Bearings - 05/09/2022
New NSK bearings deliver long service life for steelmakers
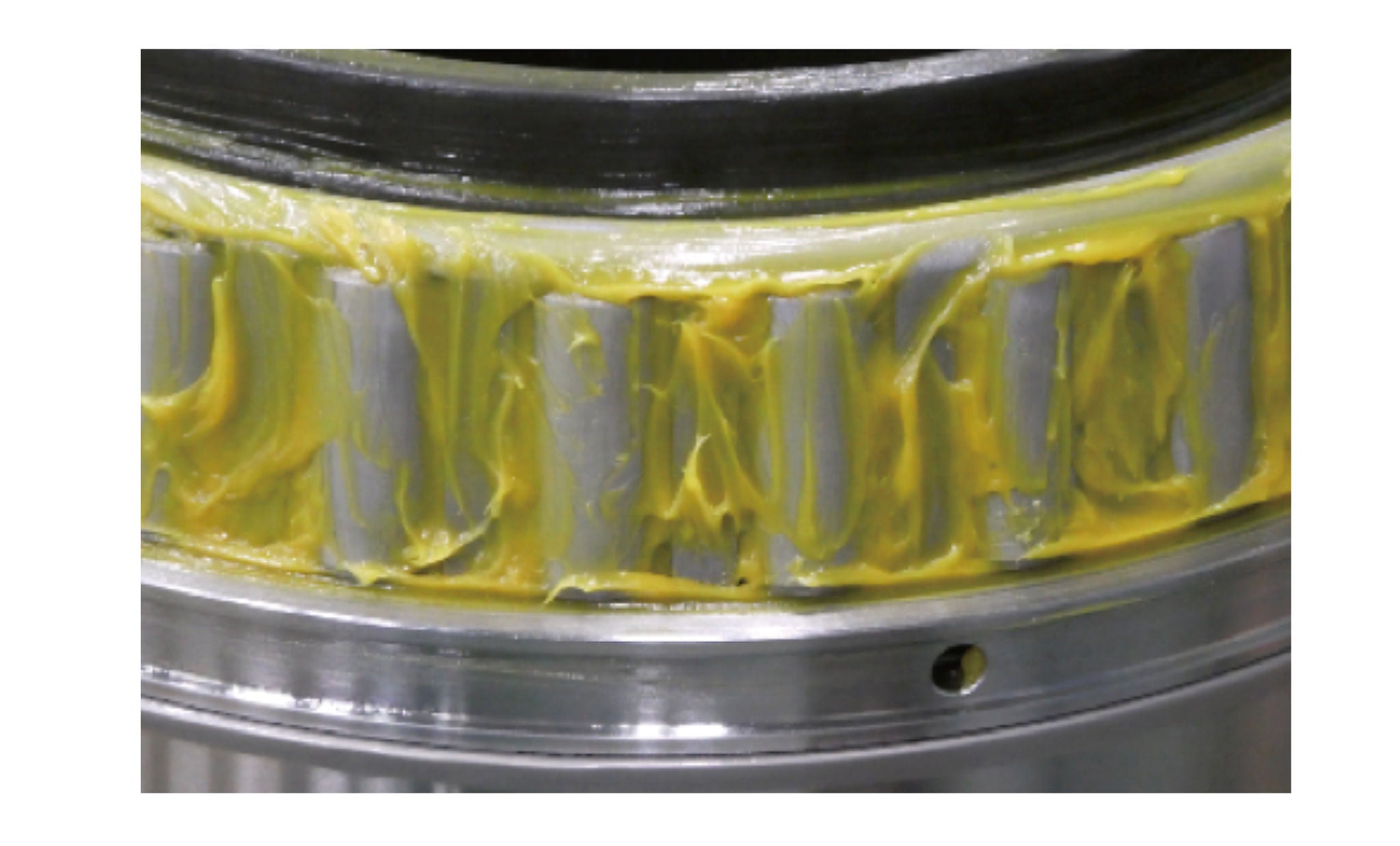
Due to harsh environmental conditions, steelmaking equipment requires highly reliable, long-life bearings that resist premature damage. NSK has therefore developed a new high-value-added bearing for the steelmaking industry that improves productivity through stable equipment operation and reduces maintenance costs with its innovative sealing and lubrication technologies.
As part of the manufacturing process from crude iron to finished product, steelmaking relies on several different types of equipment, including: equipment that melts raw pig iron to make molten steel; equipment that adjusts the composition of molten steel and hardens it; and rolling equipment that forms hardened steel into plates or bars. Among these processes, bearings for rolling mills have to withstand particularly harsh operating conditions.
In addition to accommodating extreme loads and speeds, bearings for the work rolls of rolling mills must also resist infiltration by oxide scale and cooling water. Premature damage to poorly specified bearings will result from the flaking or rusting of raceway surfaces, largely because of poor lubrication. However, over-lubricating is not the answer due to cost and environmental concerns.
With these thoughts in mind, NSK set about developing a solution which utilises sealing technology optimised for rolling mill bearings, alongside grease technology that minimises the effects of water intrusion. The outcome is a long-life, four-row tapered roller bearing that is more water-resistant than conventional bearings and delivers optimal performance in steelmaking equipment applications.
Notably, the oil seal on the new bearing is extremely compact, while a new processing method for the cage has increased roller length and diameter, and increased the number of rollers, resulting in a high load capacity design.
Optimising the internal design of the new bearing increases the basic dynamic load rating by up to 25% compared with NSK’s conventional product. Furthermore, tight sealing not only suppresses the ingress of particulates and water to extend service life, it also reduces the need for grease replenishment during maintenance periods.
By optimising the grease composition it is possible to form and maintain a thick oil film between the bearing raceway surface and the rollers to avoid metal-to-metal contact. Moreover, the use of a special additive prevents water from contacting the raceway surface, inhibiting subsequent corrosion. NSK tests in a water-infiltrated environment confirmed that the new grease has a service life more than twice that of conventional lubricating grease, helping to avert premature damage.
Available in sizes from 345 to 615.95 mm outer diameter, NSK’s new sealed-clean, four-row tapered roller bearings with water-resistant grease are suitable for work rolls in hot/cold rolling mills and other steelmaking equipment. Moving forward, the company will continue its development programme in support of steelmakers, creating products that contribute to both process advancement and environmental preservation.
Picture: 1) The optimised grease forms a thick oil film between the bearing raceway surface and the rollers to prevent metal-to-metal contact
Share