Bearings - 23/08/2021
NSK Self-Lube® bearing units save steel plant €292,136
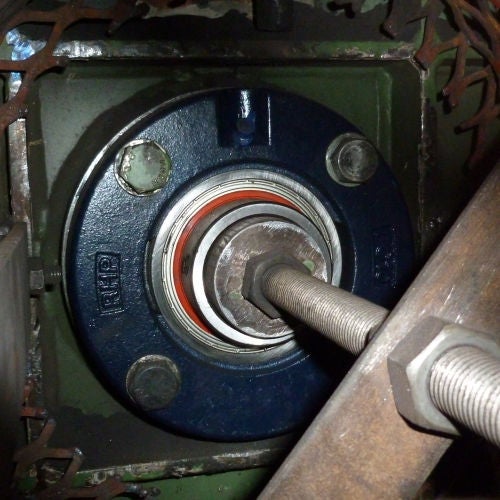
Certain sectors and applications place particularly challenging demands on bearings. Steelmaking is one such example, where the aggressive operating environment means potential bearing failures present a genuine threat to production. Extreme temperatures, particle contamination, shock/heavy loads, water, vibration, high speeds and rapid acceleration/deceleration are just some of the daily hazards that steel plant bearings have to endure. However, the NSK RHP Self-Lube® range of bearing housings and inserts can overcome these issues, as confirmed by a major steel plant.
The international steel plant in question was struggling with up to three bearing failures a year on a rotary coal valve used in its ore preparation process. In addition to the cost of replacement bearings, the failures had knock-on effects in terms of lost production, downtime and damage to associated components. The plant clearly needed a solution to this expensive problem.
NSK duly conducted a full application review, which included a temperature survey and a bearing condition report. The review revealed that the current bearing was inadequate for the high process temperatures, while the lubrication quantities and frequencies were incorrect. As a result, NSK recommended a customised RHP Self-Lube® HLT bearing insert within an RHP Self-Lube® cast iron FC housing, plus a bespoke adaptor plate and a special heat-isolating spacer.
RHP Self-Lube® units include two basic components, the insert and the housing. Each unit consists of a sealed single-row ball bearing with spherical outside diameter and extended inner ring mounted in a high-quality flanged housing made from a rigid one-piece design. Importantly, spherical seating accommodates any initial misalignment when mounting.
Self-Lube® inserts, which feature hardened, high-quality steel for inner and outer rings, also offer optimised internal geometry, a two-piece riveted high-strength steel cage, high-performance grease and durable silicone seals. Notably, the Self-Lube® HLT inserts implemented at the steel plant provide opportunities to reduce maintenance, downtime and replacement costs when operating at temperatures up to 180°C.
The units are available with various locking methods for close-fit shaft mounting. This feature, combined with a complete range of sealing solutions for all environments, makes NSK RHP Self-Lube® a very versatile product. As the name suggests, re-lubrication capability is standard.
For the rotary valve bearings at the steel plant, the expert team of NSK engineers also recommended changes to the lubrication quantities and frequencies. To ensure correct application, NSK oversaw the fitting of the new bearings as part of a trial.
After more than 12 months the bearings still had not failed, delivering a total annual cost saving for the customer of €292,136. This calculation includes cost savings associated with: the elimination of downtime due to bearing failures; fewer bearing purchase orders; reduced bearing replacement time; and the removal of compressed air cooling to help control the overheating of previous bearings.
For further information about NSK RHP Self-Lube® bearing units: www.nsk.com/eu-en/products/bearing-units/self-lube-units
Picture 1): The steel plant was struggling with up to three bearing failures a year on a rotary coal valve used in its ore preparation process
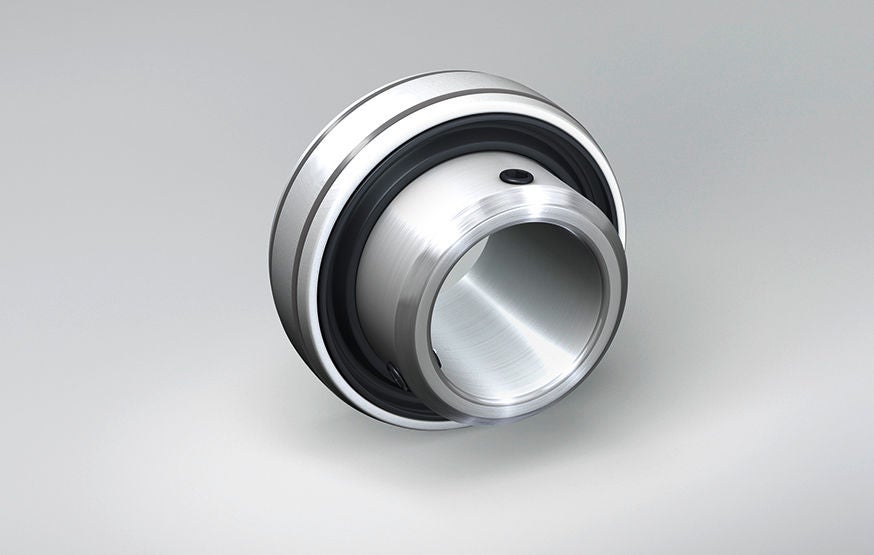
Picture 2): NSK RHP Self-Lube® HLT inserts help to reduce maintenance, downtime and replacement costs when operating at temperatures up to 180°C
Share