Wälzlager - 21/04/2020
NSK-Wälzlager sparen 10.874 Euro pro Jahr in der Getränkeproduktion
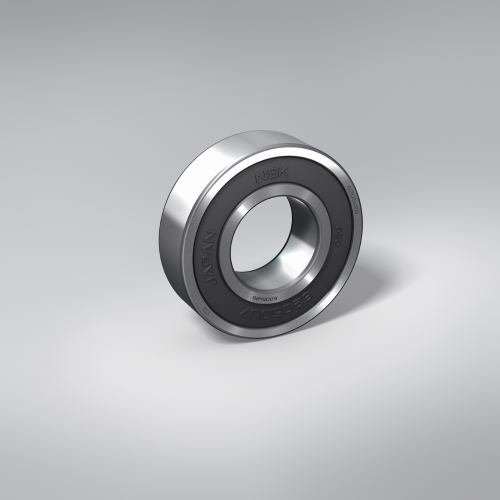
Bei einem führenden britischen Softdrink-Hersteller kam es zu vorzeitigen Lagerausfällen an einer automatischen Flaschenetikettieranlage. Durch den Wechsel auf NSK-Rillenkugellager mit berührungsloser Dichtung und Lebensdauerschmierung erhöhte sich die Lebensdauer der Lager um den Faktor 52. Jährliche Einsparungen von 10.874 € sind die Folge.
Die Betriebsleitung des Getränkeherstellers bat die NSK-Experten, sich vor Ort ein Bild von der Einbausituation der Lager zu machen und Empfehlungen zu geben, die eine Lebensdauerverlängerung der Lager zur Folge haben. Denn innerhalb des Produktionsablaufs kommt der hoch automatisierten Etikettieranlage, die einen flexiblen Kunststoff-Sleeve um die Flaschen legt, große Bedeutung zu. Deshalb mussten die Rillenkugellager wöchentlich gewechselt werden, um ungeplante Ausfälle zu vermeiden.
Der Betreiber der Sleeve-Anlage vermutete, dass die Pulverschicht auf der Innenseite der Sleeves die Ursache zunächst für eine Verunreinigung und in der Folge für die Ausfälle der Lager ist. Die Analyse von NSK ergab jedoch, dass es sich nicht um eine Kontamination handelte. Vielmehr war die Ursache ganz anderer Art.
Nach der Untersuchung von sechs ausgefallenen Wälzlagern im Rahmen des AIP-Programms („Added Value Program“) stellten die NSK-Spezialisten fest, dass Restmagnetismus im Lager Grund für den regelmäßigen Ausfall war. Dieser Magnetismus wirkte wie eine Wirbelstrombremse. Verursacht wurde er durch das Handling des Sleeve: Der Folienschlauch wird geöffnet und über eine Vorrichtung gezogen. Die Lager befinden sich auf einer Führungseinheit, die durch Magnete in Position gehalten wird. Sie ermöglicht den Rollen die korrekte Führung der Kunststofffolie.
Die Identifizierung von Restmagnetismus als Ursache war Ergebnis eines Prozesses, der mit der Demontage und Analyse der ausgefallenen Lager begann. Bei allen Lagern wurde eine stark glänzende Fläche auf dem Außenring des Lagers festgestellt, was auf fehlerhafte Rotation und das Rutschen des Lages in seinem Sitz hindeutet.
Als weiteres Merkmal der ausgefallenen Lager wurde eine leicht raue Laufbahnoberfläche festgestellt, in einigen Bereichen mit Riefenbildung. Dieses Erscheinungsbild ist zwar typisch für Lager mit Metallkäfig, es war aber deutlicher als man erwarten würde.
Abgesehen von diesen Mängeln befanden sich die Lager aber in einem guten Allgemeinzustand. Auf den Oberflächen von Wälzkörpern und Laufflächen gab es nur wenige Anzeichen für das Eindringen von Verunreinigungen oder andere größere Schadensquellen.
Auf den Magnetismus als Ausfallursache kamen die NSK-Experten durch die Analyse der Umgebungsbedingungen. Die Magnete befinden sich in unmittelbarer Nähe zu den Lagern auf der Führungseinheit. Sie bewirkten eine Polarisierung zwischen den Kugeln und dem Käfig auf der einen und den Laufringen auf der anderen Seite. Das erklärt die unruhige Lagerrotation, die der Betreiber bemerkt hatte, und auch das aufgetretene Schadensbild. Hinzu kam, so das Ergebnis der Analyse, ein Mangel an Schmierstoff, der dann zu metallischem Kontakt der Wälzpartner und somit zu zusätzlichem Verschleiß führte.
Der Anlagenbetreiber prüfte daraufhin zunächst, ob es möglich ist, die Magnete in größerer Entfernung von den Lagern anzuordnen. Das erwies sich aber als nicht durchführbar, und er bat NSK um einen Vorschlag die Situation zu verbessern.
Dieser Vorschlag lautete: Einsatz eines berührungslos abgedichteten und lebensdauergeschmierten Rillenkugellagers mit Kunststoffkäfig, welcher den Aufbau von Magnetismus und Polaritäten verringert. Diese Eigenschaften bietet ein NSK-Miniaturrillenkugellager der Baugröße 627 mit einem Kunststoffkäfig aus Polyamidharz (T1X), erhöhter Lagerluft (MC5) und einer beidseitigen Deckscheibe (ZZ) oder kontaktloser Dichtscheibe (VV).
Die Lösung wurde in die Praxis umgesetzt – und führte zu einer beachtlichen Erhöhung der Lagerlebensdauer von einer Woche auf ein Jahr. Das bedeutet eine jährliche Einsparung von 10.874 € an Kosten für Ersatzlager und Montageaufwand.
Bild: Nach dem Tausch der Wälzlager an einer Etikettieranlage spart ein Getränkehersteller nun 10.874 € pro Jahr. Zum Einsatz kommen jetzt NSK-Miniaturrillenkugellager mit Kunststoffkäfig.
Teilen