Success Story
Industry: Steel & Metals
Application: Tandem Cold Mill
Cost Savings: € 2 997 568
Introduction
A Polish steel plant started production in its tandem cold mill in the 1970s. After many years of operation, a refurbishment was necessary and to reduce costs the mill consulted with a local technical university to convert the roll mill bearings from oil mist to oil bath lubrication. Unfortunately, this did not result in the expected improvements and the mill was left with a large problem. NSK engineers were consulted to review the mill design and they proposed the use of sealed clean KVS bearings with grease lubrication. These were installed and after 1 year of operation the performance excellent. As a result, the customer adopted this solution for all its Tandem Cold Mills resulting in a superior lifetime and reduced maintenance costs.

- Steel Industry
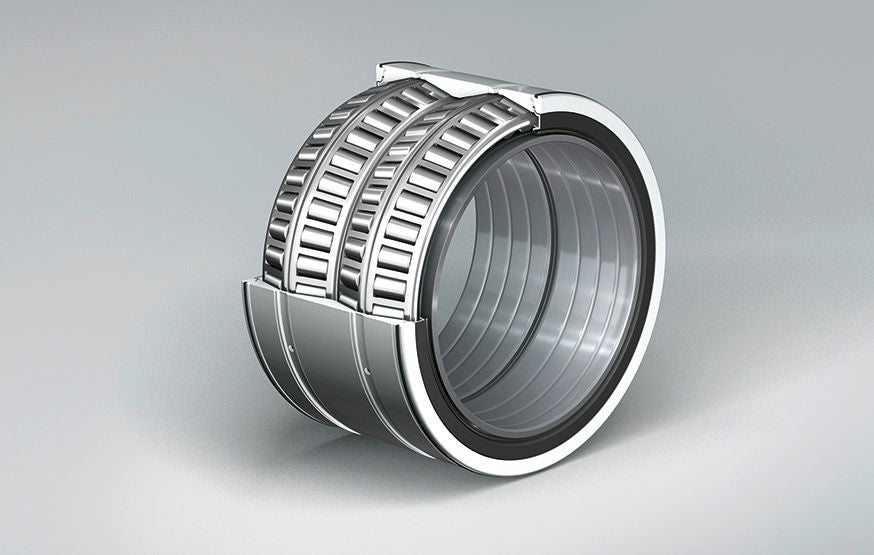
- Taper Roller Bearings - Sealed-Clean Four Row
Key Facts
- Tandem Cold Mill application
- Refurbished after many years operation
- Problem with oil-mist lubrication system
- Changing to oil bath did not bring positive results
- Installation of NSK Sealed-Clean KVS bearings produced great results
- Improved performance and productivity
Value Proposals
- Customer experienced poor performance from his oil bath lubricated bearings
- NSK were consulted and performed a design review with a proposal to adopt sealed clean KVS bearings
- A trial was conducted and after 1 year the bearings had performed very well
- Sealed-Clean 4-row Tapered Roller Bearings with grease lubrication
Product Features
- 2-4 time longer life than standard bearings
- Higher load capacity due to newly designed bearing internal geometry and special seal
- Main seal and seal holder are of a more compact design
- New type of bore seal prevents the build-up of negative pressure that can cause the entry of water through the main seals
- Special helical groove to prevent creeping on the roll neck shaft
- Newly designed bearing internal geometry - wider cage diameter
Cost Saving Breakdown
Before | Cost p.a. | NSK Solution | Cost p.a. | |
---|---|---|---|---|
Bearing Costs: 28 pcs | 75.600 € | Bearing Costs: 18 pcs | 60.030 € | |
Costs of lost production: Almost 61 working hours lost | 4.373.117 | Costs of lost production: Only 18 hours lost | 1.405.645 | |
Engineering Costs: Costs of service hours | 14.000 € | Engineering Costs: 3 times less service hours than in previous solution | 4.500 € | |
Lubrication Costs: Cost of mineral oil | 5.026 € | Lubrication Costs: Bearings equipped with preinstalled grease | 0 € | |
Total Costs | € 4 467 743 | € 1 470 175 |
Reference:SS-E-5014
Share