Bearings - 13/02/2023
Pre-assembled NSK bearings save time and money at vibrating screen manufacturer
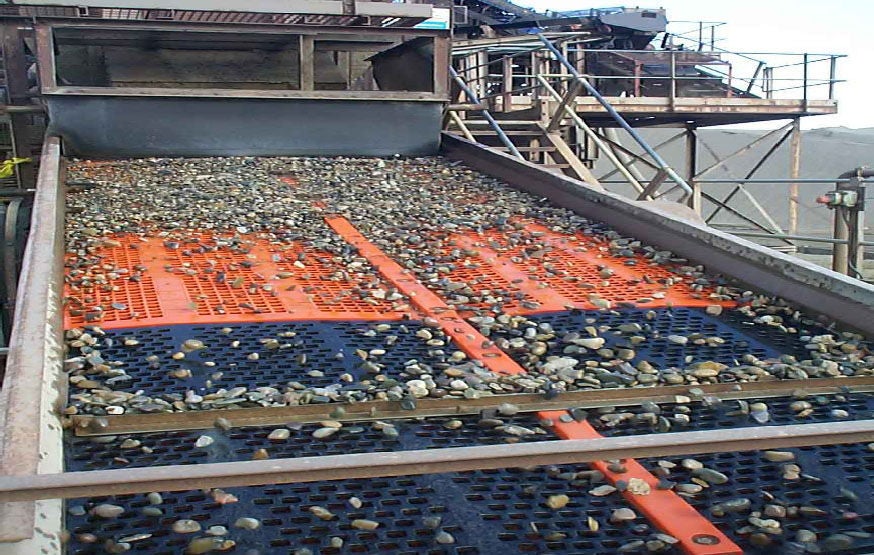
By switching to NSK pre-assembled, fully integrated bearings, a vibrating screen manufacturer is witnessing annual cost savings of €117,000. The company was previously experiencing difficulties with the consistency of the bearing mounting in its shaker box assembly. At the same time, the plant was looking for opportunities to save manufacturing costs and improve the overall performance of its screens. NSK addressed all these issues following a comprehensive design review of the original machine.
To overcome the challenges at the manufacturing plant, which produces vibrating screens for the quarry and mining sector, the company engaged the services of bearing specialist NSK. Expert engineers proposed the design and manufacture of a complete bearing assembly, such that the resultant unit could simply fasten to the machine frame without any complex assembly of housings, bearings, or seals.
Part of a value proposal, NSK first created a bespoke design with full CAD drawings for approval by the customer. Once signed-off, NSK took over the complete housing, seals and bearing assembly operation. The product could then be supplied as a built unit; packed, pre-greased and ready to fit with bearing location features.
Not only were bearing performance and reliability improved in the severe operating environments that vibrating-screen bearings endure, but the customer also witnessed a significant reduction in manufacturing costs thanks to the much-reduced need for complex fitting.
NSK’s design focuses on a bespoke housing made from high-strength SG (spheroidal graphite) iron in combination with NSK’s CAM-VS vibratory specification bearings. The integrated assembly, which reduces the need for the customer to manufacture sub-components, includes labyrinth and contact seals.
Further benefits of the solution include greater fatigue strength against vibration, shock loads, wear, and corrosion, along with a reduction in noise levels of 50-60%. End users can also re-grease the integrated bearing unit whenever required.
Ease of installation has reduced in-house costs at the vibratory screen manufacturing plant. Previously, the company would incur high annual expenditure for manufacturing the housings in-house, together with bearing purchases and assembly costs. In contrast, the plant now only has a single, much reduced cost of the pre-assembled bearing units from NSK, delivering annual savings of €117,000.
Picture 1): NSK improved bearing performance and reliability in the severe operating environments that vibrating-screen bearings endure
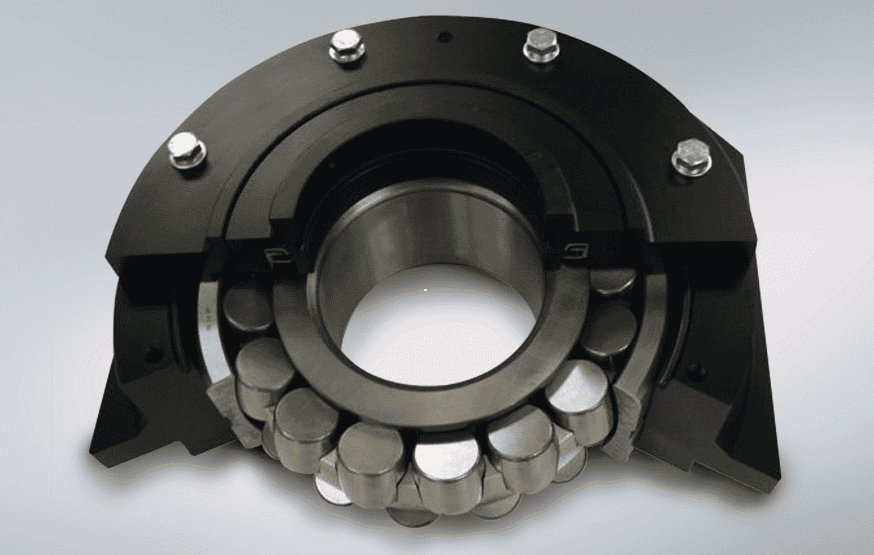
Picture 2): A cut-away of NSK’s pre-assembled, integrated bearing assembly
Share