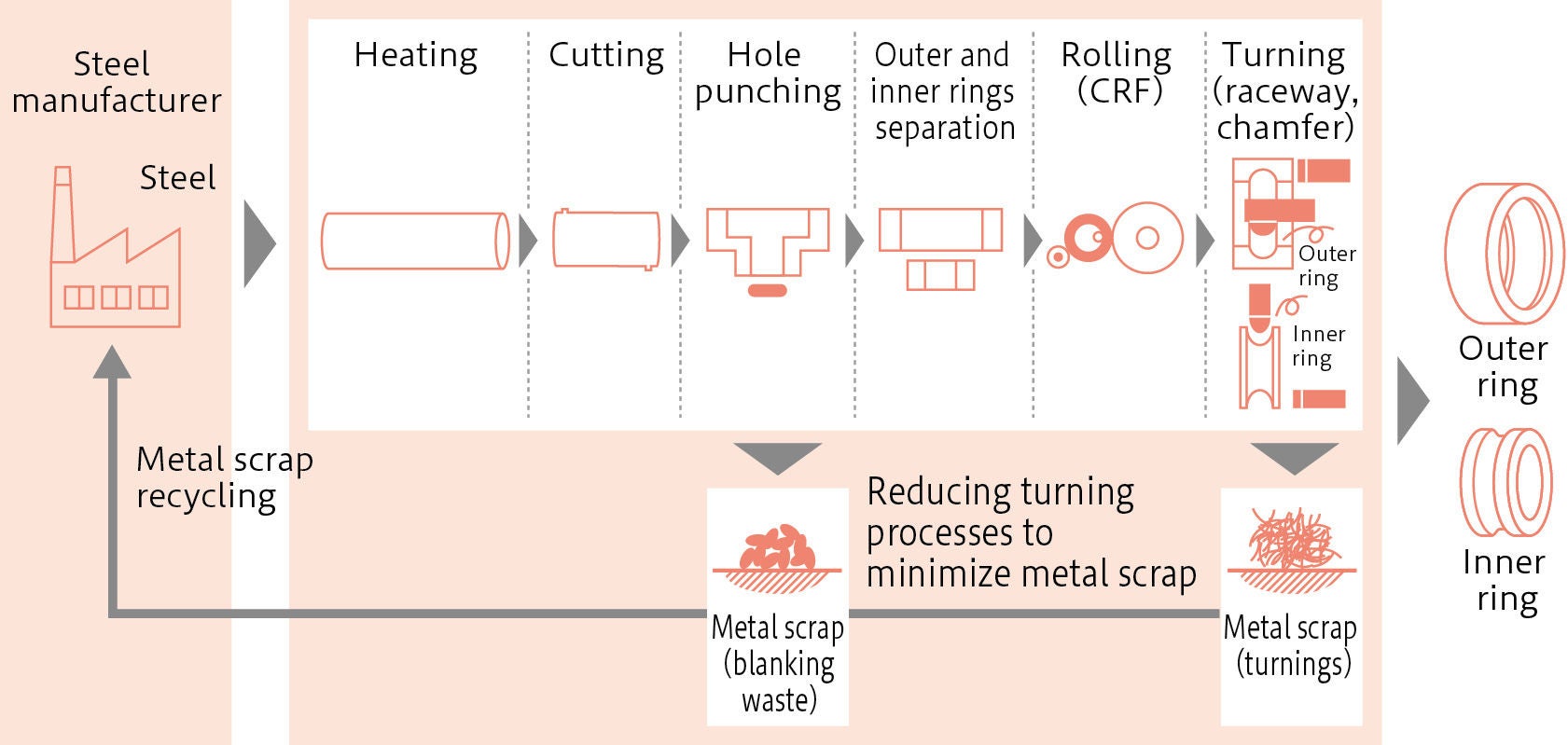
*1 The ratio of the weight of the finished part to the weight of the raw material input into the process.
*2 A machining method in which steel is rotated and shaped by applying a tool called a bit to achieve the desired form.
Reducing Grinding Waste Liquid
About 40% of the NSK Group’s waste is waste liquid generated during the grinding process, and we are taking steps to reduce this waste liquid. As part of these efforts, we are introducing equipment that distills and concentrates waste liquid as well as high-performance concentrators and dryers that quickly dry liquids. Some water recovered during distillation is reused for equipment cooling to effectively utilize resources. The concentrated waste liquid is recycled outside the company as fuel, among other uses.
Shenyang NSK Precision Co., Ltd. has installed a waste liquid evaporator.
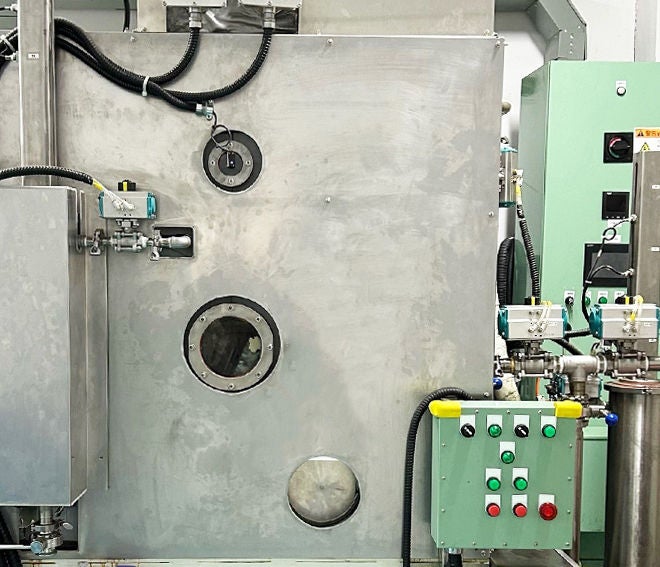
Waste liquid evaporator installed at Shenyang NSK Precision
Reducing Grinding Swarf
We are working hard to reduce the discharge of grinding swarf, which accounts for about 40% of the NSK Group's waste, and to ensure its stable recycling.
To address these issues, we are introducing briquetting equipment at our plants worldwide. This equipment compresses the grinding swarf to reduce moisture and form briquettes, thereby reducing weight and volume and allowing it to be recycled as a raw steelmaking material.
The Peterlee Plant in the UK has introduced briquetting equipment, reducing the discharge of grinding swarf and landfill waste.
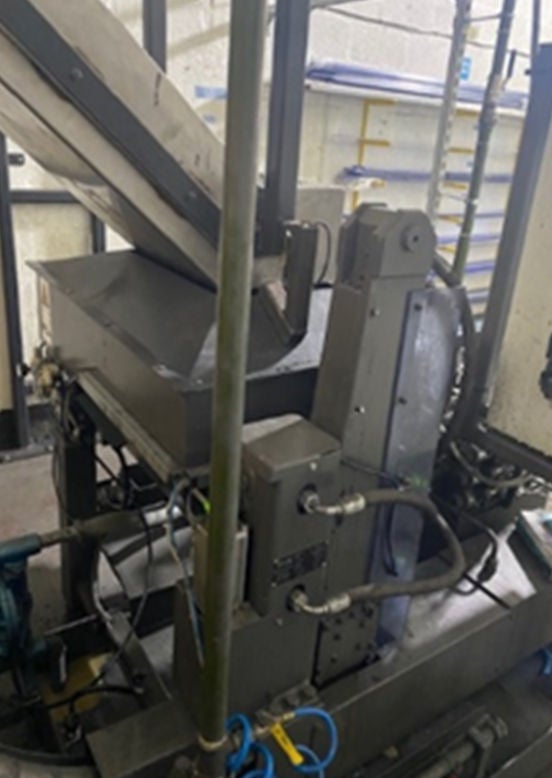
Briquetting equipment installed at the Peterlee Plant
Reducing Sludge
The NSK Group takes measures to reduce the output of sludge.
At Kunshan NSK Co., Ltd. in China, we updated the filter machine, thereby reducing the oil content of diatomaceous earth used in the filter machine and reducing the amount of waste generated. Additionally, at AKS Precision Ball (Hangzhou) Co., Ltd., a sludge dehydrator was installed, reducing the moisture content of the sludge and the amount of waste generated.
Sludge is classified as hazardous waste in China, so these initiatives have reduced hazardous waste.
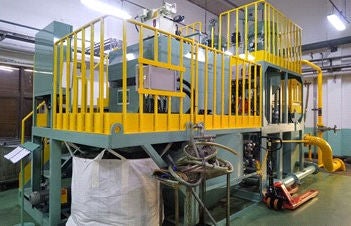
Updated filter machine at Kunshan NSK
Reducing Plastic Waste
The impact of plastic waste on marine ecosystems has become a social issue. Although plastic waste accounts for only about 1% of the NSK Group's waste, we are working to reduce it.
NSK-Warner K.K. has installed a plastic compressor. Stretch film, PP bands, and vinyl are compressed and sold as valuable materials.
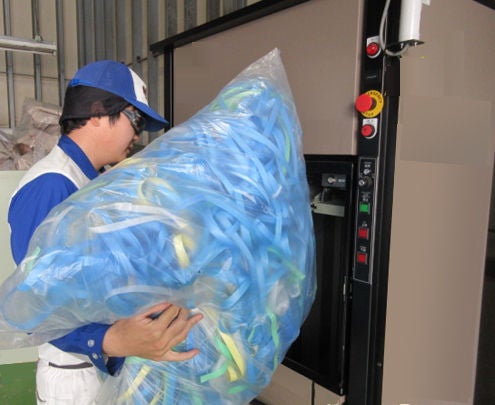
Plastic compressor installed at NSK-Warner
◆Distribution Process Initiatives
Recycling Plastic Containers
In Japan, we are working with a container producer to implement closed-loop recycling, where damaged plastic containers (returnable containers) that have been used repeatedly for many years are recycled as raw materials for new containers. This reduces the amount of virgin plastic resources used and the amount of plastic disposed of as waste.
Closed-Loop Recycling System
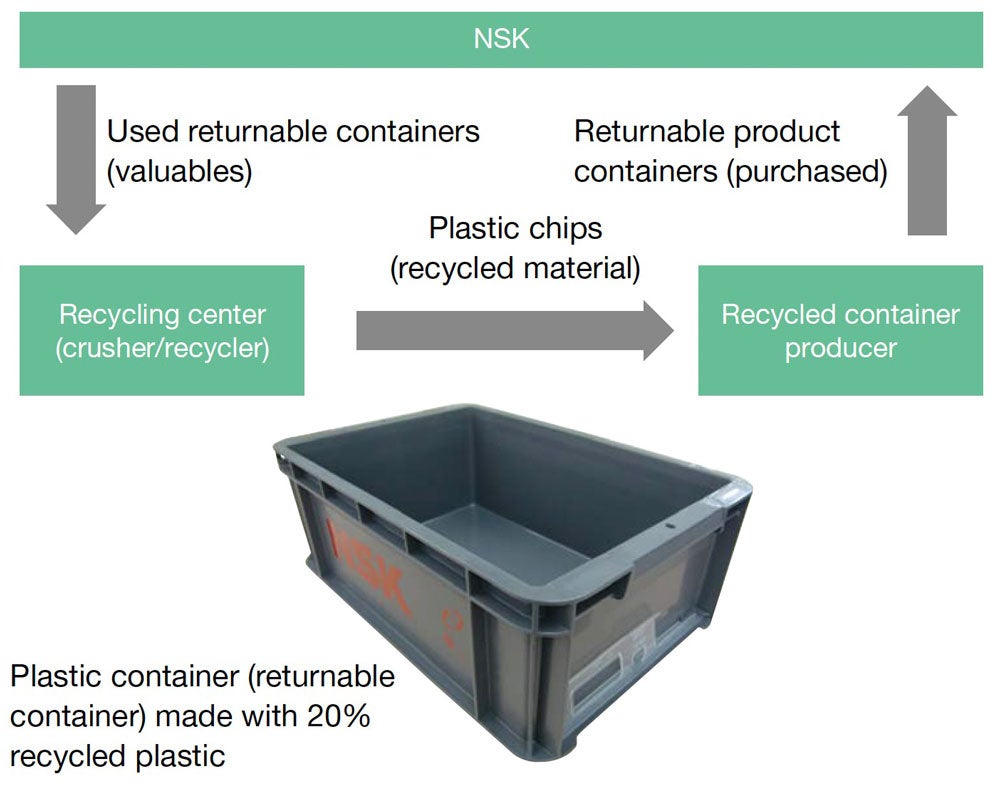
Expanding the Use of Plastic Pallets
The NSK Group is working to switch from wooden logistics pallets for transporting products to customers to plastic pallets.
Switching to plastic pallets allows for longer use with less damage, significantly reducing wood use. An additional advantage is that no splinters break off during use.
Furthermore, plastic pallets are excellent in terms of resource circulation, as pallets that can no longer be used due to damage or aging can be recycled as raw materials for new plastic products.
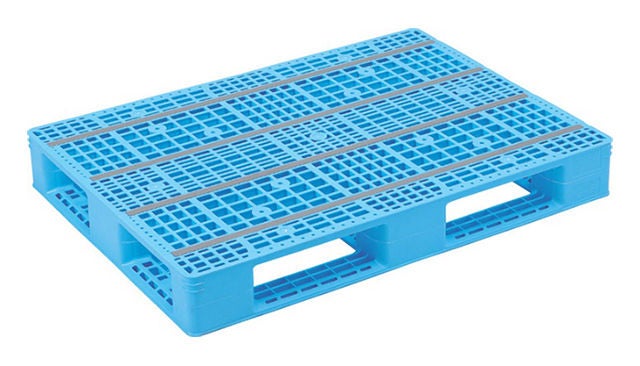
Plastic pallet
Reusing Wooden Pallets
In Europe, the wooden pallets used in shipping from Japan, being of a different size than standard European pallets (“EUR-pallet”), had been unable to be reused and were disposed of as waste. In FY2020, however, the Company commenced returning these wooden pallets to the Japan, Asia, or Oceania regions, and subsequently they are being reused for interregional shipping.
◆Regional Initiatives
In the Americas, packaging materials from unpacking imported products, previously disposed of in landfills as waste, have been sold to contractors since FY2020 for thermal recycling, where the energy generated from incineration is reused.
◆Initiatives in Development and Design
◆Initiatives in Procurement
2. Utilization of Water Resources
NSK’s Approach
An examination of our water needs revealed that the NSK Group is unlikely to be subjected to restrictions on water use, given the locations of our business sites and the volume of water we use. Still, in preparation for future risks, we are working to reduce water consumption by taking measures including cyclical using cooling water, switching to air cooling, and reusing wastewater after purification treatment in our manufacturing divisions. In addition, we are working to conserve water resources by properly treating wastewater and preventing pollution accidents.
Targets and Performance
◆Mid-Term Management Plan 2026 (MTP2026) Targets, with Targets and Performance for Each Fiscal Year
MTP2026 | FY2023 Targets | FY2023 Performance | Initiatives | FY2024 Targets | |
---|---|---|---|---|---|
Manufacturing, technology, office | Water withdrawal per unit of sales: 9% reduction from FY2017 | Below -6% (base year FY2017) | -19.5% (base year FY2017) |
| Below -7% (base year FY2017) |
Initiatives
Reusing Water Resources
PT. AKS Precision Ball Indonesia has built a new waste water treatment facility and has been reusing the treated water. Treated water is used for cleaning floors, watering plants, and filling cooling towers.
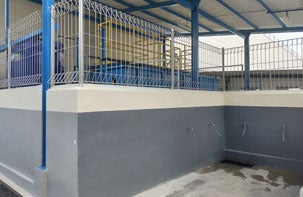
Waste water treatment facility at AKS Precision Ball Indonesia
Harvesting and Using Rainwater
At the Newark Plant in the UK, rainwater is collected and used in facilities such as lavatories. This system provides clean water by filtering and UV irradiating the rainwater to eliminate bacterial microbes and fungal spores, reducing the utility-supplied water used in lavatories and other areas by about 40%.
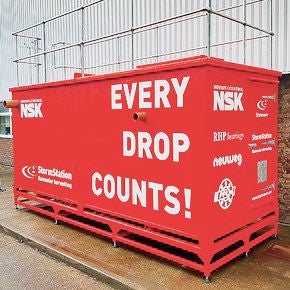
Rainwater collection system installed at the Newark Plant
Switch to Air-Cooled AC Systems
The Saitama Plant upgraded its air-conditioning systems, replacing gas-fired absorption chillers with air-cooled chillers. Not only did the upgrade significantly reduce CO2 emissions, but the switch from absorption air-conditioning equipment, which use water to heat and cool, to air-cooled chillers, which do not, reduced water consumption by approximately 50,000m3 per year (some 20% of the plant’s annual water consumption).
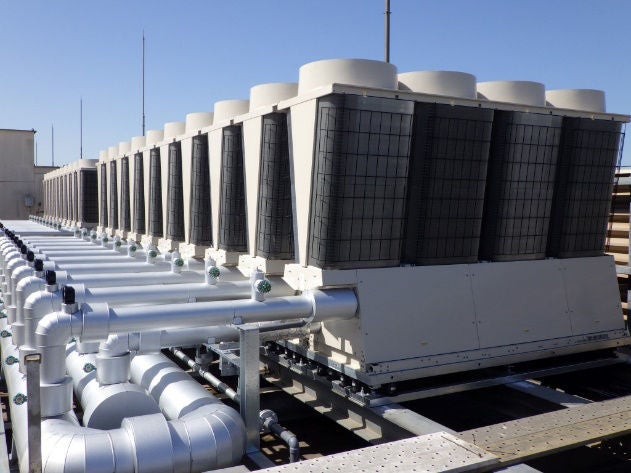
Air-cooled chillers installed at the Saitama Plant
Conducting Water Risk Assessments
Water resources are unevenly distributed across various locals, and the susceptibility to water shortages and water-related disasters varies by country and region. NSK uses the WRI Aqueduct* to assess water risk at all of its production sites around the world. The assessment found that one plant in India is located in an area at high risk of drought, with a water intake of 14,000m3 in FY2023, representing 0.4% of the NSK Group’s total water intake. The plant here is implementing initiatives with a particular focus on water recycling.
* WRI Aqueduct: A global tool for water risk assessment developed by the World Resources Institute (WRI). This tool enables the assessment of water risk with regard to water quantity, water quality, and regulatory and reputational factors in the area where a site is located.