Bearing Maintenance Tools
Correct Mounting
Why Correct Mounting and Dismounting is Important
Up to 20% of all bearing problems are caused by poor assembly techniques.
Bearings are a key component in any moving machinery and require careful application to ensure they perform to their full potential. They have to be correctly fitted both onto a shaft and into a housing. Fitting a bearing requires special tooling in order to apply the necessary force in the correct place or by heating components to achieve assembly. These considerations are not always applied leading to the bearing being damaged during the assembly or the removal process. This damage can range from indentations in the bearing raceways to seal deformation or even bearing ring cracking. Similarly with removal, damage to the bearing and its surrounding components can be costly and cause problems with future assembly. No matter what type of damage it can be assured that the bearing will not perform to its designed life causing premature machine failure and high maintenance costs.
To overcome these problems, NSK offers a complete range of specialist tools that ensure the bearing is fitted and removed without damage. This is complemented by NSK training courses which teach best practice in using these tools and helps engineers to develop safe and efficient assembly procedures.
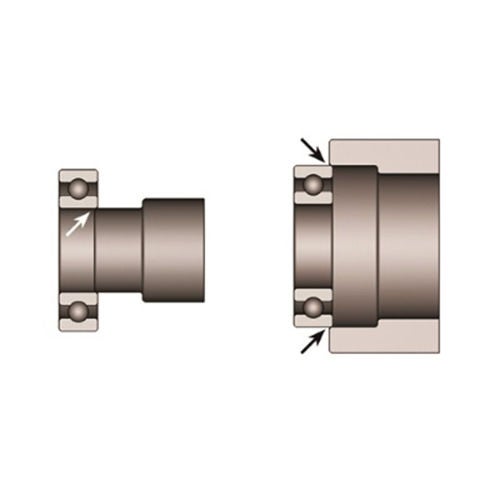
Interference Fits
For most bearings, either the inner or the outer ring (in certain cases even both) are mounted onto the shaft or into the housing with an interference fit.
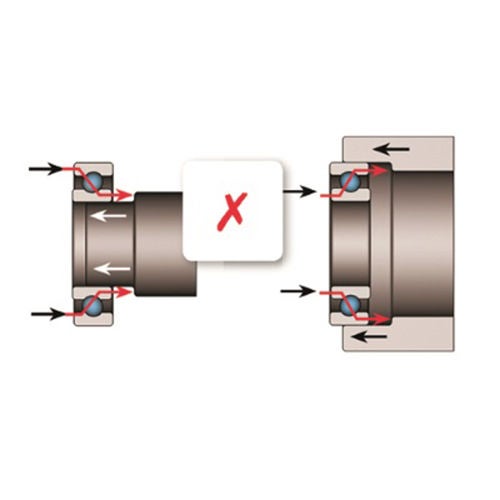
Incorrect Mounting
During cold mounting of a roller bearing, it must be made sure that the mounting forces are always applied to the ring with the interference fit. Mounting forces should never go through the rolling elements. The raceway can be damaged by application of force on the wrong bearing ring.
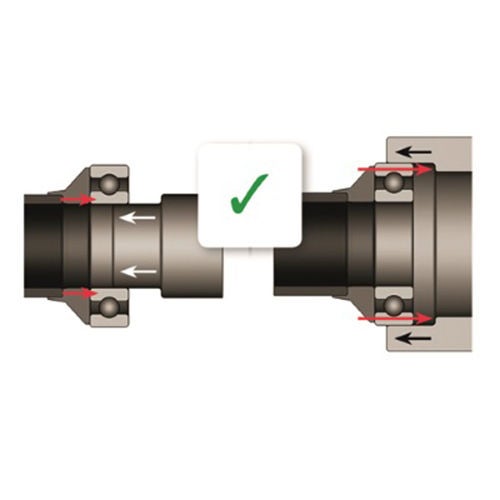
Correct Mounting
The danger of damaging raceways can be minimized by the use of the specifically designed NSK fitting tools. Raceway damages can be prevented with the correct tools.
Mechanical Tools
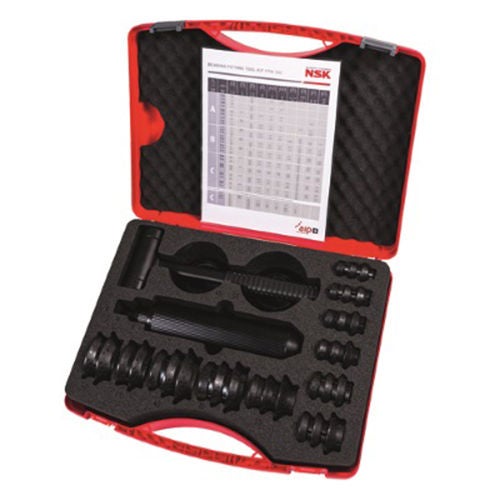
Fitting Tool Kit FTN333
Small and medium bearings are generally cold-mounted. NSK’s fitting tool kit ensures that this is carried out efficiently without damage.
- Suitable for a wide range of bearing sizes
- Impact rings made of extremely shock-resistant material
- Even transmission of force to the bearing rings due to special construction of impact rings
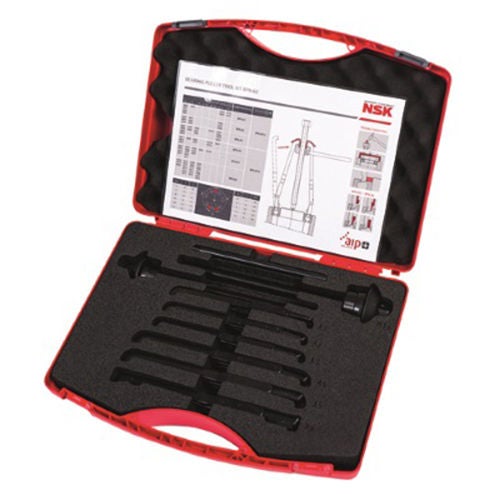
Bearing Puller Tool Kit BPN62
The puller kit can extract deep-groove ball bearings from both shafts and housings without damaging the surrounding components.
- Easy dismounting of ball bearings in blind housings
- 6 puller arm sets and 2 spindles
- Puller arms made of high quality steel
Fitting Tool Kit FTN333 - Puller Tool Kit BPN62
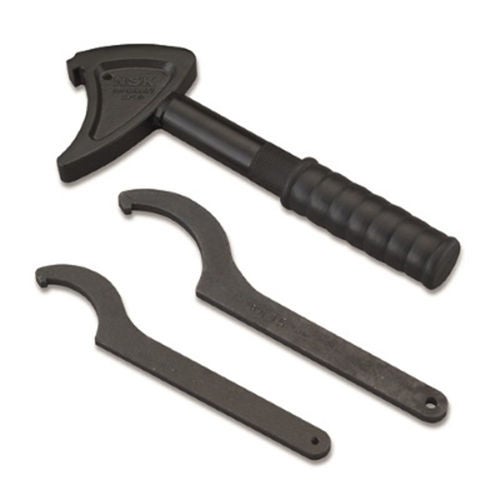
NSK Spanner Wrenches
Specially designed for locknut fitting and removal on taper bore and sleeve assemblies. These are available in standard and high-impact versions.
- Suitable for shafts, taper and adapter sleeves
- Impact range made with forged steel heads welded to alloy steel handle with easy grip rubber cover
- Impact range designed with broad head to take heavy blows and impact forces from hammers
Hydraulic Tools
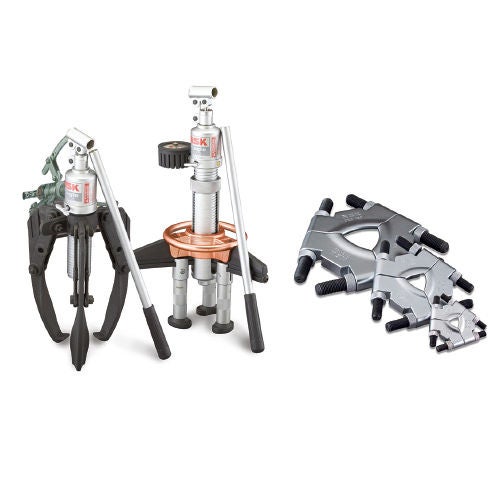
Hydraulic Pushers, Pullers and Press Plates
High loads are necessary to achieve a recommended fit between bearing and mounting surface, and NSK’s range of hydraulic pushers, pullers and press plates is ideal for the job.
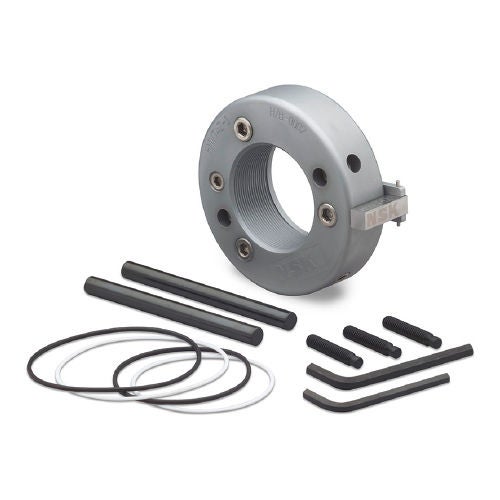
NSK Spanner Wrenches
Specially designed for locknut fitting and removal on taper bore and sleeve assemblies. These are available in standard and high-impact versions.
- Suitable for shafts, taper and adapter sleeves
- Impact range made with forged steel heads welded to alloy steel handle with easy grip rubber cover
- Impact range designed with broad head to take heavy blows and impact forces from hammers
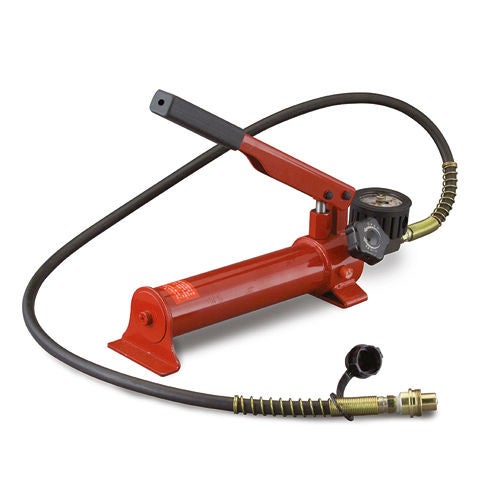
Hydraulic Pumps
NSK's range of hydraulic pumps can be used in conjunction with hydraulic nuts or for oil galleries created for removal of bearings from tapered shafts.
- Two sizes depending on capacity needed
- Pump kit includes: pump, hose, quick-disconnect, coupling, gauge, tee, extra oil and metal case
Induction Heaters
Using specially designed induction coils, NSK bearing heaters will ensure your bearings are safely and efficiently heated to the optimum temperature for easy hot mounting.
NSK offers three ranges of heaters
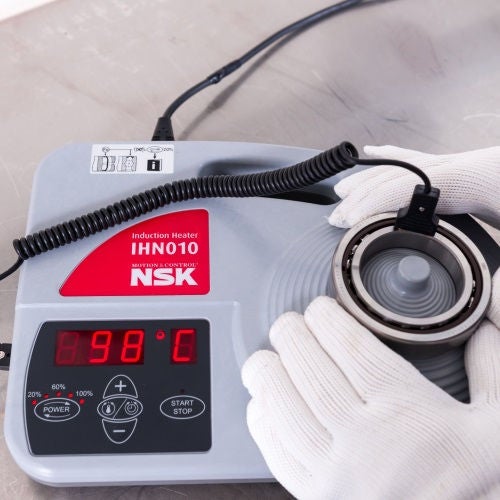
Portable Induction Heater
Portable, compact and very light (3.5 kg) Capacity 10 kg and 1.5KVA
Small and space saving, Silent operation and modern design
- Cone inductor with no support yoke required – simply place the workpiece on the device
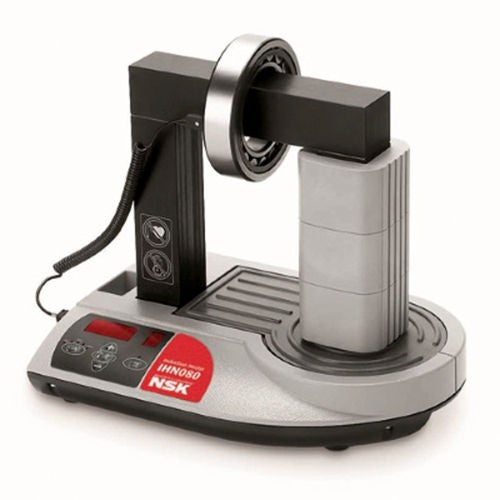
Bench Mounted Induction Heater
A range of sizes covering maximum workpiece weights from 80 kg to 300 kg
1.5 to 2.0 times faster
- Supplied with a range of yokes for different size bearing neatly stored in the base unit.
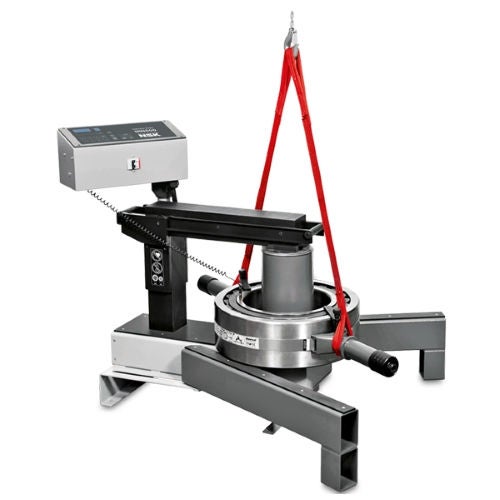
Heavy Duty Induction Heater
- Floor mounted model capable of handling workpieces up to 1200 kg
- Convenient design with sliding arm making it easy to use with heavy bearings up to 1.2m outside diameter
- Programmable control unit mounted at easy working height for use.
Induction Heater IHN010
Induction Heater IHN080
Induction Heaters - User Manuals
Belt Alignment
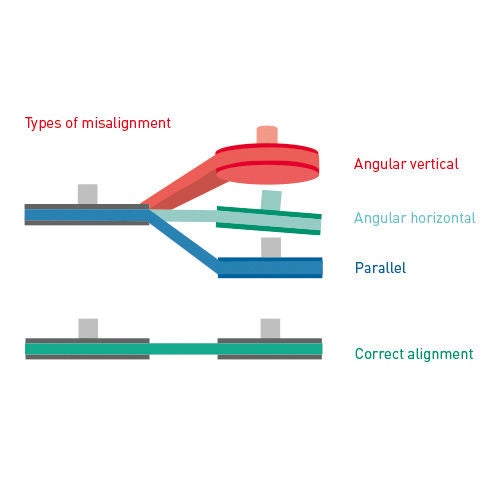
Why Belt Alignment is Important
Correct alignment of belt drives is increasingly important in an environment where machine performance and maintenance costs are key considerations. Pulley misalignment can result in unnecessary forces being applied to the machinery leading to increased wear and vibration causing premature bearing failure and thereby costly machine downtime.
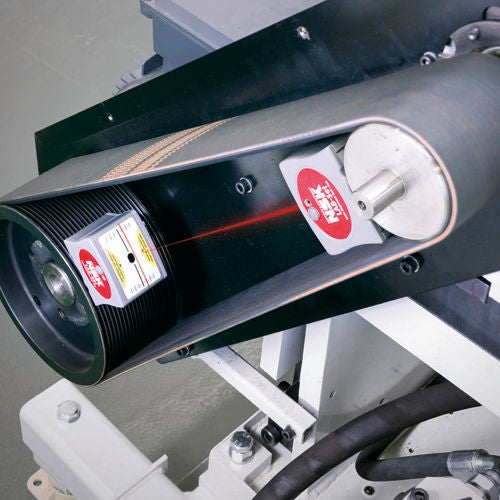
LAB-Set – the NSK Solution to All Your Belt Alignment Needs
With the LAB-Set, you are never in doubt of whether your belt transmissions are aligned or not. By using the V-grooves as reference, you will achieve precise alignment which reduces belt wear, bearing failures and vibration.
NSK’s laser alignment solution LAB-Set contains two line laser transmitters, making alignment far more accurate than single laser head types. Each set is equipped with a range of magnetic spring loaded guides which snap into the pulley grooves. This makes it very easy to mount the laser units on the pulley.
The alignment process is as easy as the mounting. Just turn on the lasers and look at the opposite mounted unit. The laser shows as a line on the target label as in the illustration to the right. If necessary, adjust your machine position until the laser lines are aligned with the centre mark. This is done for both units which ensures accurate alignment at a distance up to 6m.
What are the Benefits of Accurate Belt Alignment for You?
- Increased bearing lifetime
- Increased machinery uptime, efficiency and productivity
- Reduced wear of pulleys and belts
- Reduced unplanned downtime
- Reduced costs for component replacement
- Reduced friction and hence energy consumption
- Reduced vibration and noise
Laser Alignment Tool - Belt
Laser Alignment
Why Shaft Alignment is Important
Correct alignment of shaft drive systems is increasingly important in an environment where machine performance and maintenance costs are key considerations. Misalignment can result in unnecessary forces being applied to the machinery leading to increased wear and vibration causing premature bearing failure and thereby costly machine downtime.
LAS-Set – the NSK Solution to All Your Shaft Alignment Needs
The LAS-Set uses dual line lasers for easy set-up, even at larger distances, and digital sensors with high resolution for precise results. Additionally, a display unit that provides an icon-based, intuitive, step-by-step guide, makes the entire alignment process both straightforward and quick.
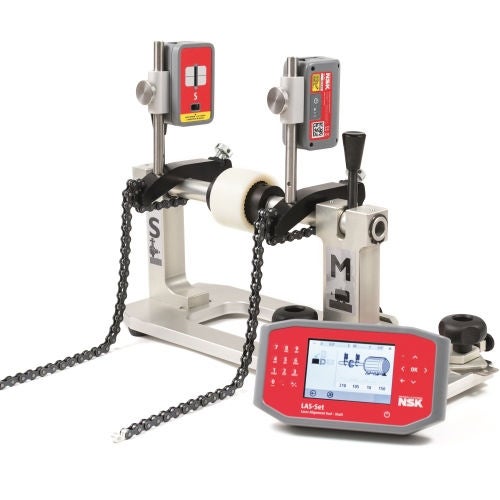
The process is simplified further by the use of wireless technology pairing the sensor units to the display. Wireless connectivity also serves to improve access and make for easy location of the display unit.
Ultimately, LAS-Set offers the capability to turn an expert task into a standard maintenance process that is simple and fast to perform, thus helping to minimise machine downtime and maximise productivity.
What are the Benefits of using the NSK Shaft Alignment
LAS-Set ?
- Simple to use with easy user interface
- Dual laser heads with digital sensors
- Built in tolerance recommendations
- Softfoot check to ensure motor is stable on its base
- Live measurements whilst adjusting with simple red/green indicator for in or out of tolerance
- Easy to save results via USB connector
Resulting in
- Increased bearing lifetime
- Increased machinery uptime, efficiency and productivity
- Reduced wear of seals and couplings
- Reduced unplanned downtime
- Reduced costs for component replacement
- Reduced friction and hence energy consumption
- Reduced vibration and noise
Laser Alignment Tool - Shaft
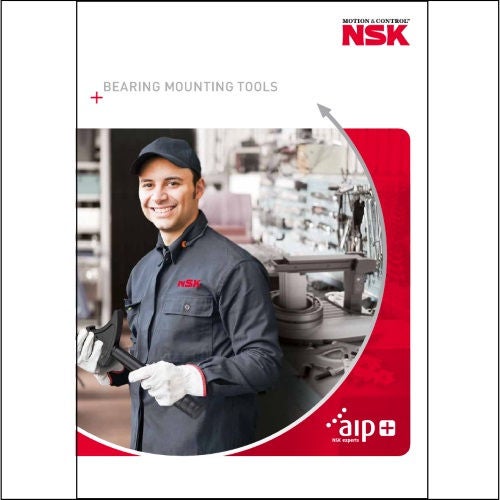
Share