Climate Change Measures
NSK’s Approach
◆Promoting CO₂ Emissions Reductions through “Create” and “Utilize” Approach
In response to the urgent issue of climate change, NSK contributes to achieving carbon neutrality across the entire supply chain. NSK works to reduce energy consumption and CO2 emissions not only during the “create” stage, when products are manufactured, but also throughout the entire product life cycle, including the “utilize” stage by customers. Furthermore, the products NSK provides contribute to the efficient use of resources by incorporating the concept of a circular economy. By leveraging its core technologies, honed over more than 100 years since our founding, NSK is dedicated to contributing to the realization of a sustainable society.
- This page outlines NSK’s activities for reducing CO2 emissions during the “create” stage, from the procurement of raw materials and components to the manufacturing and shipping of products. For information on how our products and services reduce CO2 emissions during the “utilize” stage, please visit “Environmentally Friendly Products.”
Environmentally Friendly Products
Information Disclosure Based on TCFD Recommendations
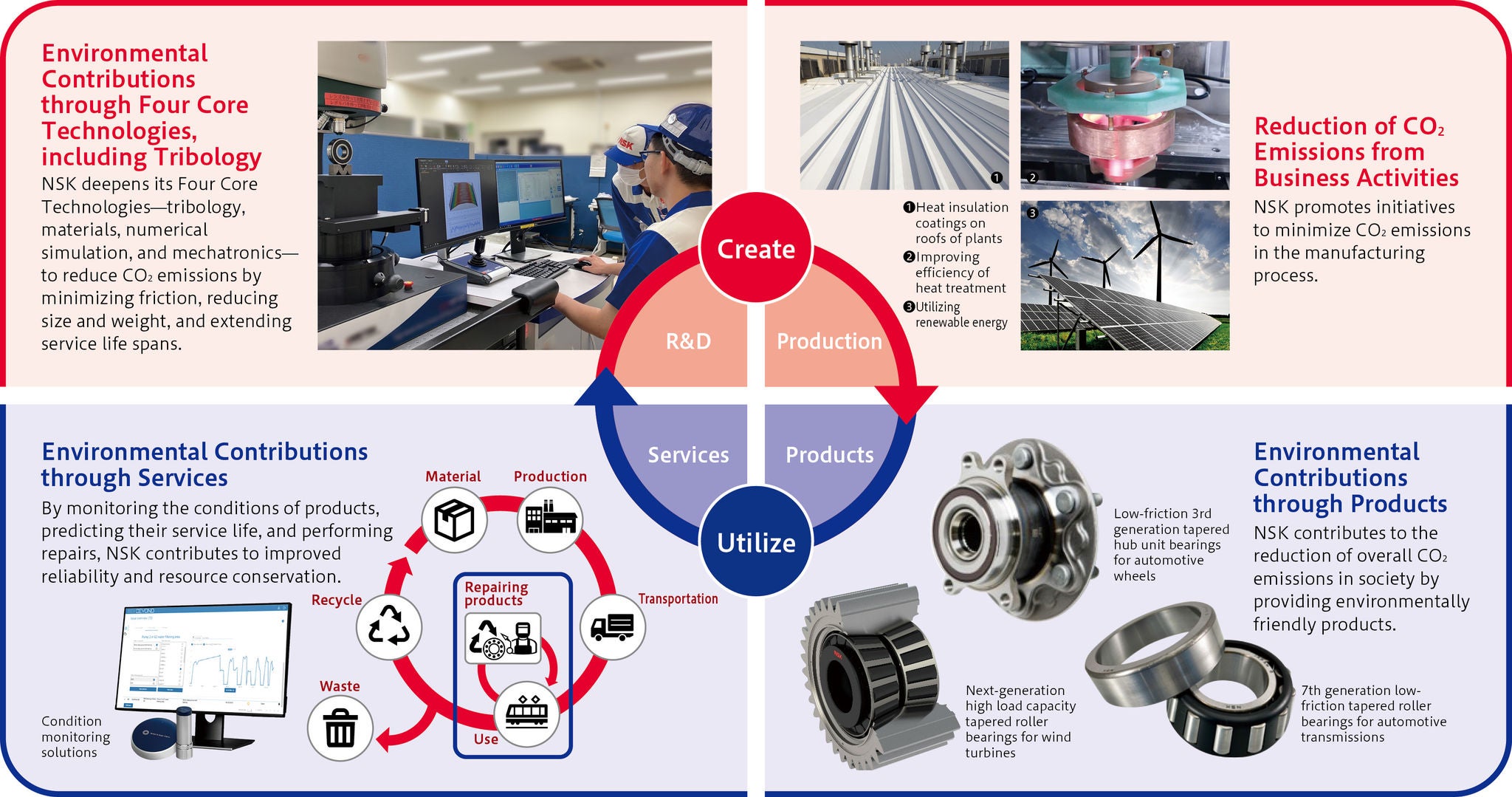
Targets and Performance
◆Mid-Term Management Plan 2026 (MTP2026) Targets, with Targets and Performance for Each Fiscal Year
MTP2026 Targets | FY2023 Targets | FY2023 Performance | Initiatives | FY2024 Targets | |
---|---|---|---|---|---|
Manufacturing, technology, offices | CO₂ emissions*: 50% reduction from FY2017 | 45.0% reduction from FY2017 | 51.7% reduction from FY2017 | (1) Promotion of energy savings and fuel conversion
(2) Production technology innovation
(3) Expanded adoption of renewable energy
◆ Mechanisms to promote measures
| 39.0% reduction from FY2017 |
Energy usage per unit of sales: 10% reduction from FY2017 | 6.0% reduction from FY2017 | 19.4% reduction from FY2017 | 7.7% reduction from FY2017 |
* Total greenhouse gas emissions (CO2 equivalent) are obtained by multiplying each type of gas by its global warming coefficient. Emission factors for electricity are variable market standards. These emission factors, which change every year, are published by power companies with which we have contracts, or are given in the International Energy Agency’s CO2 Emissions from Fuel Combustion.
◆ CO₂ Reduction Targets and Progress
- Aim to reduce Scope 1 and 2 CO2 emissions by 50% by FY2026 from FY2017 levels.
- Aim to achieve carbon neutrality for Scope 1 and 2 by FY2035.
- Aim to reduce Scope 3 CO2 emissions, which include the upstream supply chain, and contribute to the goal set by global society of net zero CO2 emissions by FY2050.
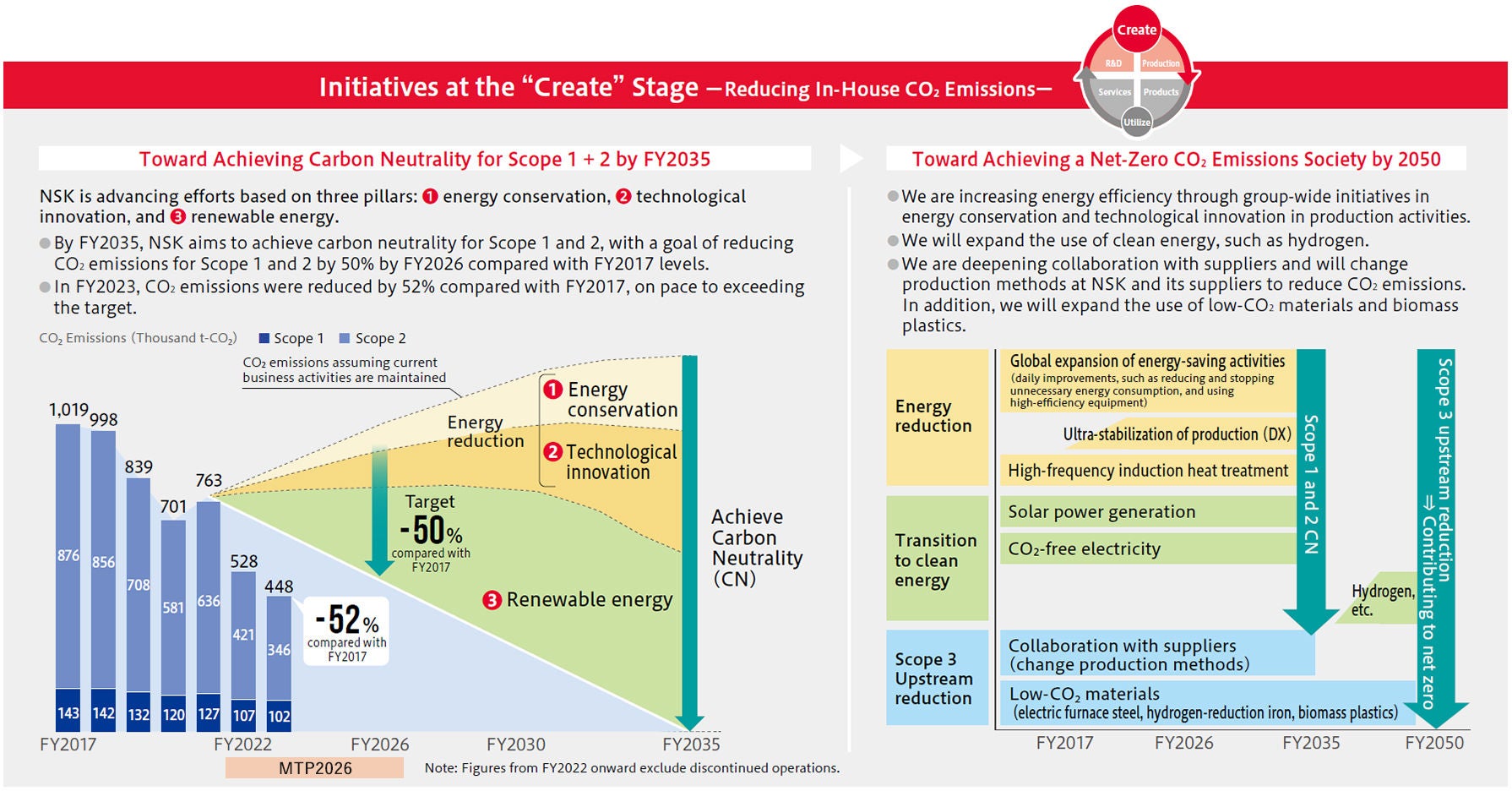
Click here for more details on NSK’s energy consumption, greenhouse gas emissions, and more.
Initiatives
◆Initiatives on “Create” Approach
Energy Reduction
The NSK Group aims to enhance (1) energy conservation and (2) technological innovation initiatives by sharing information across the entire Group and expanding activities at each site to improve energy efficiency and reduce CO2 emissions. We promote ongoing energy conservation activities and the adoption of cutting-edge technology. Since FY2017, we have set an annual target of reducing energy usage per unit of sales by more than 1% each year. As of FY2023, we achieved energy usage per unit of sales of -19.4%, exceeding our target of -6.6%.
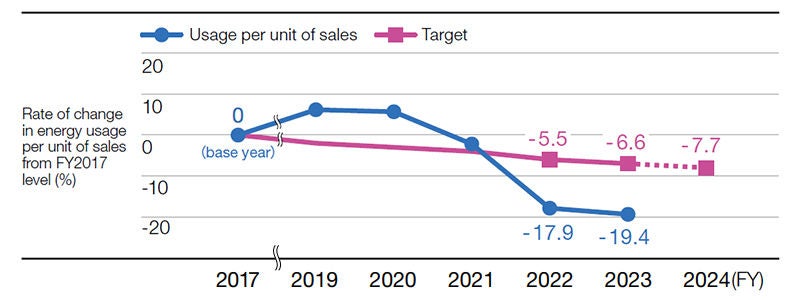
The rate of change in energy usage per unit of sales from FY2017 (base year) has been recalculated to exclude discontinued operations (steering business). Note that the energy usage per unit of sales for FY2019 - 2021 in the graph is plotted based on estimate values.
(1) Energy Conservation
NSK plants are pursuing more advanced energy management by utilizing digital tools to monitor and analyze the energy consumption of each piece of equipment. Building on this foundation, the plants are deploying energy-saving initiatives such as improving the operational efficiency of production equipment, reducing compressed air consumption, optimizing the number of compressors in operation, and enhancing the energy efficiency of air conditioning systems.
Example Initiatives
Grinding machines consume a significant amount of energy, especially the motors that rotate the grinding wheels and the pumps that circulate coolant during grinding operations. By analyzing energy consumption using its digital dashboard, the Saitama Plant identified older, less-efficient grinding machines that consumed about 40% more energy. These machines wasted energy by continuing to run even when not processing parts. Improvements were made to stop the motors when not in use, minimizing energy waste. Pump energy use was also reduced by optimizing coolant consumption to the minimum levels required.
Many production machines, which have components that require high force, such as the grinding wheel feed mechanism of grinders, are equipped with hydraulic units. Conventional hydraulic units continuously operate the hydraulic pump motor at a constant speed, resulting in wasted energy whenever high oil flow is not needed. To address this, the Otsu Plant installed high-efficiency hydraulic units that precisely control motor speed, delivering the optimal amount of hydraulic oil at all times and significantly reducing power consumption.
Saitama Prefecture is known among Japan’s prefectures for taking active steps to combat global warming, aiming to reduce its CO2 emissions by 46% by FY2030 compared to FY2013. To achieve this, the prefecture requires large-scale business sites to set and work toward emission reduction targets. The Saitama Plant is one of NSK’s largest production sites in terms of CO2 emissions and has actively pursued emission reduction initiatives. One such initiative is the conversion of its air conditioning equipment from gas to electricity. The plant’s newly installed electric air conditioning system is about four times more energy-efficient than the previous gas-powered one, leading to a significant reduction in CO2 emissions. Moreover, the electric system produces no exhaust gases, uses no water, operates stably, and requires less maintenance, thereby reducing the plant’s various environmental impacts.
Maintaining comfortable temperature levels inside large plant buildings during summer and winter is problematic due to the power consumption of air conditioning systems and the resulting CO2 emissions. To address this, the Fukushima Plant is combining inverter-controlled air conditioning with a rooftop thermal insulation coating to improve energy efficiency.
By using inverters to precisely control air conditioning operations based on indoor temperatures, the plant effectively reduces its CO2 emissions. Large air conditioning systems in the plant use five or six motors for ventilation, exhaust, and air circulation. High-precision control of each motor’s rotation speed with inverters helps lower CO2 emissions while maintaining a comfortable work environment. Thermal insulation coatings have been applied to the outer walls, their interior surfaces, and the roof of the plant. These coatings reduce the impact of outside temperatures and intense sunlight. This in turn enhances air conditioning efficiency, keeping the plant cooler in summer and warmer in winter.
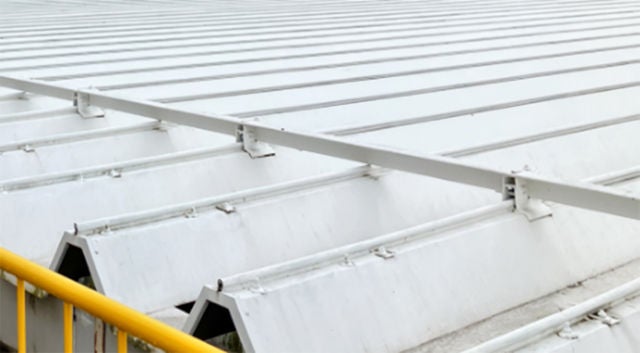
Thermal insulation coating on the roof of the Fukushima Plant
During the heat treatment process, metal components like bearing inner and outer rings are usually heated in a furnace to temperatures above 800℃ to enhance their durability. This requires substantial energy consumption, both electricity and gas. Additionally, radiant heat from the furnaces significantly raises indoor temperatures, posing challenges for improving the workplace environment and reducing air conditioning energy consumption. To address these issues, the Takasaki Plant and Haruna Plant applied thermal insulation coating to their heat treatment furnaces, minimizing heat loss. This measure not only improved the workplace environment but also enhanced heat treatment efficiency and reduced air conditioning energy consumption, leading to overall energy savings.
Compressors provide the compressed air necessary for powering production machinery in plants. However, air leaks can occur due to aging pipes and equipment, leading to greater compressor use and wasted electricity. Detecting these leaks is challenging because they are invisible and only produce faint sounds, making it difficult to pinpoint the leak locations. To solve this issue, the Ishibe Plant now uses detection devices that overlay the source of air leak noise on captured images, effectively visualizing leak locations. This technology enables rapid detection of even the smallest leaks within seconds, which were previously undetectable. Since its implementation, the number of detected air leaks doubled in FY2023 compared to FY2021, and the energy-saving effect from repairs tripled, delivering significant results.
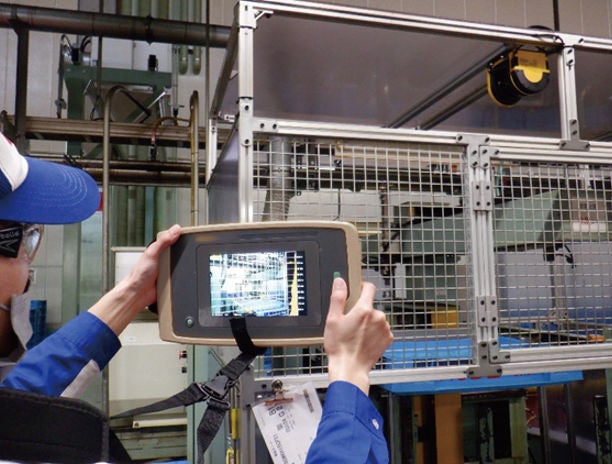
Air leak detection at the Ishibe Plant
(2)Technological Innovation
The NSK Group is reducing Group-wide CO2 emissions by adopting innovative production technologies at its plants worldwide and expanding the range of products for which these technologies are utilized.
Example Initiatives
(3) Renewable Energy
NSK is advancing its plan to switch all sites to renewable energy. The ratio of renewable energy being used to the Group’s total energy consumption increased from 21.5% in FY2022 to 34.5% in FY2023. In Europe, all sites have switched to CO2-free electricity, and the transition is progressing in Japan, the ASEAN countries, and North America. In addition, most of our factories in China have installed solar power generation systems.
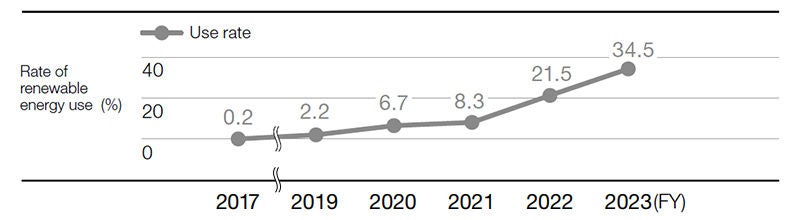
Data for FY2022 – 2023 renewable energy use rates exclude the discontinued operations.
Example Initiatives
◆Scope 3 Upstream Reductions
Example Initiatives
NSK has developed the world’s first cage made from 100% plant-derived biomass plastic. Castor bean plants, the raw material source for this biomass plastic, absorb CO2 during their growth process. Consequently, the bio-based plastic reduces CO2 emissions by 80% compared to conventional petroleum-based plastics.
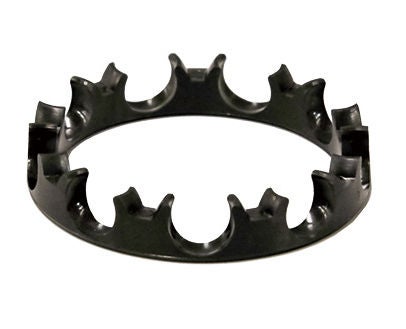
Biomass plastic cage
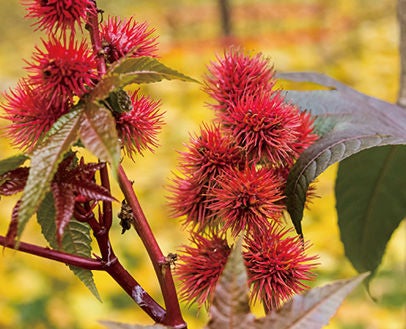
Castor bean materials