Bearings - 05/12/2022
Preventing electrical erosion of bearings in EV drivetrains
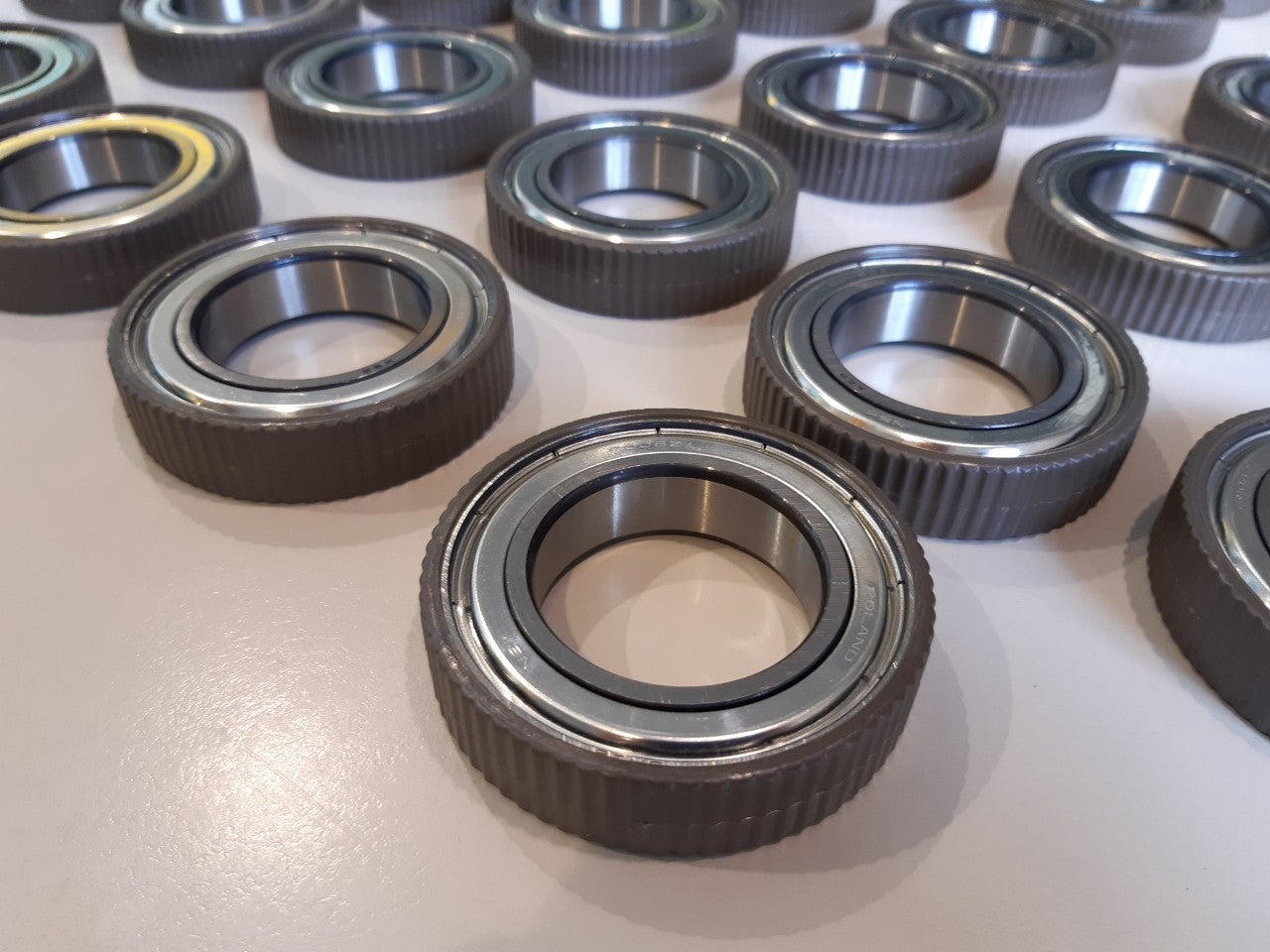
NSK currently developing a new and cost-effective way of preventing electrical erosion in the drivetrains of electric vehicles (EVs). Based on a unique method of producing a patented plastic over-moulding for deep groove ball bearings, EV manufacturers will make significant savings in comparison with expensive ‘hybrid’ bearings that feature insulating components made from ceramics.
Parasitic current can take many paths through an EV motor due to circumstances such as the presence of an inverter that switches frequently across multiple phases. Specific types of electric motor architecture can also cause a variety of bearing current flows, including rotor ground bearing currents, circulating bearing currents and EDM (electrical discharge machining) currents.
EDM currents, in particular, present a severe risk to bearings, largely due to arcing that occurs at specific voltages. This arcing (load charging) leads to uncontrolled discharging at fairly high ampere values, essentially changing the morphology of the steel bearing rings and balls. Here, material melts and re-solidifies on the metal surface so that ripples several microns deep begin to appear on the bearing raceways of both the inner and outer ring. Excessive noise is often the first indicator of this issue. For EVs, which are becoming more silent with ongoing development, noise is highly undesirable.
NSK decided it was time to set about developing a solution to this long-standing problem, firstly by assessing the conditions that promote electrical erosion, including: operating conditions such as load, rotational speed, temperature and lubricant viscosity; the condition of the resulting lubrication (hydrodynamic, mixed, boundary); and electrical properties like resistance (material and capacitive).
Established methods to help prevent electrical erosion essentially comprise either insulation or conduction. If the charges are not too high, it might be sufficient to employ a conductive grease, or well-dimensioned grounding elements. However, for specific bearing positions, such as the drive-end bearing prior to the gearbox, insulation is required in the form of either ceramic or plastic bearing components. For instance, NSK can use ceramic as a coating on the outer/inner rings, or can manufacture the entire roller elements and balls from ceramic. Although these ‘hybrid’ bearings provide an optimal countermeasure to electrical erosion, they are also expensive.
The requirement for a more cost-effective solution is pressing because the high-voltage architecture of EVs is about to change from the 400V systems that are dominant today, to 800V. The latter will potentially command 50% of the market as soon as 2030, which will simply double the issue and require even better protection measures for bearings.
NSK is therefore proposing the use of a plastic over-moulding made from a high-performance a PPS (polyphenylene sulphide) polymer that offers high resistance against heat and a large variety of chemicals, as well as stable electrical and mechanical performance (even at temperatures up to 150°C). In addition, the material provides a low level of water absorption, unlike many other polymer types, ensuring dimensional stability.
Comprehensive NSK tests reveal the performance of the over-moulded bearings in comparison with the company’s standard bearings. For example, at 24V voltage and 15kHz frequency, standard bearings showed clear electrical erosion of the inner and outer rings. In contrast, the new NSK over-moulded bearings demonstrated no evidence of this phenomenon. The same outcome resulted at various rotational speeds.
Production of the over-moulding comes courtesy of an innovative injection moulding process located at an NSK facility in Europe to optimise supply to the EV industry. Special mould features ensure homogenous distribution and orientation of the molecules and glass fibres to optimise mechanical performance. Notably, the precision of the over-moulding means there is no requirement for grinding, leaving a ‘structured’ finish in place. As a result there is not 100% contact between the housing and the outside diameter of the bearing, creating gaps filled with air. Air is a good isolator and costs nothing. This innovation provides market differentiation for the NSK solution. As a further benefit, the structured finish overcomes the established issue of bearing creep within housings, as it potentially provides a better fit due to multiple contact points (depending on the use case).
Applicable on the inner and outer ring, the patented insulation layer will usually range from 0.7 to 1.2mm in thickness. To accommodate the extra material NSK can offer space-neutral solutions. This is easiest when starting a new bearing design, although NSK can also machine material from the outer diameter of existing bearings accordingly. However, there is a cost element to this solution. As an alternative proposal, OEMs can look to open up the housing that accommodates the bearing, which means NSK will not have to change its process. Taking this pathway allows EV manufacturers to take full advantage of the significant cost savings available in comparison with hybrid bearings.
At last, the EV industry has a cost-effective solution that negates the electrical erosion of bearings in electrified drivetrains. The over-moulding is currently applicable to NSK’s 6008 and soon for its 6206 deep groove ball bearing series (sealed and non-sealed), which are ideal for EV applications.
As a final note, NSK has a modular test mould available that covers outer diameters from 55-95mm (up to 30mm width). The company is therefore ready to undertake tests on behalf of customers with requirements in this range.
Picture 1): Applicable on the inner and outer ring, the patented insulation layer thickness ranges from 0.7 to 1.2mm.
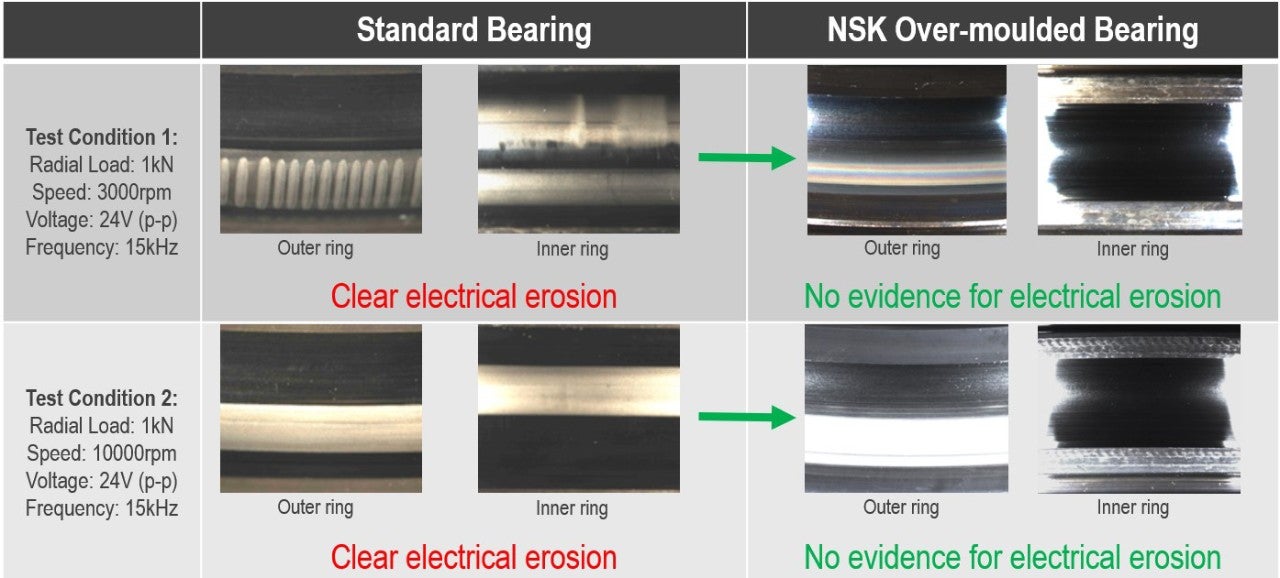
Picture 2): NSK tests reveal the success of the over-moulded bearing innovation against standard NSK bearings
Share