Machine Tools
NSK is the only manufacturer to offer a complete development and supply service for the essential parts found in machine tools.
In an industry where customers are demanding faster times-to-market and ever more customisation, you can be sure that NSK has both the experience and the expertise needed to support you.
From our Super Precision Bearings to our market-leading linear components, our high-quality components offer the reliability, efficiency and productivity the industry needs.
Time-to-Market in the Machine Tool Industry
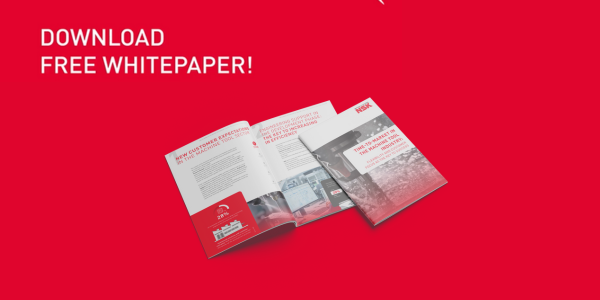
Read our latest whitepaper to learn more about the latest trends and developments driving the machine tools sector.
Written by leading NSK experts, the document outlines how we can help your company stay ahead of the curve and meet the demands of end-users.
We also recommend you check out our brochures, catalogues and technical guides, which explore every aspect of what NSK has to offer.
Products
NSK offers a wide range of high-quality products specifically developed for the machine tools market. Whether it’s our bearings, our ball screws or our linear guides, our components offer peace of mind to customers all over the globe.
Bearings & Linear
NSK offers unrivalled quality in the machine tools sector. In particular our Super Precision Bearings, manufactured in England and Japan, are market leading components.
Thanks to non-stop R&D and our use of cutting-edge technologies, our ball screws are the leading brand worldwide. They’re the component of choice for manufacturers across the globe.
Learning Module: Precision Bearings for Machine Tools
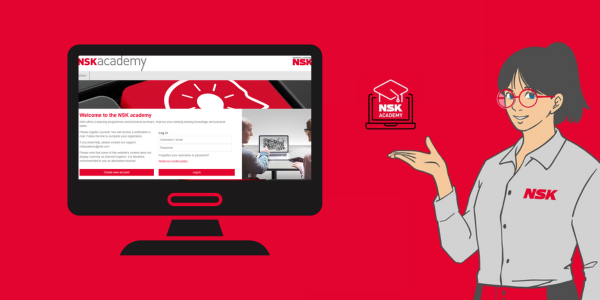
The NSK Academy is the best place to develop your understanding of the role bearings play in the Machine Tools sector.
Whether you’re new to the industry, or an experienced professional looking to refresh your knowledge and learn about something specific, our online tools and tutorials have got you covered.
Register for our Newsletter
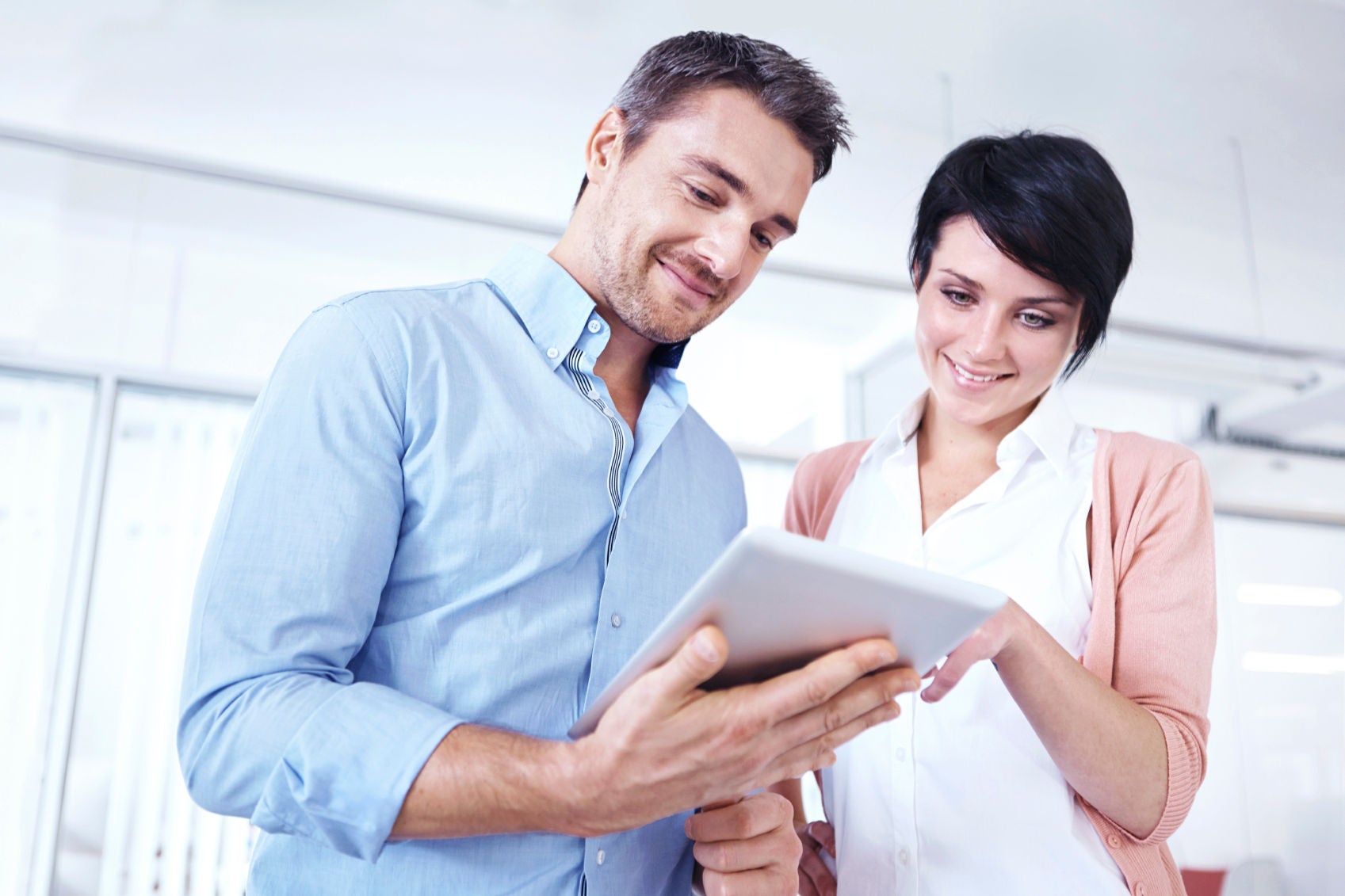
We would like to keep you informed about topics that are relevant to you: the latest news, interesting facts about our product lines, new catalogues and upcoming events.
Please fill in the form below.
Share