Linear Motion Control - 21/11/2022
New NSK ball screw for next-generation, high-accuracy machine tools
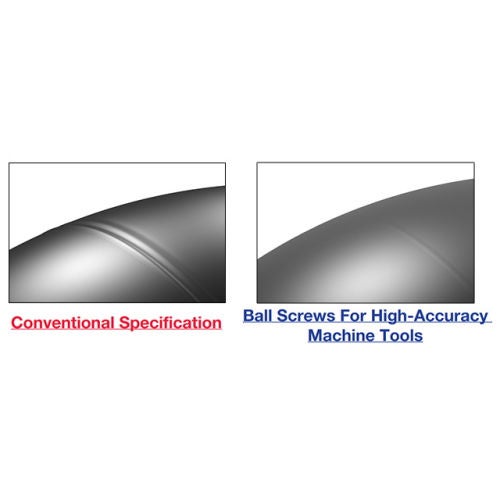
NSK has developed a new type of ball screw that exhibits reduced motion errors to deliver higher surface finish quality for machine tools used in mould and die machining and other surface-critical applications. By eliminating or reducing the time needed for secondary burnishing or polishing applications, the new ball screw also contributes to higher productivity, while simultaneously reducing the amount of drive torque to save energy.
In recent years, builders of machine tools such as five-axis milling machines have been demanding increased accuracy to produce higher quality mould and die surfaces, where the ball screws used in these machines must further improve motion accuracy.
When a ball screw reverses direction, sudden fluctuations in friction cause ‘quadrant glitch’ motion errors with two peaks, leaving streak marks on the machined surface and reducing surface quality. Numerous studies conducted on quadrant glitches show that it is possible to correct the first peak through numerical control (software-based servo controller compensation). Although it is more difficult to fully compensate for the second peak due to the combined effects of more factors (compared with the first peak), NSK can now present the machining industry with a solution to this problem.
Using real digital-twin simulation and friction analysis, NSK has developed a new ball screw with an optimised internal design. Key to this outcome was the company’s understanding of the underlying mechanism of friction fluctuations in ball screws.
Among its many features, the new ball screw stabilises drive torque and reduces friction fluctuations when reversing its direction of motion, thereby improving motion accuracy and reducing quadrant glitch motion errors. The result is a near elimination of the second peak. Indeed, up to 20% less friction fluctuations also contributes to reducing the height of the first peak.
Through a combination of NSK's new ball screw and software servo controller compensation, machine tool manufacturers can assure their customers of significant improvements in machined surface quality. Furthermore, the enhanced surface quality eliminates or reduces the need for any previously required burnishing or polishing processes, reducing lead times, while lower drive torque contributes to energy savings. All of these benefits provide machine tool builders with the opportunity to pitch unique selling points to potential customers.
To maximise convenience for machine tool manufacturers, the mountings of NSK ball screws with quadrant glitch control are fully interchangeable with those of conventional products, allowing adoption without costly equipment changes. The ball screw will be available in shaft diameters from 25 to 63mm, with leads from 5 to 30mm. Preload types will include: offset preload (Z preload), double nut preload (D preload) and spring-type double nut preload (J preload).
Picture 1): Enlarged view of machined surface (simulated image)
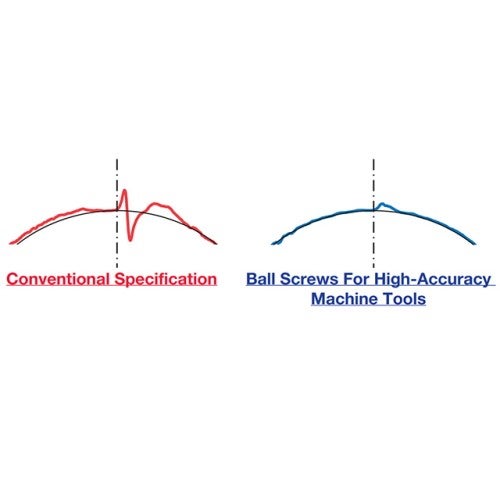
Picture 2): Motion error during circular interpolation machining (with servo controller compensation)
Share