Success Story
Industry: Food & Beverage
Application: Extrusion blow molding machine
Cost Savings: € 59 549
Introduction
A British producer of plastic bottles experienced failures of linear guides on extrusion blow molding machines. NSK examined some failed guides concluding that the failures were due to damaged end caps, caused by a combination of short stroke length, repeated start stop operation and increased friction force start up. NSK recommended the trial of NSK roller guides which have optimised internal design to reduce start up torque, resulting in less force on the end caps. The new design was fitted to one machine with no failures reported for over a year. This has eliminated production down time giving a significant saving on maintenance and lost production costs.
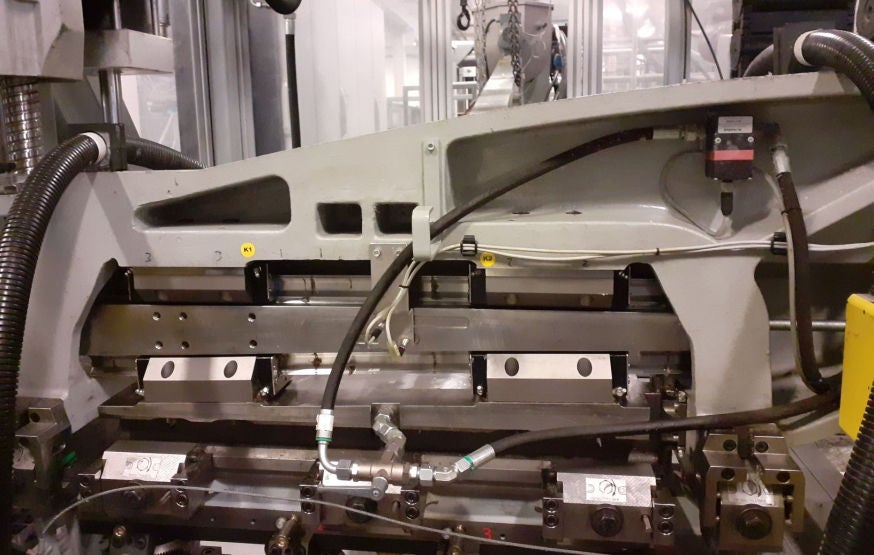
- Extrusion Blow Molding Machine

- RA Roller Guides
Key Facts
- Plastic bottle manufacturing
- Frequent bearing failure across a number of machines
- Linear roller guides failing due to damage to recirculation end caps
- NSK recommend linear guides RA Series that have spacer joints between rollers
- Reduced start up friction force
- Failures on trial machine eliminated
- Significant reduction in maintenance and lost production costs
Value Proposals
- Plastic bottle manufacturing
- Frequent bearing failure across a number of machines
- Linear roller guides failing due to damage to recirculation end caps
- NSK recommend linear guides RA Series that have spacer joints between rollers
- Reduced start up friction force
- Failures on trial machine eliminated
- Significant reduction in maintenance and lost production costs
Product Features
- Plastic bottle manufacturing
- Frequent bearing failure across a number of machines
- Linear roller guides failing due to damage to recirculation end caps
- NSK recommend linear guides RA Series that have spacer joints between rollers
- Reduced start up friction force
- Failures on trial machine eliminated
- Significant reduction in maintenance and lost production costs
Cost Saving Breakdown
Before | Cost p.a. | NSK Solution | Cost p.a. | |
---|---|---|---|---|
Bearing Costs | € 7 400 | Bearing Costs | € 5 781 | |
Engineering Costs | € 4 047 | Engineering Costs | € 1 619 | |
Costs of lost production | € 55 502 | Costs of lost production | € 0 | |
Total Costs | € 66 949 | € 7 400 |
Reference:SS-E-2-782
Share