Success Story
Industry: Steel & Metals
Application: Coiler Gearbox
Cost Savings: € 17 450
Introduction
A manufacturer of Industrial Gearboxes was commissioning a reducer gearbox in collaboration with NSK for a cold roll steel mill application. The gearbox featured NSK Spherical Roller bearings which gave the advantage of high load carrying capacity for the output shaft. During the agreed running trail, the engineers had to review performance of the bearings. Normally the gearbox would have to be stripped and the components examined. This would have been very costly and caused a significant delay to the project. However as part of the design support process, NSK performed Condition Monitoring on the running gearbox. This demonstrated that all components were in optimum condition with no need for further investigation allowing the gearbox to be released and delivered on time.

- Cold Rolling Mill
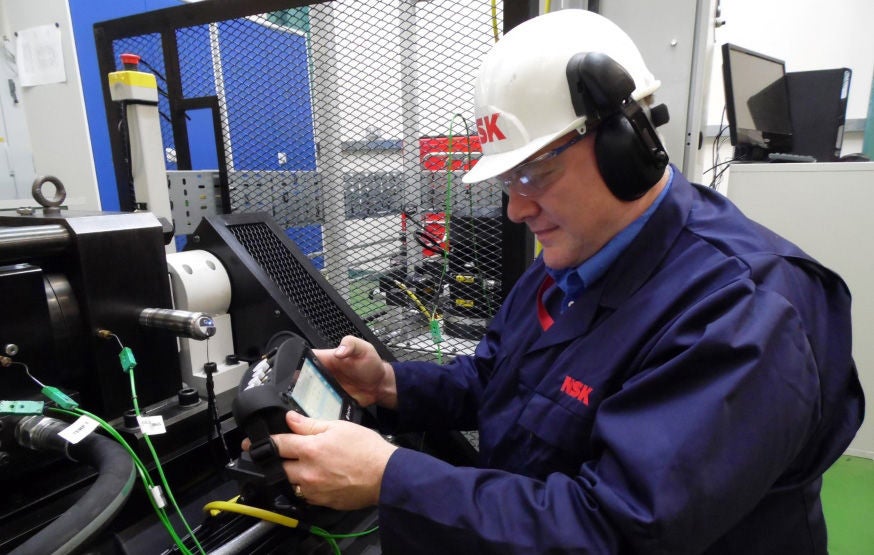
- Condition Monitoring Service (CMS)
Key Facts
- Coiler Gearbox
- Commissioning tests of new bearing set up
- Unexplained noise during testing
- NSK Solution: Condition Monitoring Service (CMS) with detailed analysis to identify bearings and associated components health. NSK performed a full vibration analysis of the running gearbox
- The results showed that the bearings were in optimum condition and no issues were identified
- This allowed the manufacturer to pass the commissioning trials
- Significant costs were saved because further investigation and disassembly of the gearbox were not necessary
Value Proposals
- An NSK expert performed an AIP Survey on the gearbox
- The NSK engineer conducted a Condition Monitoring review including all technical data, measurement conditions and explanations of spectrum analysis
- At the fixed trial running speed, the resonance of the machine was reached and some noise appeared
- No issue was detected on the bearings and there was no risk due to the noise on the final application resulting from the variable speed on the coiler gearbox
Product Features
Live assessment of a machine's condition and health while the machine is still in operation.
Predicted life of the critical components inside a machine allowing you to plan maintenance more accurately.
On-site support from NSK Engineers. Not only are our engineering experts fully trained in the use of condition monitoring, they are also experienced bearing experts and can take diagnostics to the ultimate level of root cause. This allows them to also recommend improved bearing and linear motion solutions.
Assurance that NSK as a full range supplier can help with the provision of critical bearing and linear motion spares.
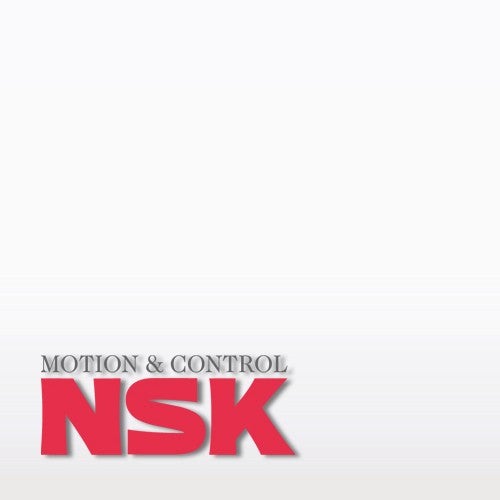
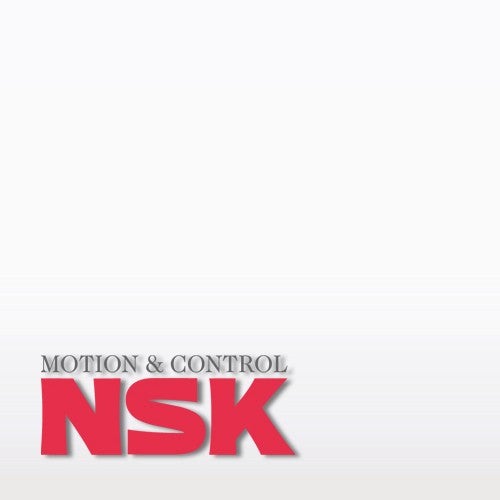
Cost Saving Breakdown
Before | Cost p.a. | NSK Solution | Cost p.a. | |
---|---|---|---|---|
Bearing Costs: Cost of bearings | € 1.750 | Bearing Costs: No further bearing needed | € 0 | |
Engineering Costs: Remove the bearings from coiler gearbox and install new bearings | € 2.500 | Engineering Costs: Replacement not necessary | € 0 | |
Costs of lost production: Late delivery costs commissioning | € 13.200 | Costs of lost production: No late delivery penalty | € 0 | |
Total Costs | € 17 450 | € 0 |
Reference:SS-E-3007
Share