Detecting and Correcting Irregularities
In order to maintain the original performance of a bearing for as long as possible, proper maintenance and inspection should be performed. If proper procedures are used, many bearing problems can be avoided and the reliability, productivity, and operating costs of the equipment containing the bearings are all improved. It is suggested that periodic maintenance be done following the procedure specified. This periodic maintenance encompasses the supervision of operating conditions, the supply or replacement of lubricants, and regular periodic inspection. Items that should be regularly checked during operation include bearing noise, vibration, temperature, and lubrication.
If an irregularity is found during operation, the cause should be determined and the proper corrective actions should be taken after referring to Table 2.
If necessary, the bearing should be dismounted and examined in detail. As for the procedure for dismounting and inspection, refer to Section 5, Inspection of Bearings.
NSK BEARING MONITOR (Bearing Abnormality Detector)
It is important during operation to detect signs of irregularities early before damage becomes severe.
The NSK Bearing Monitor is an instrument that checks the condition of bearings and gives a warning of any abnormality, or it stops a machine automatically in order to prevent serious trouble. In addition, it helps to improve maintenance and reduce its cost.
Bearing Failures and Countermeasures
In general, if rolling bearings are used correctly they will survive to their predicted fatigue life. However, they often fail prematurely due to avoidable mistakes.
In contrast to fatigue life, this premature failure is caused by improper mounting, handling, or lubrication, entry of foreign matter, or abnormal heat generation.
For instance, the causes of rib scoring, as one example of premature failure, may include insufficient lubrication, use of improper lubricant, faulty lubrication system, entry of foreign matter, bearing mounting error, excessive deflection of the shaft, or any combination of these. Thus, it is difficult to determine the real cause of some premature failures.
If all the conditions at the time of failure and previous to the time of failure are known, including the application, the operating conditions, and environment; then by studying the nature of the failure and its probable causes, the possibility of similar future failures can be reduced. The most frequent types of bearing failure, along with their causes and corrective actions, are listed in Table 3.
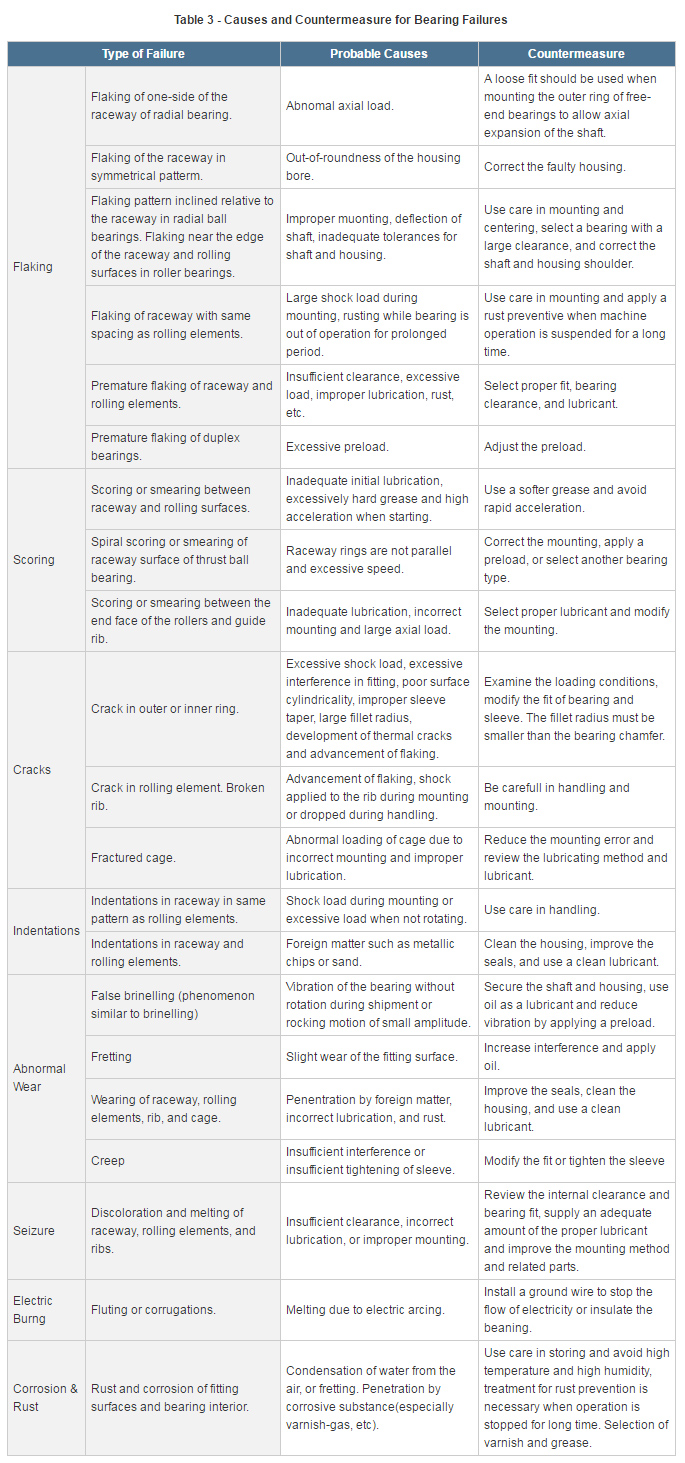
Related Pages |
---|
|