精機製品・技術レポート:クリーンハンドリング技術
1. はじめに
半導体、液晶製造装置に代表される高いクリーン度要求、およびHDDの記録密度向上などによるクリーン設備の需要拡大に伴い、クリーンルーム内におけるハンドリングのニーズが急速に高まっている。これらのハンドリングに使用される機構は、スカラ型ロボットに代表される回転機構、直交ロボットにおける直動機構、またはそれらの組合せにより構成されている。
回転機構は発塵源である駆動、支持部分をオイルシール等により比較的容易に密封できるため、高いクリーン度を得やすい利点がある。しかしながら省スペースの観点では直動機構の方が有利な場合が多く、特に昇降動作に使用されるリフタは直動機構が使用されている。(クリーンルームの床面積当たりのコストは非常に高額であるため省スペース化はクリーン化と同様に重要である。)
ここでは直動機構アクチュエータによるクリーンハンドリング技術の現状と展望について述べる。
2. クリーンハンドリングに必要な特性
図1は半導体ウエハ用リフタ部の概略図で、露光、薄膜形成等のウエハ製造プロセスにおいてウエハカセットと処理装置とのウエハ受け渡しなどに使用されるものである。このような用途において特に必要な特性を以下に示す。
(1) 低発塵
ウエハ面はダウンフローにより清浄な環境となるよう工夫されているが、周囲構造物による空気の乱れにより、リフタ部での発塵の一部がウエハ面に到達する。リフタの発塵はISO クラス2~3*)程度が要求される。
液晶用設備の場合はISO クラス4~5が必要である。
*) クリーン度は基準粒子径(評価する最小粒子径)とその粒子濃度で表されるが、以前は各国の基準が統一されていないため注意を要した。現在はISOによる統一規格が存在し、JISはISOに準じている(表1参照)。ここでのISO クラス2~3は「径0.1μm以上の粒子が1m3当たり100~1000個以下」の意味で、同じ測定値をFEDで表せばクラス1との表記になる。(FED.ST.209Dによれば、クラス1 = 0.5μm粒子1個/ft3 = 0.1μm 粒子35個/ft3= 0.1μm 粒子1000個/m3(1ft3=0.0283m3))
(2) 低振動
エンドエフェクタのウエハグリップ部は単にウエハを載せるだけの、すくい上げ方式が多い。これは、吸着方式の欠点である、吸着/開放に伴う発塵が避けられない点、チャックの開閉に時間を要する点の解消と、すくい上げ方式の弱点である振動に弱い点がアクチュエータの進歩により改善されたことによる。
ハンドリング中のウエハの位置ずれは発塵およびウエハ面にキズをつける原因となるため、あってはならない(一旦ずれるとウエハの受け渡し時にずれ量だけ押しもどされることにより再度ずれる)。すくい上げ方式のウエハに対するグリップ力はウエハ面の摩擦係数のみに依存するため振動に非常に弱い。一般的に要求される振動加速度は0.1G以下(rms)であるが、これは起動/停止時の加減速度も含めた値であり、すくい上げ方式は、おのずから動作タクトに限界を持つ方式でもある。
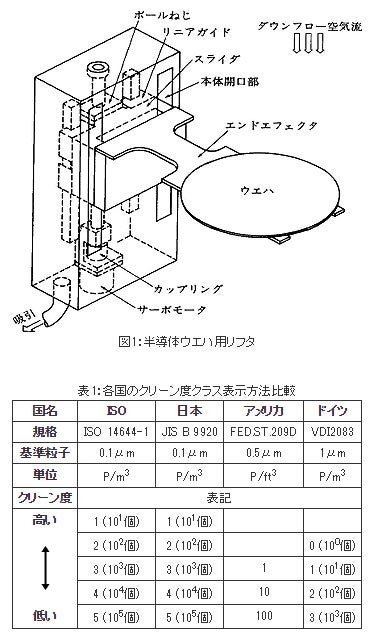
3. アクチュエータのクリーン度評価方法
アクチュエータのクリーン度を評価するに当たり少し厄介な問題は、「ワーク部のクリーン度とアクチュエータ部のクリーン度との相関が、その間の空気流の状態により大きく変動すること」および「空気流の状態は周囲構造体の影響を大きく受けること」である。このため最終的に装置全体でのクリーン度評価が不可欠となるが、一般的にアクチュエータからの発塵が多いので単体でのクリーン度(=発塵量)を明示する必要がある。
図2は当社の直動アクチュエータであるクリーン仕様XYモジュール3機種について2種類の評価方法で発塵量を測定した結果である。可搬質量の大きい順にH、M、Sモジュールとなっている。
ダウンフロー評価は高いクリーン度が必要な用途での使用環境を想定し、アクチュエータの発塵部位におけるクリーン度を測定したものである(本データはスライダ側面での最大発塵部のもの)。 一方、静止環境評価はアクチュエータをケースに収納しサンプリングの空気流と後述する吸引の空気流、およびアクチュエータの動作によって生じる空気流以外の外的要因を遮断し、アクチュエータ全体の発塵を捕らえる意図によるものである。
ダウンフロー評価方式は局部的な発塵を捕らえることにより発塵量が多く測定されるように考えられるが、実際は逆の結果となっている。これはサンプリング位置において発塵がすでに拡散されているためと推定される。測定結果が発塵部位とサンプリングチューブ端との距離や方向の影響を受けること、またその影響は、発塵箇所が局所的である場合に大きな誤差となって現れやすいことがこの方式での問題点である。発塵箇所の特定には良い方法であるが、アクチュエータの性能評価として使用する場合、条件設定に相当の注意を必要とする。
静止環境評価はこのような問題がなく信頼度の高い発塵量評価ができるため、以降の評価はこの方式によるものであり、本評価方式がNSK評価方式である。ただし本評価結果はエンドエフェクタ部でのクリーン度に対し極めて大きな発塵が測定されることに注意を要する(特に、ダウンフロー環境でのエンドエフェクタ部でのクリーン度とは全く異なる結果となる)。
いずれにしても直動アクチュエータのクリーン度としては非常に良いものであることがわかる。以下にクリーン度を高める構造について説明する。
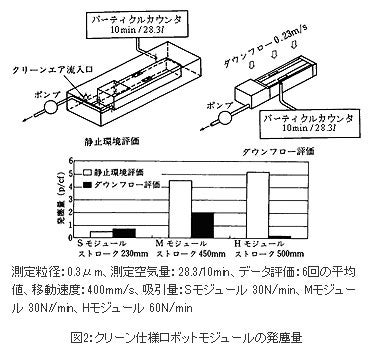
4. クリーン化構造
4.1. 基本構造
図3にクリーン仕様ロボットモジュール3機種の内、最も可搬質量の大きい「Hモジュール」の断面図を示す。左右各2個のリニアガイドベアリングにより、上下、左右、および3方向のモーメントを支え、ボールねじ(サーボモータにより駆動される)により軸方向の位置決めを行う。また、特異な構造としてスライダ開口部をふさぐシールベルトを設けている。

4.2. グリース
ボールねじ、リニアガイド、ベアリングの潤滑に使用されるグリースが主な発塵源である。図4に各種グリースのボールねじにおける発塵量を示す。フッ素系グリースは真空用途に広く使用されるが、粘度が高く発塵が少ないためクリーン用としても使用できる。時間が経過した時の発塵量は一般グリースの1/10となっている。
しかし図2との比較では発塵量が20倍に達していることが分かる。その理由は、次項に述べる吸引による効果が大きいことによる。また、本測定は密閉空間での発塵量であるが、実使用において開放された空間であればより少ない値となると考える。
LG2グリースは当社が開発したクリーン用グリースでフッ素系と同等の発塵量となっている。また、ボールねじのナット両端にラビリンスシールを設けることで、発塵量が1/10に減少することがわかる。
LG2グリースの特長は、フッ素系グリースの欠点である。「潤滑性能が悪い」「動トルクが大きい」「防錆力が劣る」点について、一般用グリースと同レベルに引き上げたことである。図5に動トルク特性を示す。フッ素系グリースが高い基油粘度によって低発塵特性を持つことに対し、LG2は基油粘度に依存しない低発塵グリースである。
また、半導体・液晶(LCD)製造装置用アクチュエータに対して高温、高荷重の用途が拡大して来ている。
そこでは発塵物質中の金属元素の存在が問題となる、これを対策してLG2と同様な低発塵特性でかつ使用温度範囲の広がった低発塵・高温・低金属元素含有仕様のクリーングリースLGUも開発され使用されている。
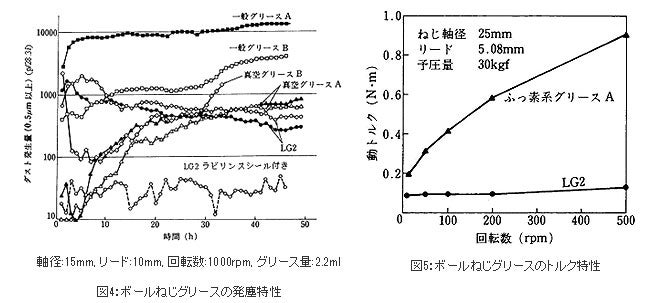
4.3. 吸引による発塵低減
真空ポンプや送気ファンにより発塵源を負圧に維持することにより外部から発塵源への空気流を作り、クリーン度を高める方法である。ボールねじナット部、リニアガイドベアリング部などを個別に吸引する方法と、アクチュエータ全体を吸引する方法がある。
前者は吸引箇所がスライダ側でかつ多数となるため吸引チューブの引回しスペースを要する、吸引箇所がグリース潤滑部と接近しているため吸引口にグリースが詰まり機能しなくなる恐れがある、といった問題点があり、後者は発塵を防ぐためには本体のスライダ開口部全体にわたり空気流を作る必要があり、その結果吸引量が多い欠点がある。
図3のアクチュエータは後者の方法によるが、開口部をシールベルトによりふさいでいる。シールベルトは両端がスライダに固定され、本体フレームの両端に設けられたプーリにより巡回する構造となっている。シールベルトと本体フレームの溝部とで形成される迷路状空間で速い空気流を作ることにより吸引量を60Nl/min(シールベルト無しに対し1/5以下)に低減している。
4.4. 内部空気の循環による発塵低減
直動アクチュエータは本体フレームに囲まれた直動部がピストンとしての作用をするため、移動方向前方の内部圧力が高くなり、ストローク端近くに移動した時にダストが外部に排出される問題(ポンピング作用)を有するが、この影響は下記により減少させることができる。
(1) 直動部断面積の小型化
直動部はリニアガイドベアリング、ボールねじナットおよびそれらとワークを結合するスライダより成っており、エンドエフェクタ固定部での剛性を確保する必要がある。これらの断面積縮小のため、図3の製品ではスライダのエンドエフェクタ固定部を最も高い剛性の得られるリニアガイドの中央に配置した。
これにより旧製品に対し、ローリング方向剛性が1.8倍に向上するとともにスライダの薄肉化により直動部断面積を77cm2から63cm2に減らすことができた。しかしながらこのポンピング作用は移動速度400mm/sにおいて151Nl/minのダストを排出しようとするもので、直動アクチュエータの高クリーン化が難しい原因はこれによるところが大きい。
(2) 本体フレーム両端の連通
スライダの移動方向後方空間は前記と逆の作用により負圧となる。よってこれを前方空間と連通させることにより前方空間の圧力を減少させることができる。多くのアクチュエータは本体フレームにアルミニウム押出し成形材を使用しており、断面は剛性の確保と軽量化のため中空部を多数有する形状となっている。この中空部をスライダ移動空間に連通させることにより容易に上記の作用が得られる。
5. 振動
アクチュエータの振動問題は2種類に大別でき、解決のための方向は全く逆となるため注意を要する。
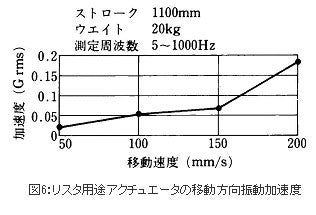
(1) 振動振幅が問題となるケース
ワイヤーボンディング(半導体チップとリードフレームとの結線工程)など、エンドエフェクタでの位置が振動振幅により定まらないことの問題で、剛性の向上、軽量化により固有振動数を上げることにより改善される。
(2) 振動加速度が問題となるケース
ウエハハンドリングがこのケースに当たる。剛性を低くすると固有振動数が下がり、振動加速度が小さくなる傾向がある。しかしながらアクチュエータ部の剛性が低い場合、離れた位置にあるウエハ部では振動振幅が拡大されるため停止位置が定まらない問題となる。アクチュエータ部においては剛性を重視、エンドエフェクタ部において振動加速度と振動振幅のバランスをとることが効果的と考える。リフタ用途アクチュエータの振動加速度測定例を図6に示す。
6. あとがき
クリーンハンドリングに対する将来的ニーズは「発塵量低減と検出粒径の小径化」および「需要拡大に伴う低コスト化」と考える。
半導体ウエハの高集積化に伴い発塵量の低減と検出粒径の小径化が同時に進行し、アクチュエータ部においても近い将来0.05μm粒子 35個/m3を要求されるものと考えている。転がり案内型アクチュエータの限界性能の追求と同時に、非接触の駆動、案内駆動方式によるハンドリングも今後需要期を迎えるのではないか。
一方、HDDの高密度化、LCD、PDP等の普及などにより組立・検査工程におけるクリーンハンドリングの需要は拡大しており、今後コスト低減のニーズが強まると思われる。しかし一般のハンドリングと異なり、クリーンハンドリングにおいてはダウンフローなどの設備面が高額となることから、アクチュエータのニーズとしては、低コスト化よりも設備を簡易化できる高いクリーン度が求められるのではないであろうか。
いずれにせよクリーン市場の拡大が見込まれる中、クリーンハンドリング技術は現在のクリーンエアの供給に依存した装置レベルでのクリーン度確保から、部品レベルの性能を競うものに成熟していくと考えている。