Success Story
Industry: Food & Beverage
Application: Oven Fan Unit
Cost Savings: € 34 907
Introduction
A leading UK Bakery was experiencing regular, unexpected production stoppages, due to premature failure of pillow block ball bearing mounted units, fitted to a high tempertaure oven re-circulation fan unit. This resulted in significant disruption to production, high downtime costs and spoilt product. NSK conducted a full evaluation of the application incl. failed bearing analysis and concluded that the bearings were seizing from excessive pre-loading and incorrect lubrication selection on installation. NSK proposed Plummer Blocks with high capacity Spherical Roller Bearings and Labyrinth seals, and recommended the correct bearing location and lubrication. This solution resulted in an immediate improvement and significant service life extension by a factor of 4.5 times.
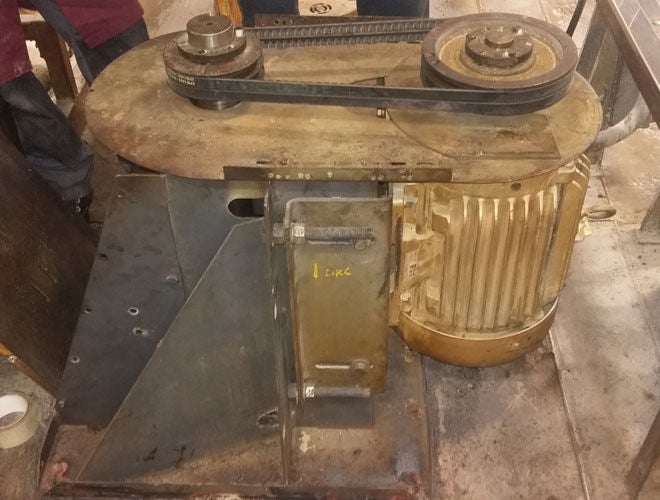
- Oven Re-Circulation Fan Unit
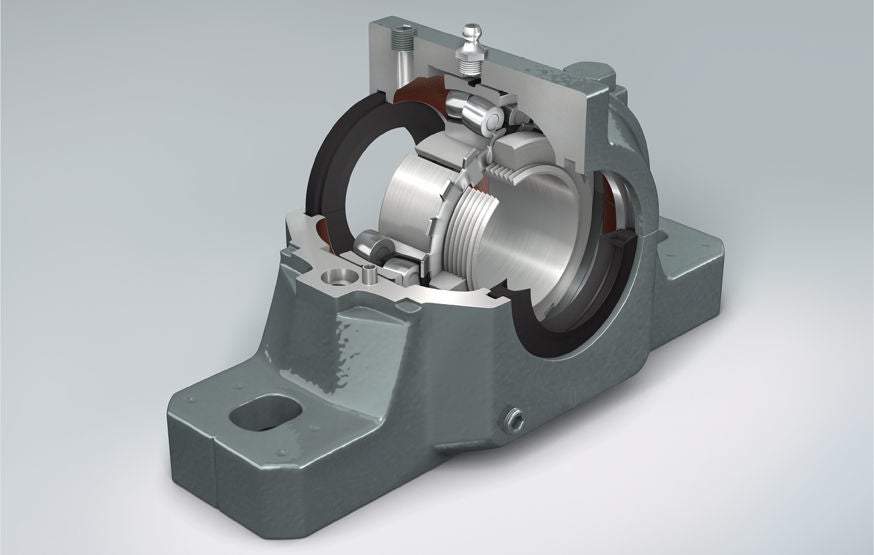
- Plummer Blocks with high capacity Spherical Roller Bearings and Labyrinth seals
Key Facts
- High temperature oven re-circulation fan unit - vertical orientation and belt driven
- Existing bearings not adequate for operating conditions
- Frequent bearing failure occuring every 6 weeks
- Bearing failure resulted in substantial machine downtime and costly loss of production
- NSK proposed SNN Plummer Blocks with high capacity Spherical Roller Bearings and Labyrinth seals, with recommendations on correct bearing location and lubrication
- Bearing life extended form 6 weeks to 27 weeks
- Large cost saving generated by improving production efficiency and equipment reliability
Value Proposals
- Following repeated and costly bearing failures the customer requested a solution to their problem on an over re-circulation fan unit.
- NSK Application Review determined the bearings had failed from excessive pre-loading and inadequate lubrication.
- NSK proposed SNN Plummer Blocks with HPS Spherical Roller Bearings and Labyrinth seals, with recommendations on correct bearing location and lubrication.
- A trial was conducted using the NSK recommendations with a 4.5 times life extension.
- This resulted in a reduction of machine downtime and maintenance costs and a significant annual cost saving
Product Features
- Equipped with 2 lubrication holes and 1 draining hole
- Solid corners in the base for locating pins
- Square shape and centre marks
- Easy assembly, easy alignment, low maintenance costs
- High rigidity (minimises deformation of the bearing seat)
- Comprehensive range of sealing & arrangements to match all needs
- Good heat transfer
- Same housing can be used with both double row self-aligning ball bearings or double row spherical roller bearings
Cost Saving Breakdown
Before | Cost p.a. | NSK Solution | Cost p.a. | |
---|---|---|---|---|
Bearing Costs: 2 bearing units replaced 9 times per year | € 14 171 | Bearing Costs: Initial installation plus 2 bearing units replaced twice per year | € 2 873 | |
Costs of lost production: € 550/hr x 5 hr replacement time x 9 breakdowns per year | € 24 750 | Costs of lost production: € 550/hr x 5 hr replacement time x 2 breakdowns per year | € 5 500 | |
Engineering Costs: 2 Maintenance Technicians x 5 hrs/breakdown x 9 breakdowns/yr | € 2 565 | Engineering Costs: 2 Maintenance Technicians x 5 hrs/breakdown x 2 breakdowns/yr | € 855 | |
Bearing Costs: Spoiled product | € 3 406 | Bearing Costs: Spoiled product | € 757 | |
Total Costs | € 44 892 | € 9 985 |
Reference:SS-E-2063
Share