Success Story
Industry: Machine Tools
Application: Horizontal Machining Centre
Cost Savings: € 24 096
Introduction
A specialised metals machining company were experiencing continuous performance problems with their horizontal machining centre. Bearings were prematurely failing causing unplanned down time and significant production problems. NSK performed a detailed analysis of the machine spindle, including a failed bearing investigation and grease condition review, and found that both cutting fluid and machining debris were entering the bearings. This caused the lubricant to fail and resulted in premature bearing failure. NSK proposed a Sealed Super Precision Bearing with a higher contact angle to improve the bearing arrangement due to high axial load and counteract the debris. Lifetime was increased from 15 days to 6 months.
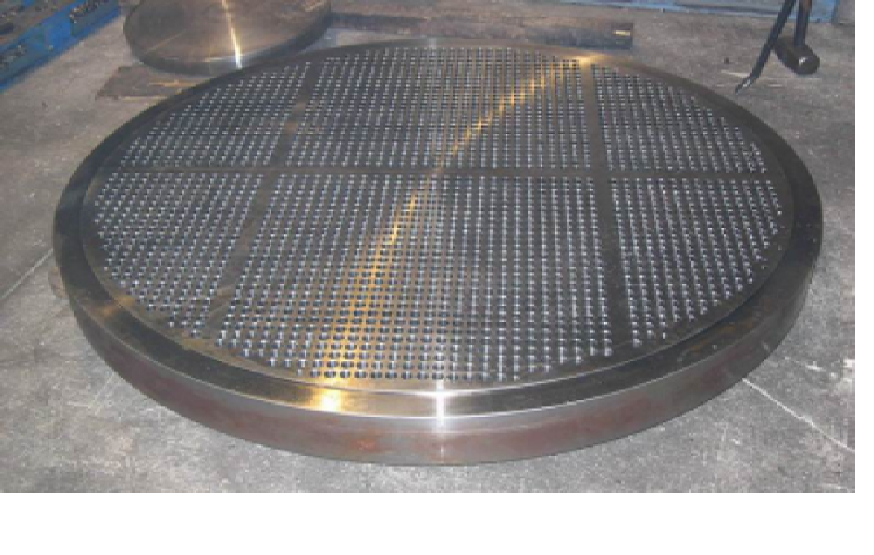
- Heat Exchanger End Plate
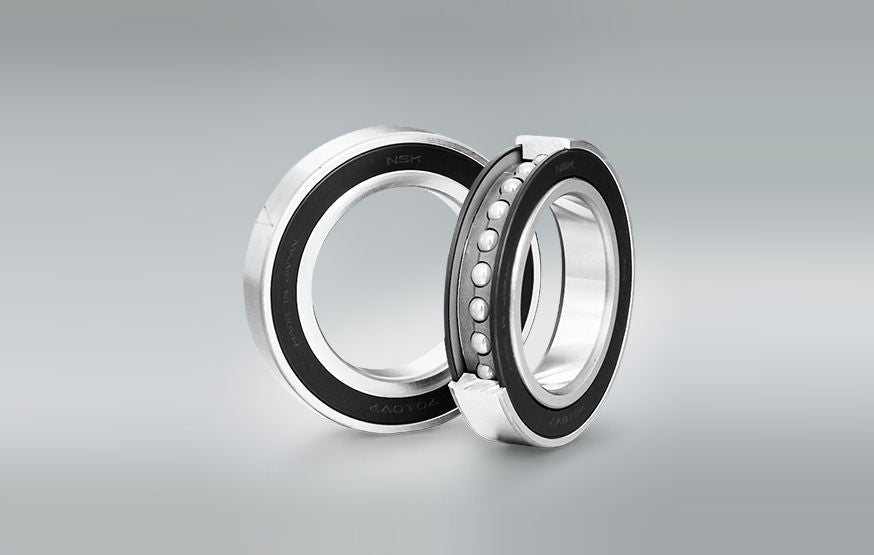
- Sealed Super Precision Bearing
Key Facts
- High axial loading
- Machining Centre Performance Issues
- Debris and cutting fluid contamination
- Grease condition and Bearing Failure Analysis highlighted root the root cause of failures
- NSK Sealed Super Precision Bearings proposed
- Increased contact angle for axial load capacity
- Lifetime improvement from 15 days to 6 months
Value Proposals
- Bearing Failure Analysis and grease condition checks showed that cutting fluid and debris were causing bearing failure
- NSK recommended the use of Sealed Super Precision Angular Contact Bearings
- An application review also revealed that a larger bearing contact angle would improve axial load carrying capacity
- Trials were set up on 3 machines and bearing life increased from 15 days to 6 months
- With these results a subsequent cost saving was presented and signed by the customer for €24.096
- Customer benefited from increased productivity and reduced maintenance costs on his machining center
Product Features
- Non-contact seals provide valuable protection; reducing raceway and ball surface wear, noise and vibration, lubricant breakdown
- Time saving: Bearing mounting time 4 x faster & contamination through poor handling eliminated
- No speed reduction due to non-contact seals
- Improved spindle performance
- Operates in horizontal and vertical positions
- Sealed bearings prevent grease migration in vertical spindles, promote temperature stability and provide higher accuracy machining
- Longer grease life: extended by 50% with sealed bearings
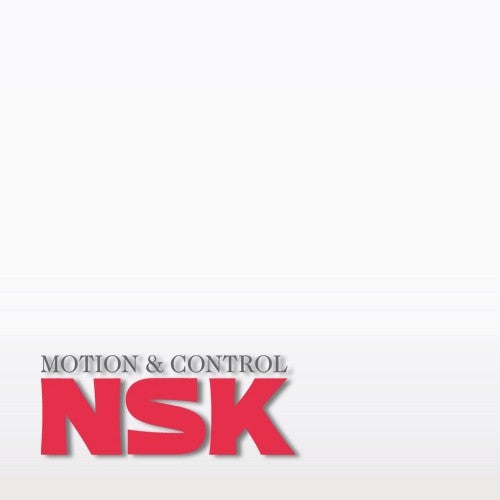
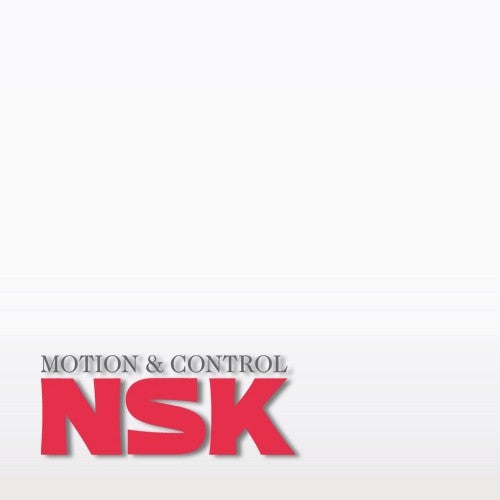
Cost Saving Breakdown
Before | Cost p.a. | NSK Solution | Cost p.a. | |
---|---|---|---|---|
Costs of lost production: Bearing life – 15 days | Costs of lost production: Bearing life – 6 months | |||
Bearing Costs: Original bearing × replacements / year × brgs. / spindle |
€27.216 | Bearing Costs: Sealed bearing × replacements / year × brgs / spindle | €3.120 | |
Total Costs | € 27 216 | € 3 120 |
Reference:SS-E-7016
Share